White Paper - Many manufacturers have realized significant cost savings and productivity improvements by integrating high strength additive manufacturing (AM) technology into their business, especially in support of their maintenance, repair and operations (MRO) strategy.
Guide to 3D Printing on the Production Line
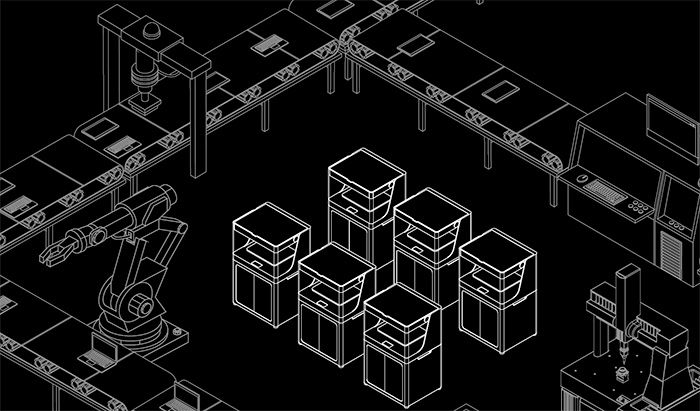
Contributed by | Markforged
IDENTIFYING OPPORTUNITIES
Additive manufacturing (AM), or 3D printing, has been hailed as the future of manufacturing for years, but despite a torrent of media anticipation, widespread manufacturing of end-use production parts via AM has not materialized. When compared to high volume manufacturing, the economics for AM are less attractive — relatively slow print times and high unit costs will never beat the massive production capabilities of high speed processes like injection molding. Instead of using it to replace existing processes for end-use production, manufacturers can leverage high strength AM to complement existing technologies in their maintenance, repair, and operations (MRO) efforts, dramatically reducing the cost of factory tooling.
There are three key identification paths to discovering the cost savings of high strength AM in your MRO toolkit. Viewing your operations through these lenses can help identify the high value opportunities in your process, which can form a strong foundation when building a return on investment (ROI) analysis of your AM strategy.
PAIN POINTS & COST DRIVERS Pinpoint root causes for process |
FACTORY APPLICATIONS Identify key components of |
MATERIALS IN MRO EQUIPMENT Determine materials in MRO |
Download this White Paper Here
The content & opinions in this article are the author’s and do not necessarily represent the views of ManufacturingTomorrow
Comments (0)
This post does not have any comments. Be the first to leave a comment below.
Featured Product
