As the manufacturing industry continues to grow and evolve, we’re seeing more focus being put on smart machines, IIoT and Industry 4.0. This is not a trend that is going away any time soon.
Top 3 Manufacturing Predictions for 2019
Gordon Styles | Star Rapid
Tell us about Star Rapid and your role in the advanced manufacturing industry?
Star Rapid is a full product life cycle manufacturer, supporting global rapid prototyping, rapid tooling and production. We offer a variety of services including, CNC machining, plastic injection molding, pressure die casting, vacuum casting and a wide range of finishing processes. Our goal is to help our customers through the entire product lifecycle from prototyping to new product introduction and beyond.
With 30 years of industry experience, I joined Star Rapid as CEO in July of 2018 to lead a two-year plan to implement fully integrated intelligent manufacturing, which is what I refer to as Industry 4.0. We are elevating Star Rapid’s business by implementing Industry 4.0 practices, continuing to develop a great team and driving sustainable growth. Prior to joining Star Rapid, I held multiple positions in general management and held senior positions in sales, marketing, business development and operations. Most recently, I served as VP of operations and quality at Multek, a division of Flex.
What are your top 3 trends for the global manufacturing industry in 2019?
As the manufacturing industry continues to grow and evolve, we’re seeing more focus being put on smart machines, IIoT and Industry 4.0. This is not a trend that is going away any time soon. In fact, it is growing exponentially. Organizations that do not begin to implement these technologies and strategies will surely fall behind. Especially in 2019, as we continue to see;
-
Industry 4.0 taking off: Industry 4.0 has been spoken about for several years now and Star Rapid has started by connecting all of our equipment to provide real time data direct from each machine. In 2019, Star Rapid expects to advance this and to take advantage of lean manufacturing and automation by doing more with less to reduce inefficiencies on the shop floor.
-
AR & VR Adoption: These technologies will be used in manufacturing not only as a training tool, but also for data management and preventative maintenance when used in tandem with machine learning and advanced artificial intelligence.
-
Blockchain: The adoption of blockchain will ensure a high level of transparency to customers on the full product life cycle from material integrity to final product.
Do you anticipate any new breakthrough technologies hitting the market next year?
Micromolding will be a technology to watch in 2019. It is one of the most unique and interesting ways to create a part. It’s important to note that micromolding is not just a slightly altered version of macromolding but requires specialized technology and expert techniques. Many designers and product engineers are excited about this process as it enables the production of high precision, micro-featured plastic injection molded parts. This is a huge breakthrough for the medical industry. Micromolding can create the tiniest of parts, such as a crowning mold, easily, whereas before it would be a tedious and daunting task.
This form of manufacturing also allows for other traditional injection molding processes at the micro scale, which is a growing demand. This enables more than just metal parts to be micromolded, but other materials such as ceramics, glass, fabrics, film or foil to other plastics.
Industry 4.0 seems to be playing a huge role in manufacturing and will continue to do so. How does Star Rapid plan to incorporate these initiatives?
Our objective is to have a fully automated, fully connected factory by August 2020. Ideally, we would like for customers to be able to tap into the system at any time and easily see where their project is within the production process. Our suppliers will also have access, which will allow for automatic replenishment driven by the system.
However, the first step is to focus on our internal processes and connect our equipment with our servers and systems to be able to take in real-time data. This will enable lean manufacturing and allow for employees to focus on less mundane tasks. This process is driven by our engineers and operators to really enable us to understand our data, rather than just connect the machines and never put our work into action. Once all our machines are connected, the next step is to focus on applying automation, artificial intelligence and machine learning.
We also plan to use AR and VR for preventative maintenance by implementing a structured approach to quality and maintenance and using cameras for maintenance efforts. We’re also examining blockchain technology to maintain the integrity of supply chains. Our goal is to take Star Rapid a step further into a bold new world with Industry 4.0.
Is Star Rapid working on any projects that you would like to talk about here?
One of our most exciting and recent projects was the opportunity to build an enclosure for the MicaSense team’s agricultural drone sensors. Our team helped the MicaSense team through the entire product lifecycle including providing design recommendations, material inspection, CNC milling, sandblasting and laser marking.
As the drone industry is growing rapidly and the opportunities are endless for this technology, we were excited to have the opportunity to help create one. Altum by MicaSense is a revolutionary 3-in-1 sensor solution for agricultural professionals who need to collect vital information on the health of their fields, vineyards and orchards. It can be carried by many kinds of industrial drones. By combining thermal, multi-spectral and high-resolution optical sensors into a single package, Altum provides high-quality data for crop analysis, pest control, irrigation and more.
Our team assisted with designing the enclosure, which is made of three parts, milled from aluminum 6061 with a T6 temper. Some of the parts were color anodized, while others were given a clear Alodine coating.
How are smart factories helping the customer journey?
Across all industries, customers expect transparency and real-time updates. Manufacturing is not excluded from this trend. Now more than ever, customers designing and building a product expect to be in-the-know on where the product is during all stages of production.
By implementing smart factories, machines are connected to servers which allows customers to easily monitor where their design is in the manufacturing process. For example, when manufacturing machines are IoT connected, a customer can log in to an online portal to easily view where their product is in the manufacturing process. This keeps the customer constantly aware of exactly what stage the product is in, without needing to constantly check in with a designer, saving both time and money.
We’ve recently implemented customized tool management and computerized tracking systems. Earlier this year, we partnered with Guhring, a German manufacturer of carbide and PCD cutting tools like drills, reamers, taps, and mills for the machining industry, to increase our speed and quality, which ultimately improves the customer journey. Guhring is able to monitor inventory control and provide real-time monitoring of tool consumption. This system creates a more efficient work flow through improved tool tracking and allows for more precise tool ordering based on anticipated future usage.
The manufacturing industry seems to be embracing blockchain. How is it implemented and what impact will it have on the sector?
While blockchain is most commonly thought of as a technology used for cryptocurrencies, such as bitcoin, it can be utilized very well for manufacturing purposes. The first step to implementing blockchain is to look at the entire IT infrastructure and examine whether the costs are worth the return on investment. Implementing blockchain technology can be costly, as it will likely require an entire upgrade to the existing IT infrastructure and legacy systems. At Star Rapid, we are continuously investing in our technology and believe the transparency and efficiency that blockchain brings to our customers is worth the investment.
We plan to use the technology to maintain the integrity of the supply chain. Data held within a blockchain is decentralized and shared across nodes, which makes it useful to create and maintain a shared and continually reconciled database. It can be used to increase transparency within a supply chain and streamline the industrial process. Blockchain in manufacturing allows manufacturers to keep an activity log of everything taking place during the manufacturing process. This will allow for the manufacturer to easily identify when there is an issue with a part or follow along the supply chain to see where a fault took place. Although the technology sounds complicated, it is actually very simple – you just have to think of it differently.
Gordon Styles is the founder of Star Rapid, a provider of rapid prototyping, rapid tooling and low-volume production services. Utilizing his background in engineering, Gordon founded Star Rapid in 2005 and under his leadership the company has expanded to 280 employees. With an international team of engineers and technicians, Star Rapid combines advanced technologies – such as 3D printing and multi-axis CNC machining – with traditional manufacturing techniques and high-quality standards. Prior to Star Rapid, Gordon owned and managed the United Kingdom’s largest rapid prototyping and rapid tooling company, STYLES RPD, which was sold to ARRK Europe in 2000.
The content & opinions in this article are the author’s and do not necessarily represent the views of ManufacturingTomorrow
Comments (0)
This post does not have any comments. Be the first to leave a comment below.
Featured Product
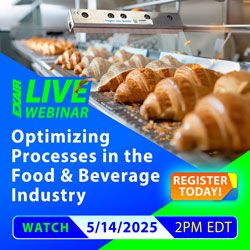