For 2019, we expect new users will continue to find their way towards additive manufacturing, and we’ll see an increasing number of companies shifting their production to AM or adding AM into the mix. New product introductions will bring success and failure...
Top Article from2019 - Polymers, Productivity and Policy: 3D Printing Trends in 2019
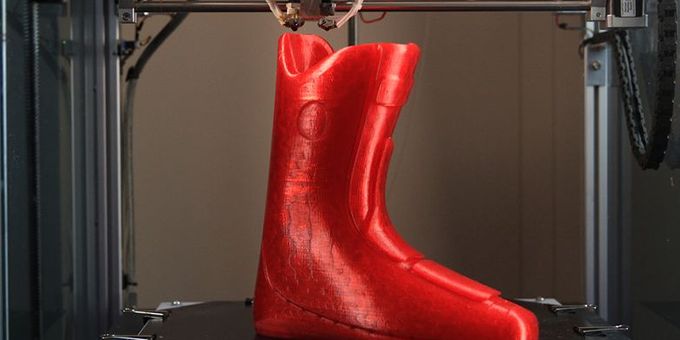
Contributed by | Materialise
3D printing is a slow revolution. But it is a revolution regardless, when you consider what the technology does: saving lives, enabling new business models, redefining how we design products. But none of that happened overnight. The revolutionary nature of 3D printing grew over decades, formed on a foundation of small but valuable steps. So where are today’s trends taking the industry in 2019? We checked in with experts at Materialise, including CEO Fried Vancraen, to find out.
Applications, not technology, will drive the 3D printing industry forward
When Materialise predicted 3D printing trends for 2018, they already shone the limelight on the application-driven approach. As Materialise observed, the industry was shifting its focus to identifying the right applications for 3D printing, rather than in developing new technologies. In 2019 that tendency will intensify, as the application-driven approach to 3D printing is likely to gain attention from the financial world.
Fried Vancraen, Materialise CEO, explains that we’ve already seen the wheels set in motion this year: “Investments are not going to machine manufacturers anymore but to companies and start-ups that apply 3D printing to create real added value in specific domains.”
This is a clear trend in Asia where governments which previously invested in technology development and 3D printing machine manufacturing are looking instead at methodologies to stimulate 3D printing consultancy and co-creation. The objective is to widen the pool of industries using 3D printing, and thereby create a market and demand for products rather than supply for a non-existing market. “Creation and stimulation of user demand is really going to accelerate 3D printing further,” according to Vancraen.
The partnership between Materialise and the industrial hub of Ulsan in South Korea illustrates this trend perfectly. Since July, Materialise is helping manufacturing companies in Ulsan to develop applications through co-creation projects combining Materialise’s 3D printing expertise with the manufacturing companies’ knowledge of their industry, market and product.
It’s not all smooth sailing, of course. When a company moves from traditional manufacturing to additive manufacturing, design engineers need to adopt a new set of rules: it’s a move from ‘design for manufacturing’ to ‘design for additive manufacturing’. Knowing what works for a design that’s intended for metal casting isn’t enough when you’re making the switch to Metal 3D Printing.
This is the main reason why many 3D printing players offer consultancy in design for additive manufacturing, to support new adopters of 3D printing with making the most of the technology for their applications.
A rise in polymer materials for 3D printing
Last year, Materialise predicted that Metal 3D Printing would get its deserved attention in 2018. This time around, it’s the plastic materials for 3D printing that have been preparing for substantial growth in 2019. A big role in this movement is being played by major material manufacturers.
Giovanni Vleminckx, a materials expert in Materialise’s research and development team, has observed a new impetus in material manufacturers like BASF to produce materials specifically for 3D printing which could take new materials out of R&D labs and onto 3D printing production floors.
“New materials for 3D printing were not being produced because they were not processable on commercially available machines. Now, large material suppliers are signaling their willingness and drive to push forward with 3D printing technology. That’s leading to a steady fast growth for 3D printing plastics.”
The rise of the application-driven approach towards innovation in 3D printing is a contributing factor. As industries identify ideal applications for 3D printing, material manufacturers will be driven to develop and certify new materials to suit those applications. In 2018, Materialise has already introduced new plastic materials to it offer: Polypropylene (PP) for Laser Sintering, and Taurus, a Stereolithography material.
This growth is especially important for highly demanding industries like aerospace and automotive that need materials with specific properties and quality requirements. Occasionally, these industries have had to weigh the design benefits and competitive advantage they get from additive manufacturing against potential downsides in cost or performance, but with new materials that trade-off won’t be necessary anymore. Industries will be able to choose the materials that best serve their applications, whether it’s for functional prototypes or series manufacturing.
The rise of manufacturing applications, as opposed to prototyping ones, is fueling a growth in materials development. The same rise is also likely to bring a new challenge: the need for materials standardization and better machine control, especially for industries with highly demanding quality requirements, such as aerospace and medical devices.
In the meantime, businesses continue to use tried and tested materials for newly identified applications. A good example is the partnership between Materialise and Airbus which in 2018 produced the first 3D-printed parts to be placed in the cabins of Airbus’s commercial aircraft, using an aerospace-certified material which Materialise introduced in 2013. The emergence of 3D-printed eyewear as a vertical was founded on an existing material, PA 12; but the real boost will come with the introduction of new materials that fit the industry’s needs.
Cases like these show that business aren’t waiting for new materials to fit their applications, but the identification of new applications can support new material development by highlighting the limits which can stand to be pushed.
Software will be the key to boosting productivity in 3D printing
There is a consensus among Materialise experts that 3D printing is reaching a new level of maturity. 3D printing started three decades ago as a rapid prototyping technology, evolved into a customization technology and now is being adopted for serial manufacturing. As industries work on integrating 3D printing into their production mix, their challenges are less about technology and more about economics. The goal is to reduce costs and to increase efficiency.
“We need to get productivity and profitability up, and costs down. Software plays a key role in that,” says Stefaan Motte, Software Vice President at Materialise.
Software makes it possible to automate tasks throughout the 3D printing process. “Automating manual labour during the preparation phase, also during and after production, is already a big help in making 3D printing scalable and cutting the costs down. This not only reduces labour but improves the efficiency of the entire process,” continues Motte.
Two more major cost factors are consumables and machine time. What if you could prevent wastage in those resources? Another way to improve productivity is through simulating the 3D printing process. Incorporating simulation into the 3D printing workflow makes it possible for production operators to spot potential build errors even before the build starts. Preventing failed builds can help reduce production costs drastically, bring down scrap rates, and increase overall profitability.
Technology-neutral interconnectivity, not proprietary solutions
Leading manufacturers in the automotive, aerospace and consumer goods industry are turning to 3D printing for its design benefits in existing verticals. However, there’s much more potential to be exploited in the global manufacturing market, currently valued at $12 trillion.
For 3D printing to unlock that potential and claim a bigger share of the $12 trillion manufacturing market, the 3D printing industry needs offer interoperability and technology-neutral solutions. If industrial manufacturers want to be serious about adopting 3D printing as a complementary manufacturing technology for final products, they simply cannot afford to be locked into proprietary solutions that limit their flexibility and choice.
“If we, as an industry, want to increase the adoption of 3D printing, we need to work together to provide more control, more choice in materials and systems and ultimately lower cost,” explains Fried Vancraen.
The same line of reasoning led earlier in 2018 to Materialise’s strategic alliance with BASF, the largest chemical producer in the world, which intends to drive growth in the 3D printing industry by promoting a more open market model. The combination of our software and the expertise of BASF in chemicals will accelerate the development of new applications and create new business opportunities.
Governments will get more involved
We have seen 3D printing emerge as a discussion point in governmental environments, says Bram Smits, Public Policy Officer at Materialise, and this can be expected to increase significantly in 2019. This rise is a signal that 3D printing is gaining importance in society and is freeing itself from the label of a prototyping technology.
“It hasn’t always been easy for governments to see the bigger picture, because the term 3D printing has been used for everything from rapid prototyping to serial manufacturing,” explains Smits. “That has made it difficult for governments to estimate the potentials and risks of 3D printing for citizens and what exactly they should seek to empower through policymaking.”
The main concerns for policy are the regulation of intellectual property and product liability. Underneath this is the concern that 3D printing could do to the physical object what the internet has done for music and movies: change business models and shift all the value to the digital file.
“3D printing will disrupt supply chains but governments overestimate how much of the value is on the digital file. A part of the value will shift from the object to the CAD file and we need to think how we regulate these files,” says Smits.
The card that the 3D printing companies decide to play is crucial for the future of 3D printing and how it will impact people’s lives. “The industry should get involved and talk to governments and explain what the technology can do, and what it can’t do and will never be able to do. With this we can create a safe and good regulatory framework that protects their citizens, designers and patients,” concludes Smits.
Conclusion, in the words of Fried Vancraen
“For 2019, we expect new users will continue to find their way towards additive manufacturing, and we’ll see an increasing number of companies shifting their production to AM or adding AM into the mix. New product introductions will bring success and failure, and both are key for this steady growth, with the learning opportunities that they present. We don’t expect 2019 to become an inflection point in the history of AM, but the stage is set for another year of incremental steps towards an additive future. The slow revolution continues.” – Fried Vancraen, Materialise CEO.
Find more info in the Materialise Blog
The content & opinions in this article are the author’s and do not necessarily represent the views of ManufacturingTomorrow
Comments (0)
This post does not have any comments. Be the first to leave a comment below.
Featured Product
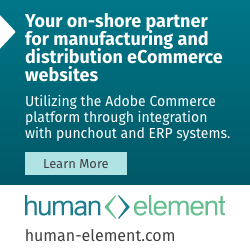