Partnering with tech companies whose investments in the Fourth Industrial Revolution are aimed at streamlining manufacturing processes is the shortest, most reliable route to your company winning the future.
Best Practices for Production in the Age of Advanced Manufacturing
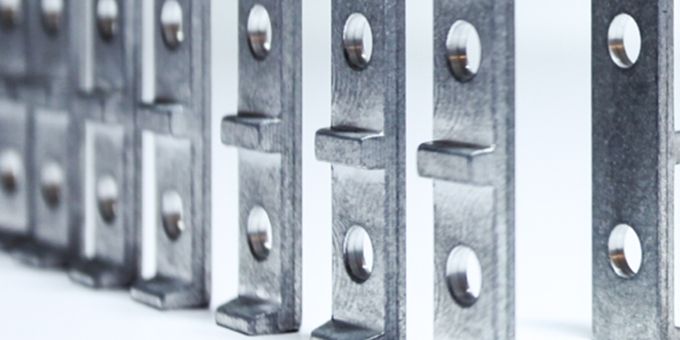
William Krueger | Xometry
We may cram 0s and 1s into everything we make in order to improve performance and customer experience, but one fact remains: What we make is real, even as the processes of making seem to become less so with each passing day.
There’s been a lot of chatter the last few years about all the ways technology is poised to dramatically alter and challenge the manufacturing landscape. While it’s true that the rising tide of robotics, automation, the Industrial Internet of Things, and AI are fast-tracking us all into a new reality, at the end of the day, one truism from our grandfathers’ manufacturing days still holds firm.
Regardless of whether we crowdsource our designs from people scattered around the globe, upload our part file to an online CNC machining platform that then automatically matches it to a CNC milling machine somewhere in Idaho or make use of in-house 3D printing, manufacturers are still in the business of making real, tangible, physical parts, components and products. We may cram 0s and 1s into everything we make in order to improve performance and customer experience, but one fact remains: What we make is real, even as the processes of making seem to become less so with each passing day.
In this dawn of the Age of Advanced Manufacturing, companies taking advantage of bleeding edge technologies to win market share and cut costs must proceed in a sort of Limbo. With one foot in the past and one foot in the future, the trick is to leverage those technologies that can yield real benefits, not just those that get the most attention.
If you’re wondering how to deduce which is which, you’re not alone, and while we don’t have a crystal ball at Xometry, as a company working to develop technologies, software and algorithms that make manufacturing easier, faster and less risky, we’re trying out and testing a lot of different options, many of our own making.
Here, then, is our companion piece to the Best Practices for Prototyping in the Age of Advanced Manufacturing, focusing this time on the best practices for production.
Keep it Streamlined
There are reasons some technologies stick around and others don’t. Besides meeting a need or solving a problem, the most resilient technologies are also almost always the easiest to use. In the world of manufacturing and CNC precision machining, ease of use has been undervalued for far too long. Given shrinking time-to-market considerations and rising customer expectations, however, streamlined processes are seeing their stock rise.
As new tech clamors for attention, it’s essential to cut out the noise in order to keep perspective. Will this new tool make work easier for your team or not? Is the learning curve reasonable enough that current projects and plans won’t be derailed? Is this tool well-conceived enough to evolve and grow in changing times? The best technology — whether it’s a big data application or smart tooling for CNC lathes and mills — won’t further complicate already complicated processes. Don’t be tempted by the promise of amazing outcomes alone. If the tech you’re courting isn’t easily applied and leveraged, chances are good it won’t yield the results you’re after.
New tech should help you innovate faster and better. It should help cut or control costs. It should let your company work at the pace of 21st-century markets. We think it should also be so easy to use that it practically runs itself, or you’ll end up squandering time and money in the pursuit of time and money, and nothing about that makes any sense.
Solve Business Problems, Not Tech Problems
New tech is sexy. We know. We have Instagram, too. But, when you’re a manufacturer fighting for market share, giving in to the siren song of the bang in lieu of the buck is a foolishness that will put you out of business. So don’t do it. Snazzed-up applications in the time of cheap and powerful tech are a dime a dozen. Unless they help you address actual business problems, however, they’re unlikely to help you solve actual business problems. For anyone running production for CNC machined parts and components, attempting to “solve actual business problems” means making use of applications that, at the very least, can get you into production faster at a price that’s competitive without sacrificing any quality.
“If the tech you’re courting isn’t easily applied and leveraged, chances are good it won’t yield the results you’re after.”
Speed. Quality. Cost. Managing procurement, while achieving these three seemingly mutually exclusive manufacturing gotta-haves has rendered many a supply chain errant and obsolete. Popular wisdom and quantifiable data have historically argued that the best you can do is two out of three. In the Age of Advanced Manufacturing, does that wisdom still hold?
For most manufacturers, the answer remains a woeful, “Yes.” Between sourcing quotes to get a good price and vetting suppliers in order to ensure production, Time — be it two weeks or two months — inevitably slips by. Forego your due diligence in quoting, and you may get high-quality parts fast, but your margin will disappear even faster. Skip the vetting stage, and you’re likely to end up with an inexpensive and quickly produced part you’re not even able to use. If ever there were a business problem to solve, this is it.
So, let’s solve it, ok?
Leverage Data for Accurate Pricing
Pricing, costing, shipping and materials data exists. It is now possible for anyone to know what something costs to make and how much people are willing to pay to get it — so long as enough inputs, processing power and data science is being wielded in the pursuit of that knowing.
The digital world — for all its massive, unfathomable size — is still a lot more measurable than the physical world. Thanks to the overlap of sensors, cloud computing, decades of digital data collection, and the World Wide Web, few mysteries like pricing need to persist.
Already, data-driven, fair market pricing is available through online CNC machining and 3D printing platforms. What that means is: Continuing to use the RFQ is nothing more than an anachronistic and unproven way of trying to drive down a price, while wasting time. Production in the Age of Advanced Manufacturing demands more.
Go Distributed...
The same holds true for the time and effort spent on supplier vetting. Far too many manufacturing companies only vet the suppliers they need for the production they’re currently running. Besides the delay in time-to-market that vetting-as-you-go requires, if anything changes or a supplier fails, this approach ensures a manufacturer will lose even more time trying to recover.
The ubiquity of cloud computing coupled with sound data analysis has rendered traditional methods of finding and vetting suppliers moot. There are tens of thousands of machine shops across the United States, and at any given time, most of them have machines sitting idle. By accessing a connected network of CNC machine shops, procurement managers can make sure that if the sky falls in Florida, they’ve got machines at the ready to put work on in Oregon. Likewise, should demand ramp up, increasing a production order from 100,00 to 1 million can happen without missing a beat — an unheard of feat even 10 years ago.
Known as distributed manufacturing, relying on a dispersed and distributed network of suppliers can save a tremendous amount of time, increase overall manufacturing processes and capabilities, allow for easy scalability and mitigate risk all at the same time. In other words, it’s an approach to manufacturing that uses tech to solve actual business problems.
...So Long as It's Qualified
Of course, utilizing a distributed manufacturing network is only a good idea if every shop on the network in question has been prequalified. Saving time and cutting costs is only admirable if quality doesn’t suffer, so be sure to choose a CNC machining network that takes qualification seriously.
Given that most machining networks are accessed online and manufacturers won’t be dealing with individual CNC machine shops directly, it can be tricky to tell which networks are serious and which networks are “serious.” Here are some quality-related questions to ask of a distributed network that will help you separate the wheat from the chaff:
- Do you have a defined and well-articulated quality control audit in place?
- What certifications do your suppliers have?
- Do you conduct site visits?
- How do you use data to improve quality?
- Do you have ways for suppliers to improve?
- Do suppliers provide first article inspections?
- What guarantees are in place in case there are problems with my parts?
At the end of the day, quality parts and components are the foundation of everything your company makes. In your tech-fueled quest to cut costs and save time, be sure you don’t sacrifice quality. You don’t have to, and the fallout from doing so could be the end of a lot more than just your job. As recalls and scandals (GM, Takata, Johnson & Johnson) have proven over the years, emphasizing profits and speed over quality can cause real harm to real people. Leverage the tech that won’t tempt you or anyone on your team to cut corners by leaning on tech applications that are forward-thinking and people-centered enough to ensure speed and competitive pricing don’t undercut quality.
Partner Up
Finally, don’t try to maneuver the changing landscape alone. In addition to how downright heady technological advancements are getting, tech is changing so fast that what was true today might not be true tomorrow. When faced with negotiating a powerful and quick-moving current, neither jumping in and hoping for the best nor delaying the jump in order to spend time trying to achieve Michael Phelps-like abilities, are sufficient. Instead, find a buddy — preferably one who can swim like Phelps and breathe underwater like Kevin Costner in Waterworld.
Manufacturing has always been an industry built on partnerships, whether those partnerships were between workers and unions, CEOs and shareholders, supply chain managers and suppliers or steelmakers and designers. As tech rewrites the rules and the world, partnership has become even more vital.
Leveraging the technologies of the Fourth Industrial Age — cloud computing, sensors, big data, analytics, deep learning, wearables, augmented reality, etc. — isn’t something your average CEO, factory foreman or procurement officer will be able to do unless a tech-savvy partner has pioneered a path. In much the same way that most of us are unable to diagnose and treat our own illnesses without the guidance of a knowledgeable and accessible doctor, few of us have the education base, training or skill sets to make proper use of today’s innovative tools.
Partnering with tech companies whose investments in the Fourth Industrial Revolution are aimed at streamlining manufacturing processes is the shortest, most reliable route to your company winning the future. While it can feel overwhelming to sort through the glut of options — there seems to be no shortage of companies, technologies, people and applications out there claiming they can solve all your manufacturing problems — take heart. Some of them actually can.
Find out more about how partnering with Xometry for CNC machining, injection molding, urethane casting, sheet metal, or 3D printing production can improve your work, streamline your life and save you time and money.
This blog was originally posted on MakeTime February 24th, 2017 and has been updated and re-posted as part of the MakeTime and Xometry Merger.
The content & opinions in this article are the author’s and do not necessarily represent the views of ManufacturingTomorrow
Comments (0)
This post does not have any comments. Be the first to leave a comment below.
Featured Product
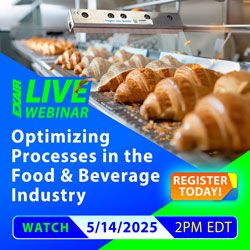