Urethane casting is a manufacturing process for making prototype and low-volume parts by using a silicone mold to form urethane parts. The parts are made out of materials that are plastic-like or rubber-like.
Three Advantages of Urethane Casting
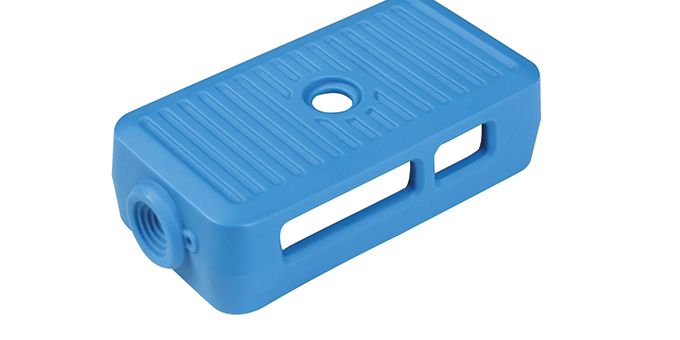
Denny Scher | ICOMold
Urethane casting is a manufacturing process for making prototype and low-volume parts by using a silicone mold to form urethane parts. The parts are made out of materials that are plastic-like or rubber-like.
The process can be ideal for quantities up to about 25 parts, and it has several advantages over other plastic manufacturing processes like injection molding and additive manufacturing (3D printing): It is fast, inexpensive, and produces high-quality parts.
Speed
The urethane casting process is very fast because the silicone molds used to make parts via this process are created very quickly, especially compared to the hard tooling used in injection molding. It is ideal for low-volume production, when quantities do not justify investment in injection mold tooling.
If the plan is to injection mold a large quantity of parts, but some are needed immediately, then urethane casting is a fast method to obtain first-run parts made before the production tooling is ready.
It’s excellent for testing product design, for one-off products, or for testing market or consumer responses to a new product. With such a quick turnaround time, urethane casted parts can bring a project to its next level for end-user testing or short-run production. It can give a company a first-to-market advantage.
Cost
The liquid poured and cured silicone molds used for casting urethane are much cheaper to produce compared to creating injection mold “hard” tooling.
To put it in perspective, a casting project might be hundreds of dollars, compared to the thousands of dollars it would be for a comparable injection molding project.
The best method of producing parts – urethane casting, CNC machining or injection molding – will be determined by part quantity. For prototypes and low-quantity parts, urethane casting provides a great value because the cost is very low, yet the quality of the parts is very high.
Quality
The cast urethane process can use a variety of formulations to produce parts that are soft or hard, colored or transparent. The silicone molds provide excellent surface finish detail and can accurately mimic production textures.
In addition, parts can be over-molded, have inserts incorporated into them, and have post-process treatments like painting.
Urethane casting produces parts with physical properties on par with injection molding, and the parts are structurally superior to their 3D printed counterparts. 3D printing - despite continuous improvements - still has material and structural integrity limitations. Urethane casting, in contrast, produces high-quality, robust parts.
About Denny Scher
Denny Scher is the Marketing Manager for ICOMold, a custom digital manufacturer with customers worldwide in a variety of industries. ICOMold provides custom plastic injection molding, CNC machined plastic and metal, and urethane casting.
The content & opinions in this article are the author’s and do not necessarily represent the views of ManufacturingTomorrow
Comments (0)
This post does not have any comments. Be the first to leave a comment below.
Featured Product
