Besides the freedom of design, 3D Printing has two crucial advantages for manufacturers: short lead times, and cost-effective mass customization. These advantages allow manufacturers to realize entirely new business models backed by digital supply chains
Talking 3D Printing in Manufacturing with Materialise
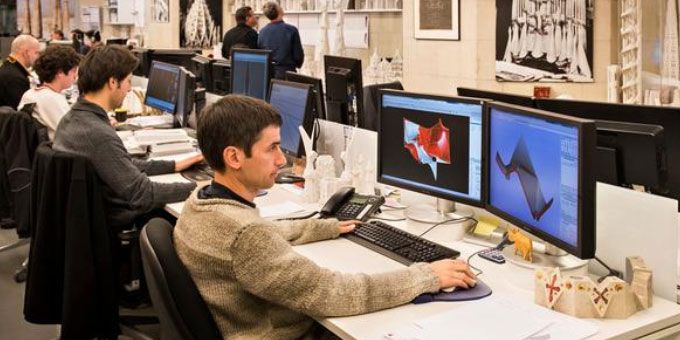
Contributed by | Materialise
Tell us about Materialise and what the company does.
Materialise was founded in 1990 by Fried Vancraen and offers 3D printing software and services. The company combines a large group of software developers with one of the largest Additive Manufacturing facilities in the world, equipped with more than 160 printers. They are continuously innovating the technologies behind 3D printing, which translates into more than 200 granted patents and 180 pending patent applications.
“Our mission is to innovate product development that results in a better and healthier world, through our software and hardware infrastructure, and an in-depth knowledge of Additive Manufacturing,” explains Fried Vancraen, CEO of Materialise.
Materialise’s software suite, better known as the Magics 3D Print Suite, includes industry-leading data preparation and design optimization tools, programs to integrate 3D printing into production environments, and software and control systems used by machine manufacturers to better bridge the gap between applications and 3D printers, allowing companies to meet the highest standards of the most demanding industries.
How are manufacturers changing to adjust to new 3D Printing and additive manufacturing technologies?
Besides the freedom of design, 3D Printing has two crucial advantages for manufacturers: short lead times, and cost-effective mass customization. These advantages allow manufacturers to realize entirely new business models backed by digital supply chains and on-demand manufacturing.
The eyewear industry is one example that has made great use of these two benefits, but to take another example, the footwear industry is not far behind. Our collaboration with RS Scan for customized Phits insoles has already shown how individually tailored orthotics are well within reach today, and we worked with Adidas two years ago for the highly publicized Futurecraft project with 3D-printed midsoles. We also have an ongoing project with Tailored Fits, a Swiss startup that makes ski boots, for customized insoles that dramatically improve comfort and performance.
Ski boot insole: a project by Materialise and Tailored Fits
As for industrial goods manufacturers, production tools are a less often talked-about aspect of 3D Printing which can offer huge cost savings and efficiency gains. Our customer Philips Lighting realized a cost savings of €89,000 a year with reinvented production tools, while a food processing OEM uses 3D Printing for mass customized nozzles.
Production of Philips Lightning
How does a manufacturer determine if the products they make will benefit from the use of 3D Printing?
At the product-level, we refer to certain ‘drivers’ for 3D Printing, a few characteristics that make a product or a part better suited for 3D Printing than conventional manufacturing technologies. One major example is complexity: when you want to design a part with internal channels, or with integrated hinges, conventional technologies won’t be very helpful. This freedom of design can be used for functionality — as in the previous example — and also for aesthetics, as the eyewear industry has already shown. Three other key ‘drivers’ are lead time, cost reduction, and short series.
Our most successful projects benefit from more than one of these factors. For instance, we work with aerospace company 328 Support Services GmbH to manufacture end-use plastic parts for the Do328 fleet of planes. These are after-market spare parts, so the volumes are low. Conventional manufacturing would force 328 to invest in tooling as well as storage space for the production tools and the parts themselves. With Additive Manufacturing, 328 doesn’t have to run the risk of obsolete parts or storage costs.
Generally speaking, 3D Printing is ideal for any manufacturing project with high value and low volumes. One example of that is any project involving customization. Since 3D Printing doesn’t need prior tooling, and encourages profitable short series, design upgrades can be put into production immediately, giving a brand a better chance to respond to market demands and trends.
Let’s say I am a small manufacturer, what are my main concerns when implementing 3D Printing?
AM requires a change in conventional design principles, in order to reap the full benefits of 3D Printing. Mistakes arise when new users attempt to apply conventional design principles to AM, rather than designing with AM in mind. As with introducing any new process into an existing production line, that initial investment required to develop a new design and engineering approach for additive manufacturing can be a barrier. As AM continues to grow more affordable per cubic centimeter and more printable materials enter the market, particularly for Metal 3D Printing, that barrier will continue to disappear.
Where do you see the role of 3D Printing in Manufacturing now and 5 years from now.
Additive Manufacturing is a fast-paced world, and innovation is constant. The industrialization of 3D Printing is well under way, with increasingly widespread adoption of 3D Printing for serial production even in some of the toughest manufacturing environments. That dictates some of these trends, notably the demand for shorter lead times and more versatility in materials.
As 3D Printing enters serial production in industries like automotive, aerospace, and consumer goods, 3D Printing is faced with the challenge to meet the benchmarks of those industries. That means the new trends in Additive Manufacturing are geared towards ensuring and improving speed, reliability, repeatability and transparency in production. All of those parameters are visible and crucial to consumer goods like eyewear, where design iterations are fast, they’re constantly pushing the boundaries of what is possible with 3D Printing, and they have to be produced with exacting precision and consistency. Extraordinary technology also needs extraordinary software. Without decent software, you can’t prepare your designs for 3D printing and may experience multiple expensive build crashes. That’s why we developed a versatile software platform that can support the needs of manufacturers in every step of the 3D printing process.
3D printing experts working on Sagrada Familia prototypes using Materialise’s famous Magics software.
The content & opinions in this article are the author’s and do not necessarily represent the views of ManufacturingTomorrow
Comments (0)
This post does not have any comments. Be the first to leave a comment below.
Featured Product
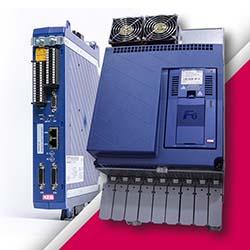