Well be showcasing some of the most unique parts weve printed in a variety of 3D printing processes and materials over the years, including the latest addition to our 3D printing service offering, HPs Multi Jet Fusion.
Talking RAPID + TCT with Protolabs
Contributed by | Proto Labs
Your company will be exhibiting at RAPID + tct, what is it that makes this an important event for your company?
RAPID + TCT is an important event for Protolabs because it gives us an opportunity to connect with our customers and those looking to learn more about the latest developments in industrial 3D printing technologies. The 3D printing side of our business has grown immensely over the years and we look forward to showcasing our latest capabilities and 3D printing service offerings at RAPID + TCT.
What can a visitor to your booth expect to see this year?
Over the past 20 years, we’ve 3D printed over 2 million unique geometries, and with that comes a lot of technology know-how and build expertise. We’ll be showcasing some of the most unique parts we’ve printed in a variety of 3D printing processes and materials over the years, including the latest addition to our 3D printing service offering, HP’s Multi Jet Fusion. Attendees will also find parts from our other digitally-enabled service offerings – CNC machining, sheet metal fabrication, and injection molding.
Any new products you will be introducing?
Our latest 3D printing addition is HP’s Multi Jet Fusion (MJF) technology. You will learn about a number of unique Multi Jet Fusion applications and its respective parts at the booth, including a mask created for Pepsi’s promotional efforts around the popular Marvel Black Panther movie! Additionally, we will have a team of Application Engineers on hand to answer all of your design and manufacturing questions.
When you get a chance to walk the exhibit hall floor yourself, what is it you will be most interested to see?
Our team is very interested in learning about new 3D printing technologies that various OEMs will be debuting and exhibiting at the show. We are a service-agnostic 3D printing service provider meaning we are in a great position to quickly adopt and offer new technologies as they become available. It is always important to make sure that we are keeping up with all of the latest trends in order to provide the best services and offerings to our customers. We pride ourselves on our ability to add new capabilities in an effort to be a total solution to our customers, so we are excited to hear what customers are asking for.
RAPID has many educational sessions & Demo’s, is your company involved in any of them this year?
Protolabs is involved in a few different presentations throughout the week. We have three speaking sessions at the Smart Manufacturing Hub where we will be presenting “A Deep Dive into Metal 3D Printing” with Josh Parker, Manager of DMLS Production. These presentations take place on Tuesday at 2:20 pm, Wednesday at 4:20 pm, and Thursday at 11:20 pm.
We are also sponsoring a lunch and learn on Wednesday from 12 – 2 pm where we will co-present with HP on “Designing for HP’s Multi Jet Fusion: 3D Printing Production and Prototype Parts.” This will be presented by Jon Eric Van Roekel, Process Engineering Manager at Protolabs and John Briden, Sr. R&D Manager at HP. The presentation will be followed by a networking reception with refreshments.
When you book a booth for a tradeshow like this what are your expectations and what does your company hope to accomplish at the event?
When we book a booth at a tradeshow we are expecting to connect with attendees who are not familiar with us and also those who are. We continually seek to expand the range of size and geometric complexity of the parts we can make within each of our product lines, to extend the variety of materials we are able to support and to identify additional manufacturing processes to which we can apply our technology in order to better serve the evolving preferences and needs of product developers and engineers. Given this, tradeshows serve as a great outlet to educate attendees on our services and how they can help them more efficiently and cost-effectively bring products to market.
The content & opinions in this article are the author’s and do not necessarily represent the views of ManufacturingTomorrow
Comments (0)
This post does not have any comments. Be the first to leave a comment below.
Featured Product
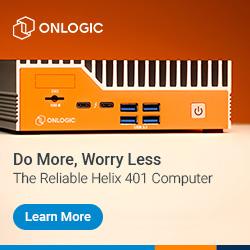