Casey created a 3D printer that uses pellets instead of filament. This was no easy feat, and the design within the pellet feeder is the “secret sauce” that finally enabled Casey to develop her perfect soles, which are used in their line of Athena and Artemis sandals.
OESH Shoes - Manufacturing Story
Contributed by | OESH
Dr. Casey Kerrigan has a unique background, as a Harvard doctor, extensively published biomechanics researcher, and runner. She was never satisfied with her running shoes, and in researching why this was the case, she discovered that existing shoes are designed improperly. Those original academic publications of hers have never been refuted. Currently accepted mass-manufactured shoes with heel elevation, side-to-side contour and arch support result in having a negative effect on the body, increasing the loads on joints, which actually increase, not decrease, the rate of injuries.
She realized that she had to design a sole that did things differently. You see, most athletic shoes are designed to cushion heel impact using toxic foam materials (typically, ethylene vinyl acetate), then control foot movement with contoured, one-size-fits-all footbeds. But heel impact isn’t when peak stresses and strains to the body occur, nor is it healthy to force all feet into rigid, generic forms.
In contrast, Casey’s concept was for a sole that acts as a gentle elastic spring, compressing when the foot is fully planted (at the instant the body’s measured stresses and strains are at their peak) and releasing energy in tune with the body’s natural movement to the next step. In addition, her design is perfectly flat in all directions so the foot can move the way the wearer chooses, always promoting healthy circulation and muscle activity.
But in researching how to make such a shoe, it became quickly apparent it was impossible via traditional manufacturing methods. So Casey spent years trying to figure this out…all based on a proven biomechanical foundation of published peer-reviewed research, and then shifting gears to engineering and manufacturing to give footwear life to the biomechanic truths…all to no acceptable solution.
Then came the “Aha” moment. With the advent of 3D printing, she realized you could develop materials that would be appropriately rubbery, yet structurally complex, and thereby suitable for developing uniquely healthy footwear. . Conceptually, 3D printing enabled her to create miniature springs that were open inside an enclosed space—designs impossible to make with shoe molds. Initially, she experimented with off-the-shelf 3D printers, and various types of filament, but still couldn’t properly create her design.
REGULAR SHOES
OESH SHOES
Fortunately, in nearby Waynesboro, VA, (where lycra and spandex were invented - Dupont once had a factory there) there’s an extrusion facility run by a brilliant engineer, Dave Daughtry. With his help, Casey started developing designs for their own 3D printer and, in the process, visited many nearby factories to see how equipment works…pulling it apart and putting it back together. They used various tools - a water jet saw, CNC milling, injection molding - finally producing a printer that enabled her to prototype soles for the first time, and realized she was finally able to make the robust sole based on her research she could have only once dreamed about, when traditional manufacturing and materials weren’t going to allow that to happen.
At the same time, Casey applied for, and was awarded, a series of grants from the National Science Foundation to research and develop this printer as a means to further develop this uniquely healthy footwear.
She researched many types of elastomers, and experimented with different types of formulations, printing numerous prototypes along the way, and also worked with some large companies (such as BASF and Huntsman Chemical), but even their materials weren’t “springy” enough alone. Meanwhile, her material in filament form wasn’t going to work because there were too many inconsistencies and failures in printing this spring-like material. They also looked into printers from Carbon, but that had a number of drawbacks as well for the type of sole Casey wanted to create.
So Casey created a 3D printer that uses pellets instead of filament. This was no easy feat, and the design within the pellet feeder is the “secret sauce” that finally enabled Casey to develop her perfect soles, which are used in their line of Athena and Artemis sandals. Pellets are also much less expensive than typical spooled filament, allowing OESH to create more affordable footwear. And it was her experience in 3D printing their sandal soles that has informed the design and manufacture of their healthy, and superior, lines of La Vida and Lea athleisure shoes.
The company is a shining example of how innovation and technology can create products that were not previously possible, and revolutionize the manufacturing process for shoes. Yes, a few other companies use 3D printing in shoe components…but none do so like OESH, who now has been able to make some of their entire style lines—at very affordable prices—with 3D printing. Indeed, it was no easy feat to create a line of shoes so easy on your feet.
About Dr. Casey Kerrigan
Dr. Casey Kerrigan, a Harvard Medical School graduate recognized by her academic peers for her peer-reviewed published research on gait (walking and running) and the effects of footwear, left her perfectly good job at the University of Virginia (UVa), where she was the first woman tenured professor and chair of the department of physical medicine and rehabilitation (PM&R), professor of mechanical and aerospace engineering, and professor of sports medicine, to make OESH.
For over 20 years she studied gait, beginning at the University of California, Los Angeleswhere she did her post-graduate residency (and simultaneously received a M.S. in Kinesiology). She returned to Harvard Medical School where she created one of the first sophisticated 3D gait and motion laboratories in the United States. Later, she was recruited to UVa where she developed an even more sophisticated laboratory that could especially break down the biomechanics of both running and walking.
Casey is well known for dramatically changing the way we think about gait and footwear–ripping apart old, sometimes disastrous concepts and rigorously testing new ones–that have now become standards of normal understanding. Casey is the one who first discovered a link between high-heeled shoes and knee osteoarthritis back in 1998 (which was widely publicized in numerous major news outlet including the New York Times, Time Magazine and ABC’s 20/20). And she is the one who published in 2009 that traditionally designed running shoes also increase knee joint torques. She received the highest honors and level of support from numerous national and international entities including the U.S. National Institutes of Health (NIH). Throughout her career, the NIH repeatedly honored Casey’s work through its highly competitive peer-review process, with continuous funding for her research.
Casey’s research, along with her years of clinical experience treating the wide variety of problems linked to poor footwear, led her to develop OESH. Additional motivation derives in part from Casey’s experience as a distance runner at the University of Chicago, where she set several school records in the early 1980’s and from her devotion to her three athletic daughters.
The content & opinions in this article are the author’s and do not necessarily represent the views of ManufacturingTomorrow
Comments (0)
This post does not have any comments. Be the first to leave a comment below.
Featured Product
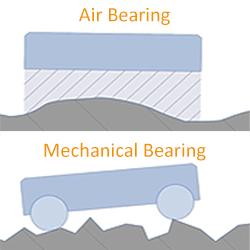