The overall goal of these 2018 trends appears to lead the marketplace to reduce complexity and cost and justify the cost of automated systems and robotics. With lower cost, robotics will become more economical, even for smaller companies looking to become more competitive.
Key Industrial Robotic Trends for 2018
Contributed by | LazerArc
The industrial robotics industry has come a long way in the past decade, as more and more robots are integrated into a variety of production lines. But, as LazerArc looks towards the new-year ahead, everyone wants to know what is on the horizon for 2018, and beyond. Here, are just a few robotics trends to keep in mind before you start planning your 2018 capital spend for improving production lines. They are:
1. An interesting trend according to Brandeis University:
"Growth in robot-as-a-service (RaaS)- Innova Research predicts that within the next two years, people should expect to see more commercial, service-based robots integrated into a variety of global industries. These specific robots will function as "pay-as-you-go" workers, "according to the service type and the time taken by the service." By 2020, this model will make up 30 percent of the global robotics market." https://blogs.brandeis.edu/
2. Other notable trends on the horizon according to a McKinsey article include: "Ease of integration: Advances in computing power, software-development techniques, and networking technologies have made assembling, installing, and maintaining robots faster and less costly than before. For example, while sensors and actuators once had to be individually connected to robot controllers with dedicated wiring through terminal racks, connectors, and junction boxes, they now use plug-and-play technologies in which components can be connected using simpler network wiring. The components will identify themselves automatically to the control system, greatly reducing setup time. These sensors and actuators can also monitor themselves and report their status to the control system, to aid process control and collect data for maintenance, and for continuous improvement and troubleshooting purposes. Other standards and network technologies make it similarly straightforward to link robots to wider production systems." https://www.mckinsey.com/
3. The demand for 7th axis or flexible linear tracks for robots continues to grow. Why?
Companies realize that using a robot for only one task is not efficient use of floor space, and production can be slower and limit the products manufactured on a production line---thus return on investment takes longer to achieve.
Companies installing robots on 7th axis robot transfer units have sped up production, decreased the need for additional floor space and reduced the amount of time required to prove return on investment for each robot.Another advantage to seventh axis robotic slides is that more than one robotic arm can be placed on the same slide for additional productivity and flexibility.
Watch a 7th axis robot transfer system in action
The automotive, aerospace, packaging, solar/wind, medical, consumer goods industries, and more, are starting to incorporate linear robot transfer units into production lines. By integrating these 7th axis slides into a production environment--- one robot will handle more than one assembly task. These tasks could include: loading/unloading, palletizing, product picking, moving products to another production line, welding, assembly and more.
In order to address the growing needs of manufacturers that are looking to integrate robots on a linear robot transfer unit, LazerArc has begun manufacturing the customized 7th Axis Slide, or Robot Transfer Unit to fit a company's application.
To guarantee longevity of the unit, LazerArc provides heavy-duty design to address this issue. It is equipped with high-precision helical rack and pinions that can handle the high dynamic loads and required accuracy. LazerArc's line of Robot Transfer Units are manufactured in floor mounted, elevated or inverted configuration. LazerArc offer the highest precision guardrails, rack and pinion system and closed loop motor control system so companies can manufacture the best product possible.
To extend the reach of the robotic arm, it is placed on a support carriage on a seventh axis slide and rack and pinions re chosen to drive the axis. Using rack and pinions in their modular base design could achieve the unlimited travel lengths achieved by mounting them end-to-end.
The LazerArc Robot Transfer systems are capable of fitting into your automated robotic systems, whether it is a material handling job, paint, and assembling or welding application. All of the units can be adapted to your specific servomotor or robot brand. LazerArc's RTU - 7th Axis system can also be engineered to any length that the customer requires. The design incorporates machined keyed ends that allow for sections to be added or removed easily, when repurposing.
Standard Features of LazerArc 7th Axis Linear Robot Transfer Units:
- Accuracy of +/- 0.003" /ft
- Pre-Machined Carriage to Secure Robot
- Oversized Linear Bearings
- Slight Design Changes
- Machined and Keyed Ends
- Cable Management Systems
- Structural Steel Columns
Options:
- Power and Communication Cables
- Bellow Guard for Linear Bearings
- Leveling Plates
- Higher Accuracy
- Custom Robot Risers
Capabilities:
- Transfer times of 1.5 meters per second
- Heavy duty linear bearings offer high tilting moments
- Optional armoloy coating on gear rack for lube free operation
- Low backlash Gear Reducer
Advantages for Design Engineers and Special Machine Builder:
- Utilizes a direct drive gear reducer and gear rack to achieve higher accuracy and better performance with less components.
- The robust tubular steel construction is "Made in USA"
- Oversized rack and pinion system for greater safety factors
The overall goal of these 2018 trends appears to lead the marketplace to reduce complexity and cost and justify the cost of automated systems and robotics. With lower cost, robotics will become more economical, even for smaller companies looking to become more competitive.
For more information on LazerArc's Robot Transfer Units visit: https://lazerarc.com/product/
The content & opinions in this article are the author’s and do not necessarily represent the views of ManufacturingTomorrow
Comments (0)
This post does not have any comments. Be the first to leave a comment below.
Featured Product
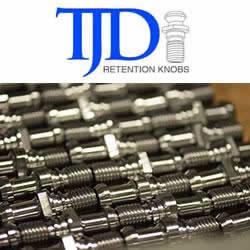