When it comes to 3D printing versus injection molding, the best production method for your parts will become clear when you can answer these questions regarding your desired quantity, quality and cost.
Will 3D Printing Be the Demise of Plastic Injection Molding?
Denny Scher | ICOMold
Some observers of the plastics manufacturing industry, especially those with a vested interest, would like to have you believe that 3D printing is going to be the demise of injection molding. While there are certainly cases where 3D printing makes sense, the reports of the death of injection molding have been greatly exaggerated.
Plastic injection molding is a tried and true method of production that is in no danger of going away anytime soon. It is a basic, dependable method of producing high quality plastic parts. Despite recent improvements in the technology of 3D printing and those likely to emerge in the future, the fact is that more than 80% of plastic parts used in products today have to be injection molded.
The answer to the question, “Which manufacturing method is best for my part?” is, “It depends.” It depends on variables like quantity, quality and cost.
Quantity
David Kazmer, Professor of Plastics Engineering at the University of Massachusetts Lowell, said in a published paper that 3D printing currently makes sense for the most rapid “procurement time to quantity” for a small quantity of 50 or fewer units.
So for production runs, injection molding is still the best manufacturing method, especially considering the long production time involved for 3D printing compared to injection molding.
There is an emerging “hybrid” practice of 3D printing the mold tooling inserts only, then producing the parts with injection molding. For certain limited applications, 3D printed inserts can be employed as a test mold for product development and very limited quantities. A 3D printed mold may last for typically just 60 to 180 pieces.
Kazmer’s study looked at where 3D printed tooling inserts may fit into the big picture, and concluded that there were still significant issues with both metal inserts (surface finish and machine cost) and polymer inserts (surface finish as well as poor strength and heat transfer).
Quality
One of the key limitations of 3D printing is the inability to make parts with the same physical properties as conventional injection molded parts. Although the number of various materials available for 3D printing seems to be constantly increasing, it is still limited compared to all the various plastic materials that can be injection molded. While a 3D printed prototype might be acceptable for evaluating its shape, there is no way to test the material characteristics if your prototype is not the same material as the production part will be.
Another issue cited in Kazmer’s study was surface finish. While the surface finish of the part may vary according to how good (expensive) the 3D printer is, it is still no match for the smooth surfaces attainable with polished steel injection molds.
Last, but certainly not least in the list of quality differences, is the issue of tolerances. Although the ability of 3D printing to hold tighter part tolerances is expected to improve with advanced process designs (like parallel printing) and optimization, today the part quality achieved in 3D printing is inferior compared to injection molding.
Cost
The overall cost of a 3D printed part compared to an injection molded part is tied to the quantity being produced, assuming the aforementioned quality issues do not preclude 3D printing as an option out of the gate. In the study at Lowell, the cost of 3D printing 300 of a certain size part was $20 each. The piece price of injection molding a million such units with a steel mold was just $1.13 each.
Another cost factor to consider is that associated with a design change in the prototyping stage. In 3D printing, there is no cost of modifying a mold for a prototype iteration. Design changes are simply made to the CAD model.
Within injection molding, design changes with a steel mold are typically easy to make and relatively inexpensive, but with aluminum molding tools, a design change may require the expense of all new tooling.
Additionally, new simulation software is now available to help resolve injection molding challenges in software – rather than through costly, time-consuming prototyping iterations. Testing molds in a virtual simulation environment cuts across communication barriers and allows designers, moldmakers, and manufacturing professionals to collaborate more efficiently and effectively, while eliminating the need for costly prototype and mold cycles.
When it comes to 3D printing versus injection molding, the best production method for your parts will become clear when you can answer these questions regarding your desired quantity, quality and cost.
About Denny Scher
Denny Scher is the Marketing Manager for ICOMold, a custom plastic injection molding company based in Holland, Ohio, USA. ICOMold manufactures plastic injection molds and plastic parts for a variety of industries, using steel mold tooling capable of manufacturing various high-quality plastic materials and surface finishes. For more information, visit www.ICOMold.com.
The content & opinions in this article are the author’s and do not necessarily represent the views of ManufacturingTomorrow
Comments (0)
This post does not have any comments. Be the first to leave a comment below.
Featured Product
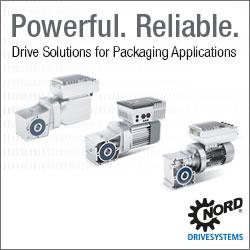