If your robotics research depends on accurate models, you may want to consider looking at MapleSim® 2015 – a high performance physical modeling and simulation tool developed by Maplesoft™.
Ilia Baranov | Clearpath Robotics
A couple challenges with robotics is that robots are expensive and they usually depend on batteries. What if you want to run an experiment with 100 robots, running for 10 hours? To help answer this question, ROS has built in support for robot simulation in the form of Gazebo. While this works quite well, it is currently unable to simulate physical properties like batteries, temperature, surface roughness. If your robotics research depends on accurate models, you may want to consider looking at MapleSim® 2015 – a high performance physical modeling and simulation tool developed by Maplesoft™.
Below we can see a video of the Grizzly RUV taking an open loop control path around a surface. Elements like current and voltage provided by the batteries, surface slipperiness and weight distribution all play a role in where the Grizzly actually ends up. To see what we’re referring to, watch the quick simulation video below:
The MapleSim model features a 200 Ah lead-acid battery pack with a nominal voltage of 48 V, similar to the Type B battery pack used in the robot, to provide electrical power to move the vehicle on an uneven terrain. The lead acid battery used in the model is part of MapleSim’s Battery Component Library. The physical behaviors of the battery are described by mathematical expressions curve-fitted based on experiment measurements to provide the accurate battery voltage and state of charge during the operations of the robot.
The interaction forces and moments at the tire-terrain contact points are generated based on a 3D tire model. A 3D mathematical expression is used to describe the terrain surface to allow the tire-terrain contact points to be calculated based on the position of the vehicle. This 3D function is also used to generate the STL graphics of the terrain for animation (see Figure 1).
The model also outputs electric motor torques, speeds, and battery state of charge as shown below:
Setting up the simulation involves using the Grizzly RUV MapleSim model, available at the bottom of this post. The graphical representation is easy to understand and also quick to modify.
MapleSim and MapleSim provide a testing and analysis environment based on the virtual prototypes of the model. A number of analysis can be performed:
- Virtual testing and analysis: an engineer can easily test the operations of the robot for any design in a virtual environment through simulations in MapleSim. Using Maple, different terrain surface conditions and tire force models to fit different test scenarios can be generated. As an example, the plot below shows different battery energy consumption (state of charge) rates under different terrain conditions.
- Battery optimization: the developed MapleSim model can be coupled with Maple’s powerful optimization toolboxes to determine the optimal battery size and optimize the Battery Management System (BMS) to minimize energy consumption, reduce battery temperature, and increase battery service life.
- Motor sizing: the robot is equipped with four electric motors which are independently controlled to provide wheel torques and steering maneuvers. The seamless integration with Maple will allow the motor sizing optimization to be performed based on MapleSim simulations.
- Chassis design and payload distribution: the virtual prototype of the system will allow engineers to easily vary payload locations and distributions and analyze their effects, e.g., roll-over, stability, controllability, etc., on certain tasks.
- Path planning: Using Maple, different terrain surface conditions and tire force models to fit different test scenarios can be generated for path planning.
- Model-based controller design: the MapleSim model will allow the control strategies to be designed and tested for accuracy before being deployed on a real vehicle.
- Localization and mapping: the high-fidelity dynamic model of the robot will allow state estimation algorithms, such as Kalman filter and other Bayesian-based filtering algorithms, to be performed at a high accuracy.
- Optimized code generation: optimized C code can be generated from the MapleSim model for purpose of implementations of control, localization, and path planning strategies.
For more information on simulating the Grizzly in MapleSim, check it out here.
About Clearpath Robotics Inc.
Clearpath Robotics Inc. is a global robotics company dedicated to automating the world’s dullest, dirtiest, and deadliest jobs with intelligent service robots. The Company provides robot hardware, software and services to enable robot development, deployment and operation. Clearpath works with over 500 of the world’s most innovative brands in over 40 countries, serving markets that span industrial materials handling, mining, military, agriculture, aerospace and academia. Clearpath is an award-winning company with recent awards, including Robotics Business Review Top 50 Company, Edison Award for Innovation, Business Insider Top 40 under 40, and Canada’s Top 100 Employers.
The content & opinions in this article are the author’s and do not necessarily represent the views of ManufacturingTomorrow
Comments (0)
This post does not have any comments. Be the first to leave a comment below.
Featured Product
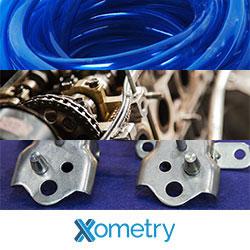