Does technology’s role in manufacturing need a rethink?
In the 1950s, a group of engineers at Toyota revolutionized car manufacturing with the concept of “kaizen” – also known as continuous improvement. Its focus was not centered on buying new machinery or groundbreaking technology. Instead, it prioritized streamlining how work was done, making small, incremental changes to processes that delivered outsized results.
Today, manufacturers are once again chasing transformation. But the approach has changed. This time, it's about AI, automation, and digital tools. With an underlying, yet immense, pressure to adopt, implement and reap the benefits as quickly as possible.
Despite ongoing global disruption, the attraction of new technology remains strong. 76% of manufacturers expect significant productivity gains in the next three years if they invest in new technology. Yet many are left asking the same question; if more is being spent on tech, when will this convert into value?
Productivity tool or digital trap?
It’s not that new technologies aren’t powerful or beneficial to industrial operations. There’s ample reason why organizations are buying more tools, integrating new platforms, and experimenting with AI. For example, to improve production schedules, reduce downtime, or help operators work more efficiently. But too often, these tools are layered onto inefficient processes, poor data infrastructure, and siloed teams. The technology offers the illusion of progress, but the fundamental problems on the factory floor remain untouched. In effect, this digitizes dysfunction.
Nowhere is this clearer than with AI. Adoption is climbing. But, despite this surge, the tangible impact of AI remains limited. Why? Because AI is often unable to solve problems a business doesn’t understand. If your processes are broken, your data is flawed, or your teams don’t trust the tools, AI can end up becoming another layer of complexity. Not clarity.
The manufacturers pulling ahead are doing things differently. Their investments are being embedded into smarter processes, aligned to clear business outcomes, and they build cultures that are ready to adapt. In fact, data shows a 42.3% performance gap in data analysis capabilities between top-performing manufacturers and their peers.
Fixing the foundations first
These strong performers are laying the groundwork first, ensuring the basics are in place before they invest in new systems or solutions. It’s a more considered approach, that may push timelines out, but often it pays off.
Because a common misstep is jumping to the conclusion - or in this context, the solution - before properly diagnosing the problem. And manufacturers are at risk of treating digital transformation as a checklist item. New MES system? Tick. AI pilot? Tick. But transformation is not about ticking boxes.
Instead, a good place to start is with data. Put simply, AI is only as good as the data it works with. If that data is scattered across systems, incomplete, or poorly defined, outputs will be misleading or incorrect.
Process clarity is another stumbling block. When automation is applied to unclear or inconsistent processes, it could make things worse and mean that it is harder to identify the root cause, because the complexity has grown. Without first mapping and understanding the process, AI can replicate inefficiencies at scale.
Then there’s culture. If employees don’t understand why new tools are being introduced, if they mistrust its outputs, or if they fear that technology is being imposed rather than introduced with purpose, uptake will suffer.
That’s why fixing the foundations is the most important starting point. Before any investment in AI or automation, manufacturers need to focus on visibility. Specifically, understanding how work gets done across the organization and where it breaks down.
Making the invisible visible
One increasingly powerful method for gaining visibility is process mining. By using system data to map out real-time workflows, manufacturers can pinpoint where friction exists. For example, where are the delays happening? Which approvals are taking too long? Where are manual workarounds undermining consistency? Why can one site process orders twice as fast as another?
Only once these issues are brought to light can they be addressed. Bottlenecks can be removed, unnecessary steps can be eliminated, and the process can be redesigned for clarity and flow. Then it does often make sense to bring AI and RPA into the picture.
However, its success hinges on having accessible, high-quality data. That means pulling information from multiple systems, establishing relationships between process elements, and preparing that data for meaningful analysis. This preparation phase may involve writing detailed data extraction queries, setting up clear relationships among process elements, and ensuring data accuracy.
While process mining delivers fast visibility, its full return on investment comes over time, as changes are made and sustained. Results need to be measured in both quantitative and qualitative ways, from faster execution and improved shipment accuracy to time saved on manual tasks. Some organizations, like Xpress Boats, have cut expedited shipping costs by 50% and have identified process issues over 90% faster by acting on these insights.
Having the right mindset it key. That means setting clear goals, like reducing invoice cycle times or improving shipment accuracy, and tracking progress against them. It also means being aware of common pitfalls like rushing in without success metrics, neglecting change management, or expecting instant payback.
Cultivating a data culture
Now robust data can come into its own. From machines, suppliers, logistics providers, and customers, manufacturers are swimming in data - but often struggle to use it effectively. Building a mature data culture means moving beyond investing in tools. Rather focusing on shared definitions, clear governance, and making data accessible to the people who need it most.
It also means embedding data into decision-making. This is where AI can make the most sense and the biggest difference. Not as the entire strategy itself, but as a powerful enabler. With a strong and real-time data foundation, AI can help adjust production schedules, identify quality issues earlier, or predict demand more accurately.
Involving the right people early also matters. Cross-functional collaboration, bringing together IT operations, planners and the shop floor, ensures that AI and other digital tools are grounded in reality. When those who’ll be using the technology every day, are part of the design process, the outputs are more practical, and the adoption is far stronger.
The time is now
We’re living through a period of persistent uncertainty, from geo-political unrest to supply chain disruption to fluctuating tariffs and many other contributing factors. Manufacturers are under pressure to respond faster just to keep pace. Speed and agility are everything.
Done right, digital tools like AI, process intelligence (PI) and robotic process automation (RPA) can be critical in achieving agility through speed of detection and intelligent response to disruptive events. They can help leaders see what’s coming, model different scenarios, and respond faster to change. But none of that works if the basics aren’t in place. Data needs to flow across the organization. Teams need to trust the tools they use. And decision-making processes need to be designed for speed and clarity, not stuck in layers of bureaucracy.
What manufacturers don’t need is more disruption. And unfortunately, that’s what AI has the potential to introduce if adopted too soon, or without a solid foundational backbone.
Creating truly intelligent operations
Before starting the next AI or tech initiative, it’s worth pausing to reflect. Are processes understood and optimized? Is the organizational data clean, connected and trusted? Are the people who’ll be impacted ready and involved? Is the problem clearly defined?
Real transformation comes from doing the groundwork - diagnosing, cleaning, aligning and collaborating. The manufacturers who get this right will see higher productivity and build smarter businesses that can adapt, grow and lead through whatever comes next.
So, does technology’s role in manufacturing need a rethink? Yes. Not because the technology is wrong, but because the thinking around them needs to be sharper. Those who take the time to get that right won’t just see better results. They’ll lead the next wave of manufacturing performance.
Comments (0)
This post does not have any comments. Be the first to leave a comment below.
Featured Product
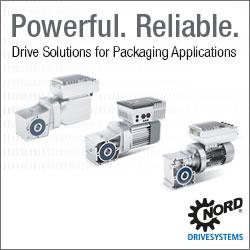