Do Our Youth Hold the Key to Manufacturing’s Skills Crisis?
For manufacturers up and down the country, a shortage of skilled workers continues to be a problem. A November 2024 report found that 97% of manufacturers cite hiring and retaining skilled labour as a challenge to the growth of their business. In the same vein, 75% of UK manufacturers cited skills shortages as their biggest barrier to growth.
While this obstacle is not unique to manufacturing, our sector has it worse than most others – 36% of manufacturing vacancies have proven difficult to fill, compared to an average of 24% in other skilled industries.
Part of this issue’s root cause is the perceived viability of career paths into the sector, with three in five young people unlikely to consider a career in manufacturing.
However, as of September last year, there were 61,000 job vacancies in the UK manufacturing sector, with 339,600 new apprenticeships starting in the same year. So, could youth-focused hiring and upskilling practices hold the key to a long-term solution?
Bridging the skills gap
Given the extent of the skills gap – and how keenly it’s being felt by manufacturers across the UK – hiring managers are understandably cautious of hiring young, unproven graduates. However, provided the correct support framework is in place for graduate hires, there are a number of benefits for the youth-focused manufacturing company.
While candidates that have already established a career in the manufacturing world are likely to have a higher skill level at point of hire, this skill level has been accrued over a number of years with another company.
Adopting a youth-first hiring process means that you have the chance to instil your ethos, your preferred way of working, and your company’s technical focus within the employee. It also means you can facilitate a more rounded skillset, rather than solely focusing on a single area of specialisation, which you might find when hiring a more experienced candidate.
Practically speaking, personnel who do not have previous experience working in the sector should be given the time to explore different areas and different positions, eventually upskilling and specialising in target areas for your business.
For instance, we start our new engineering graduate hires in either the “upstream” team, covering enquiries and costings, or the “downstream” team, working with NPIs and our production teams – allowing them to learn alongside our more experienced engineers. We then rotate these positions as they progress through their training, allowing them to experience the full gannet of GTK’s operations and helping them to gain a holistic view of the business.
When training new manufacturing engineers in the upstream and downstream areas of our operations, we make sure they spend a minimum of three months in each department before moving on to the next. Under close monitoring, one-to-ones and regular feedback, at the end of the total six months we have a great idea of what an individual both enjoys and excels in the most.
Ensuring your business is equipped to support youth
Before adopting a youth-focused hiring strategy, it’s important that your business has the time, resources and infrastructure in place to devote adequate training time to the younger people you hire.
Graduate training programmes tend to last around two years, even across different sectors like pharmaceutical or automotive. Within that time, you’ll need to allocate resources from various different teams in order to create a well-rounded knowledge base.
So, a comprehensive training and development plan is vital to help smooth your new hires’ transition from education to the workplace. Part of your recruitment strategy must include establishing a considered timeline for training, allowing staff to adapt to new roles with a reasonable scale in challenge and with variation between both hands-on and theoretical learning.
One of GTK’s new hires, Calum, joined our engineering team after graduating from Brunel University with a degree in Product Design Engineering. Following his recruitment, we were able to put together a comprehensive and bespoke training plan, knowing his educational background and applying his skillset to our business.
Equally, however, the guidance your business provides should not be limited to vocational support. In-depth pastoral support will form a key part of helping your youth hires feel engaged and supported by the company.
It’s important that dialogue around career progression is a two-way street – ultimately, forcing a new hire down a path they don’t enjoy and aren’t interested in will benefit nobody.
Retaining your people
Perhaps one of the main fears among manufacturing hiring teams is that such time and resource will be invested in youth hires, who will jump ship at the first opportunity. Ultimately, however, this is a risk that any company takes when hiring any individual, and provided the correct pastoral support and career progression plans are in place, there’s no reason your firm cannot retain the staff you are training.
According to Deloitte's recent Workforce Experience research, employees who felt they could acquire necessary skills important for the future were 2.7 times less likely to leave their organisation in the next 12 months.
What’s more, from an upskilling perspective, happy and engaged staff tend to pick up specialist skills much quicker. This can create a win-win situation for manufacturers wanting to train staff in specialist roles, resulting in a motivated workforce with in-demand skills bespoke to your business.
Supporting career pathways in manufacturing
As mentioned, the alleged scarcity of viable career pathways into manufacturing has played a key part in driving the current skills shortage, with one survey from 2023 indicating that just 2% of young people would choose manufacturing as their preferred sector.
Skills development has been heavily emphasised in the Invest 2035 Industrial Strategy; while the introduction of the wider strategy is welcome, the strength of these pathways is yet to be seen.
It’s therefore important that we as manufacturers demonstrate – wherever and however we can – that manufacturing is a viable career choice. Ultimately, an industry-wide shift towards focusing on youth development, both from a graduate level and at an earlier stage, will help futureproof our sector in a long-term response to combat the skills shortage.
Will you be implementing forward-thinking hiring practices to plug your business’ skills gap? If so, faith in the next generation of workers, guidance and a comprehensive training plan could be your ticket to a guaranteed skilled labour force for decades to come.
Comments (0)
This post does not have any comments. Be the first to leave a comment below.
Featured Product
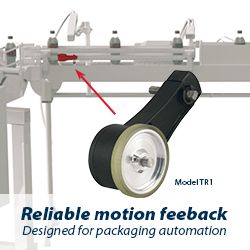