Industrial Analytics: A Catalyst for Sustainability in Manufacturing
There was a time when the average manufacturing facility was a kind of black box: you could measure inputs and outputs, and roughly gauge other metrics, but precision was a pipe dream. That's changed drastically in recent decades, with the advent of the Industrial Internet of Things (IIoT) rocketing manufacturers into a new era characterized by unprecedentedly granular insight into their day-to-day operations.
This change has occurred at the same time that a growing awareness and enthusiasm for sustainable manufacturing has taken over businesses worldwide. You would think that these developments would complement each other—that the more data we can get on our manufacturing processes, the more we should be able to make those processes sustainable.
This is true, to a point—but the fire hose of data now available to manufacturers, flying at high speed from countless machines, can be difficult to integrate and make sense of. Which is why, in recent years, advanced industrial analytics have become so crucial to sustainable manufacturing processes. They allow businesses to actually act on the vast stores of data they now have at their disposal.
The Emergence of Sustainability in Manufacturing
Truly sustainable manufacturing is a hugely complex process, but it has a relatively simple definition. It refers to efforts on the part of manufacturers to reduce environmental impact, conserve energy and other natural resources, as well as, create a safe environment for employees all while ensuring their operations remain commercially viable.
"Sustainability" as we know it,, really came into existence over the last forty years as the reality of climate change gradually seeped into public consciousness. Starting out as a concern for explicitly eco-friendly companies, sustainability has since become a priority for every major company, which is what distinguishes this present moment.
Of course, the impetus for sustainability programs on the part of manufacturers comes from multiple sources. These include:
- Regulatory Bodies like federal and state governments, whose laws companies have to abide by
- Consumer demand, which dictates both what manufacturers produce and how they produce it (because increasingly, consumers are demanding eco-conscious products)
- Corporate leaders, many of whom have emerged as significant sustainability champions in recent years, spearheading ambitious and inspiring efforts to reduce their companies' environmental impacts
Each of these three stakeholders has different (if overlapping) objectives regarding sustainable manufacturing. All three, though, are invested in conserving resources and protecting the environment.
Strategies and Technologies for Effective Sustainable Manufacturing
Any successful sustainability initiative begins with intensive planning. Long before you can implement any changes, you need to determine a) the precise nature of your current resource-consumption and environmental impact, as well as b) what you'd like those numbers to look like after your sustainability initiative is implemented.
The Organization for Economic Co-operation and Development, an international organization that works to build more sustainable economic development policies, has created a toolkit of 18 key quantitative indicators for environmental performance, which can serve as a good starting point here: it includes the recycled/reused content of both inputs and outputs, water intensity, energy intensity, greenhouse gas emissions intensity, what proportion of energy is renewable, and more.
Of course, the precise nature of your sustainability initiative will dictate which factors you want to focus on. The important thing is to get a grasp on these factors well in advance and to set sustainability benchmarks accordingly.
As noted above, the advent of connected manufacturing devices has been a major boon to sustainability efforts. During every step of the sustainability process—from pre-planning/benchmark setting to implementation to follow-up—it is now possible to precisely gauge how you're allocating your resources and what their environmental impact might be. By using the proper sensors, manufacturers can do things like identify levels of energy usage and wastewater generation, as well as inefficiencies in supply chain operations. These sensors generate reams of data, which can then be put to productive use in sustainability initiatives.
It's important to note that this isn't a one-time thing—the idea is not to look at the numbers beforehand, implement some changes, look at the numbers again, and then rest on your laurels. Any meaningful sustainability effort is going to be a permanent process—key metrics must be continually tracked.
For that very reason, it's important to secure buy-in from everyone at the company before, during, and after you begin your sustainability initiative—from employees to boardroom members. There is no simple dial you can manipulate to reduce energy consumption—it's an active, daily process requiring company-wide effort across teams and departments. In many cases, employees may need to be upskilled to handle the changing nature of your company's operations.
The Imperative for a Manufacturing Analytics Platform
As mentioned, an enormous quantity of data is generated by today's connected machinery. But when it comes to actually making sense of all this data, conventional methods are effectively useless—its scope and complexity means only advanced analytics platforms can possibly hope to turn it into something actionable.
Accordingly, the advantages of advanced analytics platforms are numerous and well-established. They include the ability to:
- Monitor and manage energy consumption in real time
- Track and reduce emissions in real time
- Automatically generate sophisticated yet easy-to-read reports, which can keep stakeholders informed
- Process graphics and control charts for continuous improvement
- Engage in complex data modeling, permitting proactive measures through predictive insights
The benefits of all this activity are far from abstract. When it comes to reduced energy consumption, the financial incentives are clear, as are the environmental ones—conscientiously reducing energy use helps save both money and the planet. According to at least one study, people working at businesses that take energy consumption seriously are more productive on average. Using less energy can also help boost your brand's reputation and put a crucial buffer between your company and increasingly volatile energy markets. Additionally, the type of sustainability measures we're talking about here can significantly strengthen your supply chain and build overall resilience.
So, if you're looking to cut down expenses, reduce environmental impact, boost brand reputation, and increase employee productivity, advanced analytics are the way to go. Given worldwide carbon reduction targets and the possibility of more restrictive energy use regulations, starting your analytics-enhanced sustainability initiative now will give your company a head start on what will soon become industry-standard practice.
Kevin Jones serves as the Director of Sales and Marketing for dataPARC. Kevin has been with the company since 2001 and has over 22 years of experience in process industries and using data to drive decisions. Kevin holds an undergraduate degree in Chemical Engineering from University of Idaho. dataPARC is a leading provider of industrial analytics and data visualization tools for process optimization and decision support.
Comments (0)
This post does not have any comments. Be the first to leave a comment below.
Featured Product
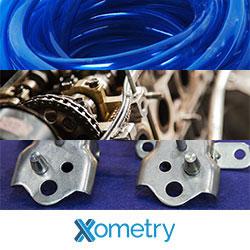