Designing a More Responsive Supply Chain: 7 Strategies for Manufacturers
Supply chain operations are critical to manufacturers’ success. One that’s slow or frequently disrupted will hinder a business’s ability to impress clients and reduce costs, regardless of a product’s quality. Companies must design a responsive supply chain, whether they run their own logistics or rely on third-party partners.
Responsive supply chains are flexible, quickly adapting to demand shifts and disruptions. They can then mitigate challenges that affect industry competitors and minimize waste. Here are seven ways manufacturers can create an effective one.
Modernize Demand Forecasting
The first step to creating a responsive supply chain is monitoring the factors that require a response. Manufacturers must forecast demand changes, but traditional means are insufficient.
Consensus forecasting, which generates individual forecasts for each function before combining them, typically takes four to five weeks, by which time data may be outdated. Instead, manufacturers should focus on the information that will produce the most cohesive, accurate picture. Consumer data from retailers’ POS systems, internal shipment data, web activity and macroeconomic trends are good places to start.
Manufacturers should feed this data into intelligent algorithms as soon as possible. Machine learning models can consolidate and analyze the information far faster and more accurately than people, producing timely, reliable forecasts. Companies can use these insights to predict incoming changes, enabling faster responses.
Evaluate Supplier Relations
Supply chain responsiveness involves both sides of a manufacturer’s logistics: getting materials in and sending products out. Many strategies focus on the latter, but it’s important not to overlook the former. Manufacturers should review their suppliers to ensure the companies that provide their raw materials are equally flexible.
One of the most important factors to consider is communication. Manufacturers should partner with suppliers that share as much information as possible and communicate quickly. They likely have multiple suppliers for various materials, so they should consider using digital communication platforms where they can consolidate conversations.
Diversification is another supplier strategy manufacturers may want to consider. As of June 2021, 55% of supply chain leaders had already implemented dual sourcing for raw materials. Partnering with multiple sources and nearshoring or reshoring can help enable responsiveness even when a supplier falls short.
Assign Different Strategies to Various Products
Manufacturers should also consider that certain products may require differing strategies. They carry various sales volatility, risk margins, costs, market attitudes, buyer expectations, volume and more. Consequently, applying one method across the board won’t result in optimal responsiveness for every product.
Given this variability, manufacturers should segment their products into a few different groups. One way to do this is to plot them along two axes such as demand volatility and shipment volume. Manufacturers can then group items with similar conditions.
Companies that have established these segments can tailor supply chain strategies to each one. For example, high-volume but low-volatility products are better suited for lean production and shipping methods, whereas low-volume, high-volatility items require more resiliency.
Prepare for Weather Delays
A responsive supply chain can adapt to a broad range of unforeseen disruptions. One of the most likely of these, in addition to demand shifts, is inclement weather. Manufacturers may not be able to predict every weather-related challenge, but they can prepare to mitigate them.
More than 70% of U.S. roads are in snowy regions, so any supply chain must prepare for winter weather. Leaving room for slower transportation during colder months and equipping drivers with maintenance equipment can help. Similarly, manufacturers should partner with logistics providers whose drivers undergo extensive training for driving in poor conditions.
Telematics systems and other Internet of Things (IoT) devices are indispensable resources for these efforts. Manufacturers should gather and analyze real-time data about weather conditions and shipment locations to keep an eye on developing situations and respond appropriately.
Keep Vehicles in Prime Condition
Similarly, manufacturers should work with their logistics partners to ensure all vehicles stay in optimal condition. Overlooking maintenance can result in unexpected breakdowns, creating delays that ripple throughout the supply chain. Regular, schedule-based care is better than reactive approaches, but organizations can go further.
Predictive maintenance uses IoT devices to analyze machine health indicators and alert companies when they need repair. That way, businesses can address these concerns before they become costlier, more disruptive problems. Using these readings instead of schedules eliminates unnecessary maintenance stops.
Conventional wisdom holds that oil changes should occur every 3,000 miles, but some vehicles can go 15,000 miles between changes. Data accounts for situations like this, repairing trucks according to their needs instead of a potentially inaccurate schedule.
Improve Logistics Visibility
The IoT can improve more than just maintenance and weather responses. Manufacturers must have immediate insight into every situation to respond to developments quickly and effectively. Thankfully, IoT tracking and data analytics can provide that visibility.
IoT tracking systems can reveal real-time information about shipment location, temperature and quality. Data from other sources can inform supply chain leaders about potential incoming disruptions, like weather, high traffic or facility shutdowns. Gathering this data and feeding it into a single analytics program can give manufacturers a more current, comprehensive picture of their supply chain.
Manufacturers should seek to eliminate any blind spots in their supply chain, asking partners to provide as much data as possible. This visibility is good for business, too. Studies show that 94% of consumers today are more likely to be loyal to companies that offer complete transparency.
Always Have a Contingency Plan
Data monitoring is the first step to another critical supply chain responsiveness strategy. Continuous evolution is vital, as trends and disruptions never stay the same for long. Manufacturers must frequently review their supply chain data to look for weak points and develop backup plans.
Regardless of how flexible and data-centric a supply chain is, it can’t account for every scenario. The COVID-19 pandemic highlights this uncertainty, with 54% of supply chain disruptions in 2020 leading to a “war room” situation that threatened mapped supplier sites. Given how disruptive unforeseen challenges can be, manufacturers should develop contingency plans for when their strategy fails.
What this looks like depends on the specific manufacturer and its supply chain. It may entail having different suppliers or logistics partners they can contact if their current one fails. It should involve backups of mission-critical data and standardized communication. Manufacturers should review their supply chain information to see what assets they need to protect the most and build from there.
Modern Manufacturers Need Responsive Supply Chains
The past few years have highlighted how fragile many supply chains are. Manufacturers must move past historical supply chain shortcomings as world industry becomes increasingly interconnected.
These seven strategies can help manufacturers build more responsive supply chains. They can then adapt to the circumstances that would otherwise stop them in their tracks.
Comments (1)
Featured Product
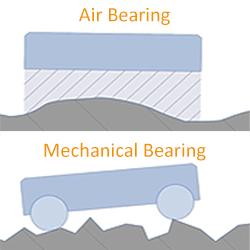