Tend Introduces 1st Factory Optimization Analytics Platform that Combines Robot and PLC Data
Tend announces the immediate availability of the first “plug and play” software solution for factory optimization that blends robot alarms, alerts and data streams with the rest of the data from automation cells. In.production is based on a proprietary machine-learning software engine that runs in the factory, using anomaly detection to allow manufacturers to address chronic problems and potential failures throughout the factory to minimize a loss of production. Some unique attributes of In.production include:
● Analyzes data from most robot manufacturers and PLCs to provide complete device visibility across the factory
● No programming. Factory managers configure alarms and alerts from all devices to produce actionable reporting
● Any factory device that produces data can be monitored for faults and analyzed for predictive maintenance
● Immediate resolution to faults via remote access to the robots and PLCs via smart phones, tablets and PCs
Unlike complex systems that require vast amounts of factory data be processed remotely, Tend’s solution deploys “edge” technology within the factory to identify alerts and self-learn the automation cell’s “normal” operational parameters. Tend’s software locally processes the ongoing data from robots and other devices for anomalies that indicate potential failures, sending alerts via SMS or Email that pinpoint which component is showing signs of failing health. Maintenance teams can immediately identify problems and fix it before an actual failure occurs and chronic problems are prioritized for resolution.
“Tend’s solution has started a revolution,” said Glenn Dantes, Vice President/Owner of ICR Services, a leading Robot Systems Integrator and service provider. “They have the only plug and play product we have seen that combines the data from robots like Fanuc, Kawasaki and Yaskawa with data from other devices in the factory to deliver a complete picture of what is causing downtime across the factory,” Glenn added, “Tend’s platform also gives us the ability to monitor, alert and remotely access all the devices in a manufacturing facility. We can even offer remote maintenance services to help manufacturers dramatically reducing their downtime. And their predictive maintenance capabilities allow us to fix a part before it causes any failures.”
“To reduce downtime, manufacturers have been screaming for a platform that combines Robot Data with Device Data from across entire factory to get a complete and instantaneous view of what is causing production problems.” said Steve Sickler, President at Tend. “In.production delivers that solution it in an easy to use ‘App’ that can be up in running in minutes without programming. Our affordable ‘plug and play’ approach to solving this problem allows even smaller manufacturers that lack a large IT staff to optimize their factory by identifying chronic problems and using predictive maintenance to avoid unforeseen downtime. Combined with the remote monitoring, alerting and access In.Production provides, we have a complete solution.”
In.productionTM is one component of Tend’s first “robot and PLC agnostic” platform. “Both robot and PLC manufacturers already struggle to provide modern software as it is not their core competence,” Mr. Sickler added. “And asking them to provide great software for their competitors’ equipment is just unrealistic. With Tend, companies can standardize on our single platform for a holistic view of all of their factory maintenance issues and priorities across major brands of equipment.”
About Tend.ai:
Tend.ai has developed the first hardware-agnostic factory optimization software suite combined with local computing to deliver the essential modern platform for reducing factory downtime that is easy to set-up and use. Tend has been deployed at some of the leading manufacturers via a nationwide network of certified system integrators. Learn more at https://tend.ai.
Comments (0)
This post does not have any comments. Be the first to leave a comment below.
Featured Product
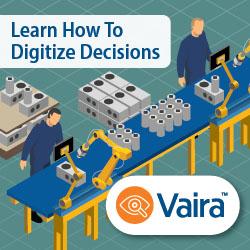