QVI® Introduces New Fusion 350 Large Field of View Metrology System at IMTS 2018
QVI Fusion systems are innovative measurement tools that combine a large field of view (LFOV) optical system with available touch probe, laser, and micro-sensors to produce a family of uniquely productive metrology systems.
Innovative Optics, Multisensor Measurement Tools Offer Enhanced ProductivityQVI® (Quality Vision International, www.qvii.com) introduces its new Fusion 350 large field of view multisensor metrology system, unveiling it to the public at IMTS 2018, McCormick Place, Chicago, September 10-15, in QVI Booth E-135602.
QVI Fusion systems are innovative measurement tools that combine a large field of view (LFOV) optical system with available touch probe, laser, and micro-sensors to produce a family of uniquely productive metrology systems.
The new Fusion 350 is designed to characterize large parts or groups of small parts that primarily require two-dimensional measurement.
The heart of Fusions capability lies in its large field optical system, which allows high accuracy imaging of a wide area — up to 100 mm. QVIs exclusive image analysis software tools can instantly process and identify all features and dimensions within the field of view, with no need for a pre-programmed measurement routine. If a measurement routine has been prepared, Fusions AutoID feature allows placement of any previously programmed part or multiple parts anywhere on the stage, even without fixturing, and Fusion will identify the parts and automatically measure them.
Fusion 350 is ideal for high speed measurement of 2D parts. With its large 450 x 450 mm measuring area and flexible dual magnification optics, it can easily accommodate large parts or groups of smaller parts, and measure both large and small feature sizes. AutoID and Feature Extraction identify and measure single or multiple parts instantly. DRS™ laser and TP20 touch trigger probe are available options for precise three-axis measurements.
All Fusion models are equipped with QVI ZONE3® Express CAD-based 3D metrology software. ZONE3 features a clear, simple user interface, and its kinematic model simulates the machine, part, fixtures, and measuring sensors, updated in real time. Built-in productivity maximizing tools, integrated GD&T functionality, and visual validation of measurement intent offer speed and power to the measurement process. ZONE3 supports simultaneous use of multiple sensors, making appropriate tools available for complex measurement tasks.
About QVI
QVI (Quality Vision International, www.qvii.com) designs and builds a complete line of dimensional measuring machines that combine proprietary optical, laser, and contact sensors for precision measurement of manufactured components and assemblies. More than 65,000 QVI systems are used by manufacturers in over 75 countries to measure and inspect their products for quality and process control.
Founded in 1945, QVI has grown to become the world leader in optical, electronic and software technologies for vision and multisensor measuring systems. QVI brands include OGP SmartScope®, VIEW, RAM, CCP, KOTEM, Itaca and ShapeGrabber. Headquartered in Rochester, New York, USA, QVI maintains corporate facilities in Dayton, Phoenix, Ottawa, Frankfurt, Turin, Budapest, Singapore, Shanghai, Beijing, Xi'an, Suzhou, Bangalore and Tokyo.
Featured Product
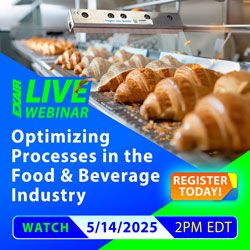
ATEX Cabinet Cooler Systems
EXAIR's ATEX Cabinet Coolers are certified for use with classified enclosure purge and pressurization systems in Zones 2 and 22 explosive environments. Cooling offered from 1,000 Btu/hr to 5,600 Btu/hr, maintain NEMA 4/4X integrity. https://exair.co/184_545a