From Reaction to Prediction: Rethinking HVAC Maintenance Strategies
Author is Dayton Palen, CEM, LEED GA
In the world of HVAC, maintenance is no longer just about fixing what's broken — it's about predicting what will break before it does. As buildings become smarter and more reliant on digital systems, maintenance strategies are evolving too. We're seeing a major shift from traditional reactive maintenance toward predictive and condition-based maintenance models that leverage data and analytics to increase reliability and reduce costs.
Let's explore how these strategies differ, why the shift matters, and what it really takes to implement predictive/proactive maintenance in today's buildings.
Understanding the Maintenance Spectrum
HVAC maintenance strategies can be visualized along a spectrum, ranging from purely reactive to highly prescriptive. Reactive maintenance is the most traditional form — systems are left to run until failure occurs, at which point emergency service is required. Preventive maintenance takes a slightly more proactive approach by servicing equipment at regular intervals, such as every six months, regardless of actual wear or performance.
Condition-based maintenance (CBM) introduces real-time monitoring into the equation. By using sensors to assess equipment condition, maintenance is only performed when data indicates it's necessary. Predictive maintenance builds on this by using historical data and analytics to forecast potential failures, allowing action before a problem even manifests. The most advanced strategy, prescriptive maintenance, not only predicts issues but also recommends specific actions based on the likely outcomes.
These approaches reflect an evolution in maintenance thinking — one that shifts from reacting to problems to preventing them in the most efficient, data-informed possible way.
The following graphic illustrates the timing and cost tradeoffs between reactive, preventive, condition-based, and predictive maintenance strategies. It shows how predictive maintenance enables intervention before serious performance decline or failure occurs, helping reduce both risk and cost.
Source: ENDAQ - Maintenance Strategy Curve
The Hidden Cost of Reactive Maintenance
While reactive maintenance may appear simple and cost-effective on the surface, it often leads to deeper, more expensive problems over time. Unplanned downtime is one of the most immediate risks. HVAC systems are prone to failure under peak load conditions — for example, during heatwaves or cold snaps — which can lead to uncomfortable indoor environments, tenant complaints, and, in commercial real estate, the risk of losing tenants altogether. In mission-critical facilities like hospitals or data centers, downtime can jeopardize safety or disrupt operations entirely.
Beyond downtime, reactive maintenance results in much higher emergency repair costs. These include premium charges for after-hours labor, expedited parts shipping, and inefficient use of internal staff. Often, the urgency leads to temporary fixes rather than sustainable, long-term solutions.
Failures rarely occur in isolation. One component breaking down can strain or damage others. A failed fan motor, for instance, might overheat adjacent sensors or wiring. Similarly, issues like clogged condensate lines or refrigerant leaks can cause water damage or mold growth. These secondary effects multiply the cost and complexity of repairs.
Running systems to the point of failure also reduces their operational lifespan. Motors, bearings, compressors, and other components degrade faster when operating under stress. Issues like vibration, heat, and restricted airflow — often symptoms of neglect — shorten equipment life significantly. ASHRAE data suggests that systems under reactive maintenance may last five to ten years less than those maintained proactively.
Lastly, there are serious safety and compliance risks. Poor air quality, undetected leaks, or temperature control failures can result in OSHA violations or noncompliance with ASHRAE standards, particularly ASHRAE 62.1, which regulates indoor air quality and ventilation. In regulated industries, this can lead to legal penalties or reputational harm.
Equipment Type Median Life (Reactive) Extended Life (Predictive)
Rooftop Units ~ 15 Years 1-7 Years
Centrifugal Chillers ~ 20 Years 1-7 Years
Source: ASHRAE. According to the ASHRAE Service Life and Maintenance Cost Database, median service life for HVAC components is often shortened under reactive strategies.
Challenges of Going Predictive/Proactive
Shifting to a predictive/proactive maintenance strategy offers clear benefits, but it comes with its own set of challenges. One of the largest barriers is the upfront investment required. Sensors, data acquisition systems, and analytics platforms must be installed and integrated with existing HVAC infrastructure, which can be costly.
Data management also poses a significant challenge. Predictive/proactive maintenance generates a constant stream of information that must be collected, stored, and analyzed in real-time. Without proper IT infrastructure and trained personnel, this data is underutilized or misinterpreted.
Many buildings still operate on legacy systems that may not be compatible with modern sensors or platforms, requiring either upgrades or creative integration. At the same time, technicians and maintenance teams must be trained to understand and act on the insights these systems provide — a major cultural and educational shift for some organizations.
Finally, successful implementation often depends on vendor coordination. Building operators must select and manage third-party tools and services that work within their broader ecosystem.
Benefits of Shifting to Predictive and Condition-Based Maintenance
Despite these obstacles, the advantages of moving toward predictive and CBM strategies are compelling. One of the most immediate benefits is the significant reduction in unplanned downtime. By identifying issues before they lead to failure, operators can schedule maintenance during off-peak hours, minimizing disruptions to building occupants. Analytics and maintenance providers report that predictive strategies can reduce unplanned downtime by up to 50% (McKinsey & Company, 2025).
There are also considerable financial benefits. Predictive/proactive maintenance ensures systems are only serviced when needed, avoiding unnecessary inspections and part replacements. Emergency repair costs are dramatically reduced, and budgets become more predictable. Siemens estimates that organizations can lower overall maintenance costs by 25% to 40% through predictive practices
(SIEMENS, 2025).
These strategies also extend equipment lifespan. By preventing problems like short-cycling, overheating, and unbalanced airflow, systems experience less stress and wear. ASHRAE reports that predictive maintenance can extend the life of HVAC equipment by five to ten years, which delays capital expenditures and reduces long-term costs (ASHRAE, 2025)
Energy efficiency is another key advantage. Well-maintained systems run more efficiently, consuming less energy. Predictive analytics can fine-tune operations in real time, adjusting temperature setpoints or airflow based on occupancy trends or environmental data. The U.S. Department of Energy estimates potential energy savings of 10% to 20% in facilities using predictive maintenance (U.S. DOE, 2025).
Planning and resource allocation also improve dramatically. With better visibility into asset health, facility managers can allocate technician labor more effectively and manage parts inventory based on actual need. This proactive approach turns maintenance from a reactive chore into a strategic function.
Perhaps most important is access to data-driven insights. Facility managers can benchmark performance across multiple assets or sites, identify patterns, and make smarter decisions about upgrades, retrofits, and replacements. When integrated with a building management system or digital twin, predictive systems can provide real-time optimization and forecasting tools that transform how buildings are managed.
The following graphic illustrates how maintenance costs and failure rates vary across strategies. Predictive maintenance clearly hits the "sweet spot" — reducing both cost and risk better than either reactive or preventive alone.
Source: Kaizen Institute - Reactive, Preventive, and Predictive Maintenance
A Smarter Future for HVAC
The evolution toward predictive and condition-based maintenance reflects a broader transformation in building management — one rooted in data, foresight, and continuous improvement. By adopting these strategies, building owners and operators can improve reliability, reduce costs, extend asset life, and improve occupant comfort and safety.
While the path to predictive maintenance requires investment and change, the long-term benefits make it one of the smartest moves a building owner/operator can make. The future isn't reactive — it's predictive, and it's already here.
Learn more about Siemens' mechanical services or Operations Manager solutions.
About the Author
Dayton Palen, CEM, LEED GA is a business development manager at Siemens Smart Infrastructure USA. He can be reached at dayton.palen@siemens.com.
Sources
ASHRAE. ASHRAE Service Life and Maintenance Cost Database. American Society of Heating, Refrigerating and Air-Conditioning Engineers. Accessed April 7, 2025. https://xp20.ashrae.org/publicdatabase/.
ENDAQ. "Differences Between Condition-Based, Predictive, and Prescriptive Maintenance." Last modified August 25, 2022. https://blog.endaq.com/differences-between-condition-based-predictive-and-prescriptive-maintenance.
Kaizen Institute. "Reactive vs. Predictive Maintenance." Accessed April 7, 2025. https://kaizen.com/insights/reactive-predictive-maintenance/.
Siemens USA. "Analytic Services for Smart Buildings." Accessed April 7, 2025. https://www.siemens.com/us/en/products/buildingtechnologies/smart-buildings/digital-services/analytic-services.html.
U.S. Department of Energy. Operations and Maintenance Best Practices: A Guide to Achieving Operational Efficiency. Accessed April 7, 2025. https://www.energy.gov/eere/femp/operations-and-maintenance-best-practices.
McKinsey & Company. "The Promise and Challenge of the Age of Artificial Intelligence in Maintenance." Accessed April 7, 2025. https://www.mckinsey.com/business-functions/operations/our-insights/the-promise-and-challenge-of-the-age-of-artificial-intelligence-in-maintenance.
Siemens Building Technologies. "Predictive Maintenance in Smart Buildings." Accessed April 7, 2025. https://www.siemens.com/global/en/products/buildingtechnologies/smart-buildings.html.
Featured Product
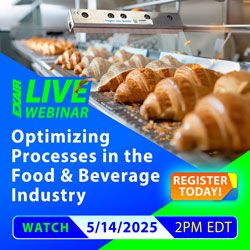
Optimizing Processes For Food and Beverage Industry Webinar
Compressed air is used in nearly all industry types within the manufacturing sector. Since it is also one of the most expensive resources in the manufacturing environment, optimizing your compressed air system for specific applications is beneficial.
This webinar will focus on applications in the Food and Beverage Industry. We'll highlight the benefits of employing an intelligent compressed air solution for tasks ranging from simple liquid spill clean-up to more complex packaging and labeling applications. We'll also look at more innovative solutions with an automation twist to perform product movements and rejections based on quality control inputs.
We will discuss several examples from the food and beverage industry to highlight these benefits and show their universal nature for other sectors.
Register for Webinar on May 14 at 2:00 pm https://exair.co/184_sweb25em