PROVING THE VIABILITY OF METALLISED 3D-PRINTED POLYMER PARTS FOR INDUSTRIAL APPLICATIONS
Andreas Frölich, CEO, Horizon Microtechnologies
For years, metallising 3D-printed or 3D microfabricated polymer parts has been viewed as an enticing but ultimately unreliable approach for industrial applications. The challenges of mechanical robustness and outgassing of the printed part, thermal expansion mismatch and adhesion between the part and the metallisation layer, as well as environmental durability of the metallised layer have caused many engineers to dismiss the concept outright. Failed attempts have only reinforced scepticism.
Across industries, various companies have explored metallisation techniques for polymer-based 3D-printed parts, with mixed success. By way of example, I have seen efforts to develop mm-wave components for defence applications founder due to coating instability under extreme conditions. In another instance, I remember a startup making strides toward using metallised polymer parts in space applications which ultimately abandoned the effort, presumably due to process instability issues.
These cases highlight the key reasons for industry scepticism. Many previous attempts have suffered from inconsistent coating performance, where adhesion failures and uneven deposition led to unreliable results. In other instances, environmental vulnerabilities became evident when components exposed to extreme temperatures, humidity, and mechanical stresses failed to maintain coating integrity. Additionally, limited long-term stability has been a major issue, with outgassing, mechanical degradation, and loss of electrical performance affecting many projects that initially seemed promising.
Tackling Perception Concerns
At Horizon Microtechnologies, our expertise suggests to us that the challenges surrounding metallisation can be overcome if the underlying problems are understood correctly. Our proprietary copper coating process is designed to overcome historical failure modes, but we know that claims alone are not enough. Rather than relying on unproven assumptions, we are committed to a rigorous, evidence-based approach to validation. The only way to change industry perceptions is through hard evidence.
That is why we are embarking on an intensive six-month testing program to systematically address the major concerns that have hindered adoption in the past. Each test will simulate real-world operating conditions primarily for (but not limited to) RF and mm-wave applications in the demanding aerospace sector. Horizon will evaluate its coatings under extreme environmental conditions by exposing them to sudden temperature changes and sustained humidity cycles. In addition, mechanical stresses will be assessed through vibration tests, and outgassing will be examined while exposure to atomic oxygen will simulate the harsh conditions encountered in space applications in low-earth orbit.
Other important tests will focus on compatibility with high-temperature assembly processes will be evaluated through reflow and adhesion tests, ensuring that the coatings maintain their integrity even when subjected to industrial soldering conditions.
Transparency
A key aspect of this initiative is transparency. Horizon Microtechnologies will publish the results of each test, providing the industry with concrete data to evaluate the viability of metallised polymer components. By removing ambiguity and speculation, this approach will allow engineers and designers to assess the material's suitability for specific applications, from aerospace to telecommunications and advanced electronics manufacturing.
Historically, scepticism has been reinforced by the lack of detailed and accessible validation data. Many attempts at metallisation have been conducted behind closed doors, with findings remaining proprietary or incomplete. This opacity has left potential adopters without the necessary confidence to fully explore the technology's potential. By openly sharing our findings, Horizon seeks to challenge not only technical limitations but also the industry's perception of reliability.
The Future for RF & mm-Wave Applications
The ability to metallise complex, lightweight polymer components has profound implications for high-performance applications. In the RF and mm-wave sectors, where traditional metal components present significant weight and manufacturing constraints, the introduction of validated, high-quality alternatives can revolutionise design possibilities.
By way of example, we can consider a directional antenna such as a horn or array antenna to be used in a portable or mobile application such as a UAV payload. Here, every gram of antenna weight is one less gram available for electronic components. On the other hand, basic physics considerations impose a direct relation between the antenna size and its directionality, meaning it can't be reasonably miniaturized without impacting functionality. This leaves the substitution of metal by metallised polymer as the only option to reduce weight.
When we pass these comprehensive tests, Horizon will not merely ‘claim' success in the performance of its metallisation process — it will have ‘demonstrated' success via passage through established testing methods and performance tests of devices pre- and post environmental testing. Our aim is to show that metallised 3D-printed polymer parts should no longer be seen as an experimental risk. Instead, they will emerge as a proven, high-performance alternative, offering new pathways for industries that require advanced manufacturing solutions.
The results of these tests will establish a new benchmark, transforming industry perceptions and unlocking new possibilities for engineers and designers worldwide.
The time for scepticism is over. The era of proof begins now.
www.3dmicrofabrication.com
Featured Product
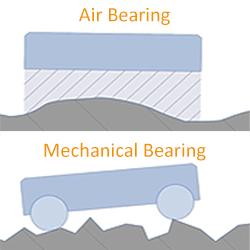
PI USA - Need 6-Axis Precision Motion Control?
With six degrees of freedom and extremely versatile motion and positioning capabilities, hexapods find applications in Aero-Space, Automation/Assembly, Life Sciences, Microscopy, Optics, Photonics. How can a hexapod help your application?