Wireless connectivity enables manufacturers to more easily rearrange their production facilities to meet specific needs, minimizing costly downtime between production runs for multiple clients.
Smarter Manufacturing: Improving Safety and Efficiency With The IoT
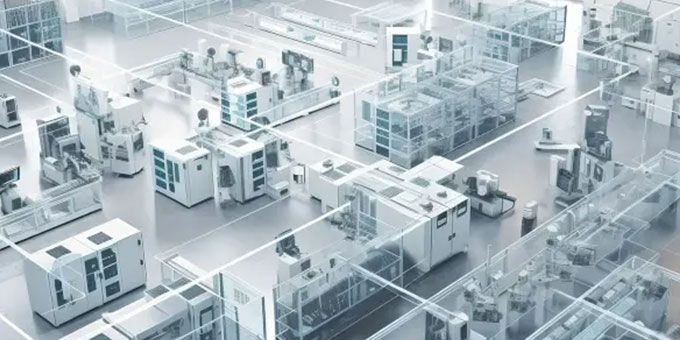
Alex Pluemer, | MacroFab
While there are a few buzzwords and catchphrases floating around to describe the ongoing technological transformation of production facilities, manufacturing has always had the objectives of optimizing efficiency, reducing costs, and ensuring a safe work environment even before factory automation existed. But the invention of the assembly line ushered in a new age in manufacturing processes; now digitization, connectivity, and the IoT are manifesting the next frontier in factory production.
Wireless connectivity enables manufacturers to more easily rearrange their production facilities to meet specific needs, minimizing costly downtime between production runs for multiple clients. Fewer wires and cables to trip over also reduce the risk of workplace injuries and equipment malfunctions.
But wire-free production settings are just one benefit of IoT integration into manufacturing facilities.
Key Takeaways
• IoT integration in manufacturing facilities improves efficiency, safety, and sustainability by enabling wireless connectivity and real-time monitoring of inventory, equipment, and environmental conditions.
• Data-driven optimization through the collection and analysis of massive amounts of sensor data helps manufacturers optimize workflow and regulate equipment stress, reducing downtime and costs.
• Safety and environmental benefits of IoT integration include waste reduction, decreased emissions, and fewer workplace injuries due to automation and improved monitoring.
Many Tasks Performed by Sensors
Digitally monitoring inventory and materials with shelf sensors can help head off potential supply issues before they cause production delays, and sensors that measure repetitive stress on equipment can foresee potential repairs or wholesale replacement before a significant breakdown. This proactive approach can significantly reduce the financial and operational risks associated with unplanned production stoppages, thus safeguarding both productivity and profitability.
Measuring environmental conditions within a production facility – temperature, humidity, air quality, etc. – can help maintain healthy working conditions for human beings and machines alike. By doing so, the company not only adheres to industry and safety regulations but also improves employee satisfaction and efficiency, which directly impacts the bottom line.
Integrating the IoT into a fully or partially automated factory setting can help increase production, reduce downtime and delays, and enhance overall workplace health and safety, while simultaneously improving sustainability and reducing its carbon footprint. These aspects are crucial in a world where business efficacy is increasingly linked with sustainable practices and conscious corporate social responsibility, helping a company remain competitive and appealing to both consumers and investors.
Data-Driven Optimization
The amount of raw information continuous monitoring and data collection can produce can be staggering – a single vibration sensor or air quality monitor taking a reading every second will produce over half a million data points in a week. The data collected could include things like bearing wear, sensor aging, and vibrational stress on motor anchor bolts. AI algorithms could use this data to predict when machine maintenance or replacement is needed, prior to an actual failure and line-down event.
Data collected from a single site has value, but if data is collected from all the manufacturers’ customers, then very accurate predictions can be made for all customers. This is, in fact, one of the things that makes MacroFab’s technology platform and factory network so valuable to all customers.
But data in such great volume would be impossible to process without data analytics. Although the term is often used in other contexts (i.e. targeted advertising), manufacturers can use similar applications to identify patterns in the river of data being collected from multiple sources.
For example, analytic algorithms can make a connection between something as simple as the relative temperature or humidity in a manufacturing facility and the performance of equipment over time. Cooler, drier interior conditions might extend a particular machine’s lifetime by months or even years and/or cut down on downtime and repair costs.
Processing just a few days’ worth of data collected from multiple inputs and cross-referencing them for correlations in a spreadsheet would take months, but data analytics applications can do it almost instantaneously, providing production managers with real-time insight into how their facilities are performing.
The same kind of analytics can be applied to manufacturing outputs to provide insights into the most efficient production lines for any particular kind of manufacturing process. By using statistical insights from previous jobs, MacroFab is constantly improving upon factory matching for current and future production.
Safety and Environmental Benefits
Reducing production facilities’ environmental impact is a regulatory imperative in modern manufacturing, and many parts of the world have financial incentivization systems in place to encourage more eco-friendly production methods and technologies. Therefore, the adoption of these eco-friendly strategies not only satisfies legislative requirements but also presents potential cost-saving opportunities and helps in fostering a positive corporate image.
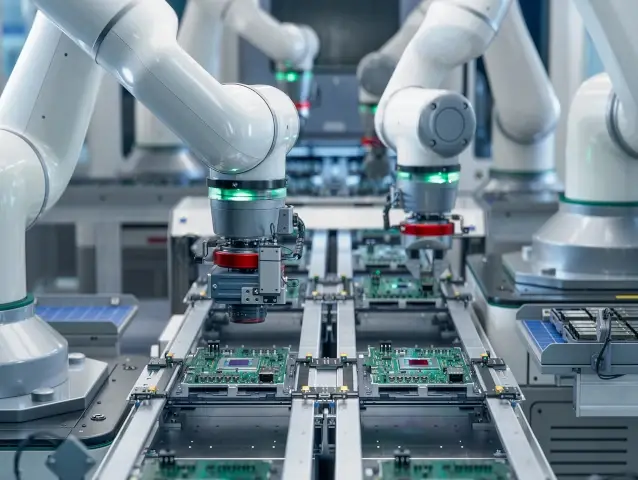
Moreover, automation greatly reduces workplace injuries and other accidents – robotic arms and limbs with wider ranges of motion than previous iterations (due in part to fewer wires/cords wrapped around their exterior) can perform more complex and intricate tasks that are potentially hazardous to human health than ever before. Automated forklifts and other machines that carry cumbersome loads eliminate the need for workers to operate heavy machinery and automated vehicles that transport materials or inventory between facilities reduce collisions or property damage due to human error. This capability can significantly enhance overall production efficiency, while also ensuring the safety and well-being of workers, which in turn leads to improved morale and reduced liabilities.
The biggest savings realized from automation is time – time spent performing relatively mundane tasks, time spent repairing equipment, and time spent reconfiguring the production floor to meet the needs of a particular customer’s production demands and schedule. This conservation of time results in a more streamlined and efficient manufacturing process, enabling quicker response to market demands, enhancing customer satisfaction, and ultimately contributing to increased revenues.
The Future of Automation
In the future, factories will be managed almost entirely remotely, or at least from an office on-site. Manufacturers will manage large networks of wirelessly connected machines, vehicles, and devices and process data with algorithms to optimize production and environmental safety in the future. The move towards this kind of digitization and automation is thus not only a futuristic concept but an inevitable trend, promising to revolutionize the manufacturing industry, optimize resource allocation, and ultimately drive substantial economic benefits.
The content & opinions in this article are the author’s and do not necessarily represent the views of ManufacturingTomorrow
Comments (0)
This post does not have any comments. Be the first to leave a comment below.
Featured Product
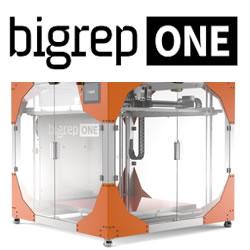