Artificial intelligence has the potential to deliver game-changing results for quality inspection and defect detection. However, until now the process of training the model has proven problematic.
Data Guys Versus Production Pros - Who is the Best Person to Train AI Programs for Defect Detection?
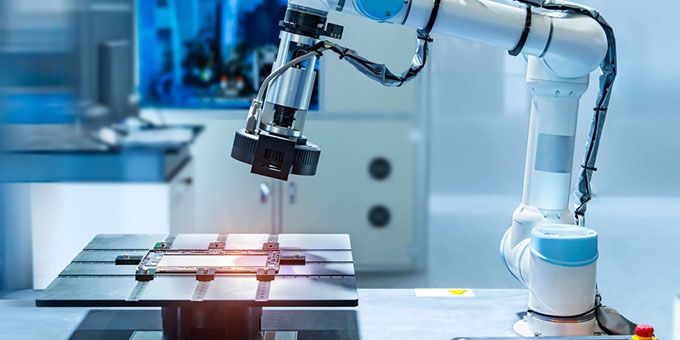
Zohar Kantor, Chief Revenue and Customer Success Officer | Qualisense
When using artificial intelligence (AI) as part of a quality inspection system, many programs require a data expert to help train the model. However, that person is not the most knowledgeable about the product itself. In this article, Zohar Kantor, Chief Revenue and Customer Success Officer at artificial intelligence developer Qualisense assesses whether the data experts or quality managers are the best candidates for helping train the model.
Artificial intelligence has the potential to deliver game-changing results for quality inspection and defect detection. However, until now the process of training the model has proven problematic. The traditional, supervised model requires extensive input from the quality manager and other personnel involved in the production process. For many, the hassle and time this process takes means it is not a worthwhile investment.
The alternative, unsupervised model promises much more on paper, but often fails to deliver in practice. For an unsupervised model, minimal input is required to get the model up and running, but you need input at a later stage to optimise the model. Experience has taught us that relatively minor changes in environmental conditions can seriously impact the performance of the model, which requires the data specialist or other service personnel who supplied the system returning to fine-tune the model. This can be a never-ending story, and one that never ends with a model that fully meets the needs and KPIs of the user.
The optimal solution that industry experts are now leaning toward involves a mixture of these two models. The first stage of the model building process involves as much automation as possible, and is largely unsupervised. The model can be fed untagged images during normal production and learn for itself, building a general understanding of what an okay product looks like and what potential defects look like, grouping the latter into categories. By automating this stage of the model-building process, you reduce time and stress.
However, you still need guided learning to fine-tune that final twenty percent of the process at least. At some stage, the model will require feedback so that it can understand, from the defects that it’s found, which actually are defects and which are normal occurrences, like the presence of dust, fibre or water. The model also needs feedback on which regions of the product are more sensitive than others, so it know where to pay the most attention in the future. Who is the best person to be involved in this process? The data experts, who understand artificial intelligence but have less familiarity with the product? Or the quality manager or similar production personnel, who have a deep knowledge of the product and the potential defects, but do not have a background in AI?
Leverage the quality manager
Until now, the answer to this question was the data expert. If the model was not performing as intended, you had to bring in the data expert to optimise it further or provide additional feedback.
The problem with this is approach was that the data expert won’t be able to determine the difference between a defect that requires flagging, and a defect that is within tolerable limits. They are also less knowledge about different categorizations of defect. They can provide feedback to the model, but without that specific knowledge of the product and the defects that occur, that feedback will be model-oriented, rather than product-oriented.
Ideally, you therefore want the quality manager or another person who knows the product inside out involved in training the model. The problem was that until now, their involvement demanded significant time. By having the first stage of the learning process automated or unsupervised, you can eliminate this. You then need the input of the quality manager for that final ten or twenty per cent, to provide the feedback and optimization in those areas where knowledge of the product is key.
By leveraging the knowledge of production personnel, the model you develop is far more accurate and can handle the more complex problems that previous generations of AI program struggled to contend with.
Qualisense develops software solutions for quality inspection systems. To find out how much time you can save on building your model, contact Zohar Kantor today on zohar.kantor@lean-ai-tech.com or visit https://qualisense.ai/
About QualiSense
QualiSense was founded in 2021 in partnership by Johnson Electric and Cortica to develop a groundbreaking augmented AI platform that processes non-labelled production data to train itself to detect defective parts with minimal user guidance.
The content & opinions in this article are the author’s and do not necessarily represent the views of ManufacturingTomorrow
Comments (0)
This post does not have any comments. Be the first to leave a comment below.
Featured Product
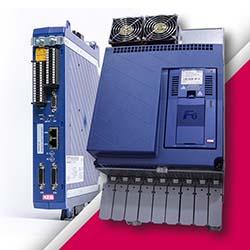