Composable manufacturing is an approach that uses a virtual tool to assemble – or compose – modular packages of pre-programmed processes into new workflows on a screen.
AI-driven Composable Manufacturing’s Plug-and-play Approach Gives Manufacturers the Jump on Disruptions
Srinivas Kuppa, Chief Strategy Officer | SymphonyAI Industrial
Whether it’s called Industry 4.0 or just a new era with new challenges, manufacturing is undoubtedly at a crossroads. Knowing business as usual isn’t enough, manufacturers are recalibrating operations to increase productivity without overproducing. They're reducing energy consumption in the face of volatile energy costs, climate change, and other pressures. Inspired by the Internet of Things and other innovations, they’re looking to boost efficiency via digital problem-solving.
But navigating change is never a simple matter. As manufacturers clarify their objectives and pivot to new market realities, they face strong headwinds. Conditions are tough. Supply-chain snarls, labor shortages and inflation are not going away. Instead, these forces are intensifying, putting still more demand on manufacturers to optimize production. We’re seeing increased demand for specialized materials, with a new focus on smaller batch sizes — the so-called “batch of one.” These smaller batch sizes require plants to respond to demand quickly, effectively and continuously.
New challenges call for new solutions, of course. Today, more plant managers are turning to composable manufacturing to address their needs. Composable manufacturing is an approach that uses a virtual tool to assemble – or compose – modular packages of pre-programmed processes into new workflows on a screen. Deploying AI, machine learning and other cutting-edge technologies, composable manufacturing gives companies to a library of templated functions, a set of core productized capabilities that can be mixed and matched with each other, and an inbuilt integration with other plant systems.
Grappling with such a turbulent landscape, with its escalating demands and new pain points, takes unprecedented agility and flexibility. Without question, a digital transformation in manufacturing through the composable approach is the best – perhaps the only – means to achieve that dynamism. What’s necessary, however, is an execution and operations system that is not only quick and efficient but agile and flexible. Moreover, this system must be able to standardize data from the many disparate processes within a plant or a group of plants, and it must support continuous improvement to meet ever-changing market conditions.
The problematic digital status quo
Too often, manufacturing takes a wrong turn along the way. For instance, an enterprise may depend on a traditional manufacturing execution system (MES) or a manufacturing operations management platform that is monolithic and inflexible and therefore entails significant sunk costs. A common reflex when hunting for alternatives is to instead opt for a slew of different point solutions. But these quick, small-scale fixes only respond to specific problems within the plant’s four walls. They tend to be low-code, drag-and-drop MES apps that don’t marry well.
But point solutions can’t communicate or share data with larger systems or other point solutions. The last thing manufacturers need is a solution that creates data silos across the plant. Anarchy is the result. There’s no standardization, no way to share metrics, no way to share insights.
Without shared data, plant managers can’t glean lessons from across their production cycles, and they lose out on opportunities. The only way to solve the problem is to go back and invest in time-consuming retroactive governance. That adds a whole new level of complexity. What’s more, technical integration campaigns are costly.
Another fix manufacturers may consider is a self-made system. While certainly well-intentioned, that approach is also time-consuming and expensive. Furthermore, by the time the system is perfected, it’s likely already outdated — particularly given the quicksilver pace of changing market demands and conditions. If a bespoke system depends on automation and AI, which it should, there’s another issue: Who’s going to run it? Most plants can’t hire teams of data scientists and they don't have the luxury of the downtime necessary for in-depth training on sophisticated AI systems.
Transcending the challenges: composable manufacturing
A better way forward includes AI-based digital systems that manufacturers don’t need to reinvent the wheel to take advantage of. Composable manufacturing is one such example. With composable manufacturing, enterprises can – and should – leverage either libraries of solutions or a third party’s out-of-the-box execution system for the best results. Already proven, a composable manufacturing system provides the tools and agility for continuous improvement. It’s also designed specifically to provide value quickly and solve problems when they arise.
Composable manufacturing is what it sounds like: a building block approach designed to adapt to the needs of the user. It allows manufacturers to visualize production lines on a screen like flow charts using Lego or Tetris-like images that correspond to processes, technologies, equipment, and other assets. The “composable” aspect of the system allows manufacturers to interlink the images in ways that mirror how the assets function and interoperate in the real world.
Whether working with a low code library of importable composable functions — arrangeable blocks, core functions, equipment and system integration models, and common user interface technologies — or simply implementing a pre-made composable system right out of the box, the results are the same. Manufacturers achieve minimal downtime and disruption and maximum flexibility. These systems are designed so the functionalities that manufacturers need can simply be dropped into a specific location in a particular facility. A visual workflow on a computer screen means that plant engineers, rather than IT teams, can mix and match these functionalities according to their plants’ preexisting operations.
These functionalities don’t exist in a vacuum, either. Composable manufacturing systems connect to Salesforce, SAP and other business solutions. They feature standardized governance to maintain consistency across the board, wherever the system is deployed. AI provides a through-line of intelligence to create continuous learning and drive productivity, running metrics on a whole range of operational key performance indicators — process, quality, line, plant level, assets, whatever a manufacturer needs. The result is actionable — and accurate — intelligence for decision-making that drives continuous growth.
We’ve seen some phenomenal results when manufacturers choose this type of composable system. In one instance, a global multi-industry consumer products company improved yield and throughput by 30 percent. Another global commodity products company increased lead-time and service response by half. An international high-tech and semiconductor leader reduced waste by 30 percent. And a global agricultural products company cut costs due to poor quality by more than a third.
A plug-and-play approach, governance, standardization, and data-driven actions are novel factors in manufacturing. But a component-based system, easily accessed and utilized, makes it possible, particularly when deployment is a matter of weeks, not months, and adaptations and additions must be complete within the plant’s production schedule — not the other way around. At the end of the day, it’s all about avoiding anarchy, managing variables, and making it simple. Composable manufacturing is the tool that puts manufacturers ahead of disruption — and not a moment (or a rollout) too soon.
The content & opinions in this article are the author’s and do not necessarily represent the views of ManufacturingTomorrow
Comments (0)
This post does not have any comments. Be the first to leave a comment below.
Featured Product
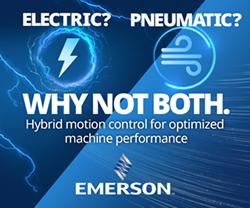