How a leading dairy producer used Westfalia AS/RS to streamline processes in two locations, helping deliver a higher quality product to its customers.
The Tale of Two Cold-Storage Warehouses: Automating Aurora Organic Dairy
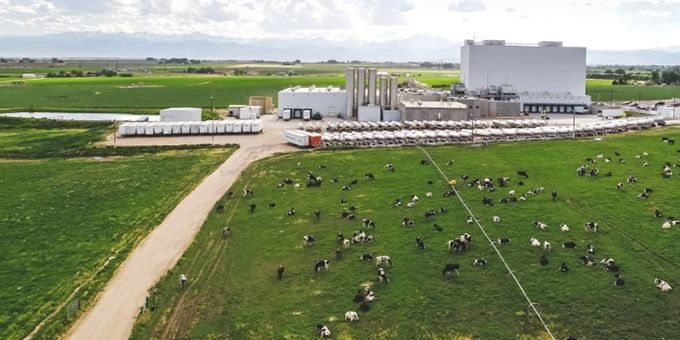
Case Study from | Westfalia Technologies, Inc.
About Aurora Organic Dairy
Aurora Organic Dairy is the leading producer of store-brand organic milk and butter for U.S. retailers, operating several farms and facilities across the nation. Based in Boulder, CO, it oversees heifer farms and organic dairy farms in Colorado and Texas, as well as organic dairy processing plants in Platteville, CO and Columbia, MO. They manage the entire product lifecycle—from its farms to its processing facility—with a dedication to organic standards and sustainable production at every stage. To meet these standards and ensure the highest quality product for their customers, Aurora needed an efficient solution to build an in-house cold-storage warehouse.
And so, Aurora’s partnership with Westfalia began—in Platteville, CO.
Platteville, CO: An Expansion Years in the Making
Aurora Organic Dairy’s (AOD) integrated cow-to-carton model began in 2003 with an on-farm milk plant in Platteville, Colo. Its organic dairy products are distributed nationally, and AOD has a large inventory of extended shelf life (ESL) products, which helps to balance supply and demand while providing excellent customer service levels. As AOD grew through new channels and an expanded product assortment, the company outgrew its third-party warehousing, and needed a small-footprint, in-house cold storage facility on-site at its milk processing plants.
Challenged with a lack of space to accommodate a large warehouse addition, Aurora reached out to Westfalia Technologies to design an Automated Storage/Retrieval System (AS/RS). The AS/RS allowed them to build a highly automated cold-storage warehouse adjacent to the milk plant to accommodate their growth within limited square footage and transform the entire warehousing process, from production to shipping to staging.
“As a company with a strong foundation of sustainability, we liked that we could build a smaller warehouse for long-term energy savings,” said Joe Harmon, Senior Manager of Technical Resources at Aurora Organic Dairy. “We also felt that Westfalia offered a more flexible design than other companies. The racking design allowed us to build a custom facility based on the sheer number of pallets we needed to store on the square footage we have available.”
The custom solution is tied directly to production, allowing flexibility to process orders in advance. With pallet accumulation on the inbound and outbound system, orders can be fed to the dock to allow for quicker truck turns. In addition, two high-speed tandem pallet cranes provide the high throughput necessary to support future growth. This not only makes the production and distribution process more efficient, it also eliminates the need for manual touches—reducing labor costs and improving product freshness and quality.
Aurora was pleased with Platteville’s AS/RS which exceeded the company’s initial throughput and energy efficiency goals. Harmon noted Westfalia’s continued support and expertise throughout the design and installation process was one of the major benefits of the partnership.
“The biggest challenge to implementation was that we were running the plant and producing products during the warehouse construction and commissioning process,” said Harmon. “Westfalia was a great partner to be able to work with a fully operational facility and allow us to keep it running while they completed the commissioning of the warehouse, train employees, and troubleshoot any issues.”
When it came time to expand once again, Aurora decided to build a second dairy processing plant in Columbia, Missouri. With the success of the Platteville cold-storage facility behind them, they knew that this time, it would be automated from the start—with Westfalia by their side.
Columbia, MO: Taking AS/RS to the Next Level
Aurora selected Westfalia to design, manufacture and install a second AS/RS within their new Columbia cold-storage warehouse in 2018. While the AS/RS solution was similar to the Platteville installation, the Columbia location was a greenfield site; this offered far greater flexibility in square footage, capacity and solution design.
Without space restrictions, Westfalia designed an AS/RS with a true outbound staging system. With two outbound staging lanes to pre-stage products ahead of time, trucks at the Columbia warehouse can turn in under 30 minutes at the dock. This further maximized warehouse and distribution efficiency.
“We developed a solution that worked well for us in Colorado, so it was natural to implement a very similar solution for our second location,” Harmon said. “The fact that the warehouses are so similar and designed by Westfalia also provides flexibility in maintenance and training between the two facilities, as well.”
The addition of the Columbia warehouse meant Aurora could expand its product offerings to customers and ship milk from another key location. Ultimately, Aurora’s continued partnership with Westfalia resulted in another streamlined production and distribution site, with even faster truck turns and higher throughput.
A Continued Partnership
Integrated with Westfalia’s AS/RS, both the Platteville and Columbia cold-storage warehouses saw improved efficiency, higher throughput, and more control over inventory—all contributing to the delivery of a higher quality product to their customers. In addition, Aurora saw cost savings from building an in-house solution, rather than relying on third-party cold storage providers. A consistent AS/RS design also allowed for simplified training and maintenance across facilities, with Westfalia experts to assist along the way.
With a long-standing relationship and two successful projects under their belt, Aurora Organic Dairy and Westfalia Technologies continue to work closely together to implement the best solutions for the future.
The content & opinions in this article are the author’s and do not necessarily represent the views of ManufacturingTomorrow
Comments (0)
This post does not have any comments. Be the first to leave a comment below.
Featured Product
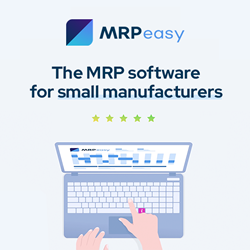