Does keeping an organized workplace really create a competitive advantage? DSI believe it does and here are the reasons why.
The 5S Method for Workplace Organization
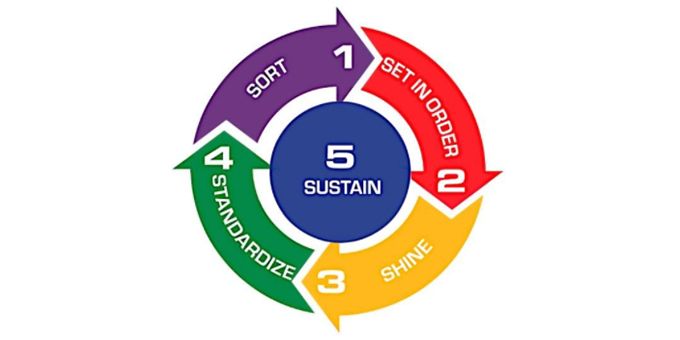
Randy Dennison, Marketing Manager | Decimet Sales Inc.
It’s a competitive world out there, but for Sheet Metal Fabrication and CNC Machining shops like Decimet Sales Inc. (DSI), it’s more than just a competitive space - it’s crowded! That’s why DSI looks for ways to differentiate themselves from the competition, while maintaining quality and staying competitively priced. One such way is by adopting the 5S method for workplace organization.
Does keeping an organized workplace really create a competitive advantage? DSI believe it does and here are the reasons why.
First, the 5S method for workplace organization is a systematic approach to higher productivity. Top productivity means producing more in less time and that translates into satisfied customers. If DSI customers can get their projects on time and within budget, a relationship of trust is built. That’s a much-needed differentiator in their crowded industry.
Secondly, the 5S method leads to lower costs. When costs are reduced while maintaining product quality, savings can be passed on to the customer and that helps build on the relationship of trust.
Additionally, the 5S method can help DSI move toward higher quality, increased safety, and improved employee satisfaction. When employees feel safe and satisfied, turnover is reduced and production increases. Management can work at more important tasks rather than spending hours at interviewing applicants and training new employees.
The benefits of the 5S method are numerous and are helping differentiate DSI as a great choice for metal fabrication and CNC machining services. These benefits can be traced back to the elements that make up the 5S method.
The 5S Method Explained
The 5S method was first industrialized by the Toyota Motor company back in the 1970’s. It can be identified as one of the techniques used to enable Just in Time (Lean) manufacturing which reduces time in the manufacturing process or with the response times between supplier and customer. The philosophy behind this method aims to eliminate all distractions, mess, clutter, or waste in the production process so that the value to customer products or services can be improve or increased.
There are five main elements to the 5S method that if implemented correctly, can transform a manufacturer into a safer and higher productive facility. The elements are very practical, and everyone can participate. These elements are described below:
Sort: With this first element, a value is placed on all items that take up space in the work area. Any tool, furniture, material, machinery, equipment, or any item not needed for the current production in the applicable area is eliminated. This creates a workspace free of clutter and provides the groundwork for all other elements.
When items are in question, the red tag method can be applied. This involves putting a red tag on the item and placing it in a designated “red tag” area. If the item hasn’t been used in a determined amount of time, for example one month, then the item can be eliminated or stored.
Set in Order: With this element, all things necessary to complete the current production are put in a strategic or logical place. These items should be easy to store, identify, get to, and easily returned to their proper home. The main key is standardization. If items are used together, they should be stored together. Other standardization options may include, storing items in priority order or putting items used more frequently closest to the user, labeling items and a host of other guidelines that may apply.
One additional consideration is to identify anything that would cause waste which can appear in many different forms. For example, defects, wait-time, additional steps, motion, excessive inventory, overproducing or extra processes, transportation or un-utilized skills can all produce some form of waste.
Shine: Keeping your workplace cleaned daily is the third element of the 5S method. It is such a simple concept but easily overlooked and forgotten when production gets busy. Clean machines and work areas make an inviting environment for employees and make them invested as they take ownership of their area.
Shine also includes inspection and preventative maintenance. The goal of Shine is to have everything clean and running longer in top working order. That means the work will be safer with fewer injuries and insurance claims. In addition, there will be fewer equipment breakdowns. Breakdowns and investing in repair maintenance, parts, and new equipment is expensive to say the least.
Standardize: Create a working order, standard procedure, a posted schedule, or checklist will help to ensure the elements of 5S are carried out daily. The goal of Standardize is to systemize the 5S elements so that one-time tasks can be turned into lasting habits. Visual charts or posters can be used and are great tools that help remind employees that a system is in place. If a system is in place and employees are held accountable to following it, they will know what to do and when to do it. Standardized procedures create uniform order and greater productivity.
Sustain: This last element of the 5S method should be designed to keep employees involved, motivated, and focused on 5S which keeps them on track to greater productivity. Concrete steps must be taken with everyone, including managers to make 5S a long-term program so that 5S becomes part of the business culture rather than a one-time procedure. When 5S becomes part of the culture, employees stop cutting corners, and the business will realize a host of other positive results like increased efficiency and productivity.
Safety: Some businesses include a sixth element for workplace organization and may be referred to as 6S. This element helps to guide management and employees in reducing or mitigating risk and injury. Safety may include, adding ergonomics to workplaces, marking potentially hazardous areas with signs and labels, or taping off intersections between forklifts and pedestrians. If the workplace has hazardous risks due to the layout or equipment setup, steps should be taken to eliminate those risks. If an accident occurs, consider why it occurred and if any part of the 5S method should be changed to reduce or eliminate the risk of future accidents.
5S works and makes a difference when everyone is accountable. Both manager and employee have an integral part once the decision has been made to make 5S part of the business culture.
DSI knows the importance of 5S, and they are working every day to sustain it as part of the DSI culture. That means, you as their customer reap the benefits of choosing a metal fabricator or CNC machining service facility that operates with greater efficiency and productivity.
If you have any questions about the 5S method for workplace organization or if you wish to tour the DSI facility, please contact them at 763-428-4321.
The content & opinions in this article are the author’s and do not necessarily represent the views of ManufacturingTomorrow
Comments (0)
This post does not have any comments. Be the first to leave a comment below.
Featured Product
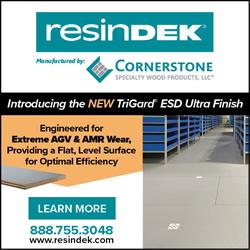