Two Ultra Motion Servo Cylinders were successfully employed to control the telescope’s elevation and azimuth throughout the flights. The ARTEMIS system had to operate flawlessly at 70,000 feet and in ambient temperatures as low as -60°C.
Ultra Motion Actuators Help Measure The Moon At 70,000 Feet
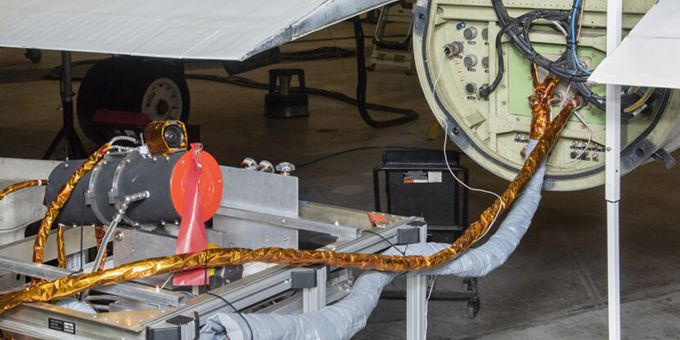
Case Study from | Ultra Motion
The airborne lunar spectral irradiance mission (Air-LUSI) is a partnership between NASA and NIST to create SI-traceable measurements of lunar spectral irradiance in an effort to improve the measurements of Earth observing satellites. These satellites monitor the weather, vegetation, ocean currents, pollution, and more. Using the light reflected from the moon as a constant absolute reference point for satellite calibration will allow for improvements to these satellites and consistency between data from different satellite instruments. Satellites will be able to calibrate in-orbit and over-time as sensors degrade.
The custom telescope used to acquire the data is installed into the wing pod of an Earth Resources-2 aircraft, which is a direct descendant of the U-2 spy plane. The ER-2 flies to an altitude of 70,000 feet allowing the telescope to measure the light from the moon above 95% of the Earth’s atmosphere. Reducing the distortion effect of the atmosphere allows Air-LUSI to characterize the spectral irradiance of the moon more accurately than ground-based measurements, and in a similar environment to the Low-Earth Orbit satellites that will make use of the calibration point.
Ultra Motion’s Role
An autonomous robotic telescope mount instrument subsystem (ARTEMIS) was created by Dr. S. Andrew Gadsden and his team in the Intelligent Control and Estimation laboratory at the University of Guelph (Ontario, Canada) in order to accurately track the moon during the flight. Two Ultra Motion Servo Cylinders were successfully employed to control the telescope’s elevation and azimuth throughout the flights. The ARTEMIS system had to operate flawlessly at 70,000 feet and in ambient temperatures as low as -60°C. External heating elements were used to maintain the temperature of the actuators throughout the flight. Custom self-heating Servo Cylinder firmware can be installed to use the motor as a heat generating element for applications that cannot make use of external heaters.
Telemetry was gathered from the actuator’s integrated controller in order to monitor the performance and health of the Servo Cylinder throughout the experiment. This included absolute position from the Phase Index contactless sensor, actuator temperature, bus voltage, and actuator phase current. Real-time data from the Servo Cylinders provide insight into the overall performance of the system and increases the confidence of the ARTEMIS for future test flights.
Results
A demonstration flight campaign over five separate flights showed that the ARTEMIS successfully tracked the moon with a root-mean-squared-error of 0.11° tracking accuracy! The Air-LUSI experiment will continue to be used over the coming years to gather lunar irradiance data for a range of lunar phases. As the data set grows, a higher fidelity lunar spectral irradiance model can be produced and allow for improvements to a significant amount of Earth-observing satellites.
A video overview of the Air-LUSI mission is shown below:
https://www.youtube.com/watch?v=4pT2_sO-of8&feature=emb_title
Photo Credit: Ken Ulrich, NASA
Photo Credit: Ken Ulrich, NASA
Photo Credit: Ken Ulrich, NASA
Telemetry recorded via the Servo Cylinder’s serial communication interface. The above graphs represent the azimuth actuator’s temperature and the elevation actuator’s absolute position during the five separate flights.
The content & opinions in this article are the author’s and do not necessarily represent the views of ManufacturingTomorrow
Comments (0)
This post does not have any comments. Be the first to leave a comment below.
Featured Product
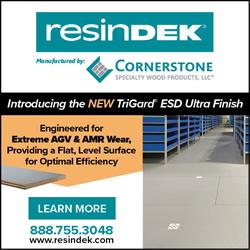