Now, more than ever, there is a greater need to reduce risk for fast-turn, first time right builds, particularly in essential and highly complex businesses such as medical technology, semiconducting, and others where there is a high cost of getting it wrong.
CoDevelopment: Why Continuously Sharing Design & Manufacturing Data Empowers Electronics Engineers to Innovate Faster
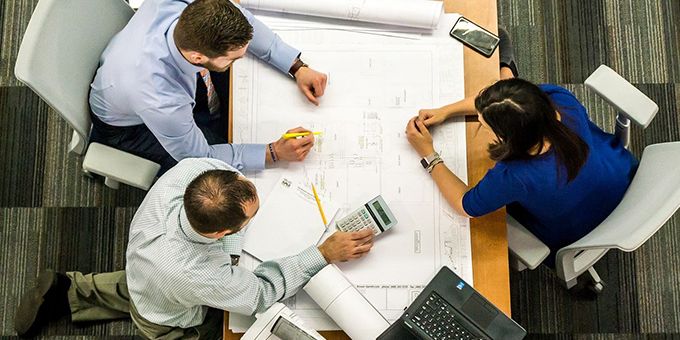
Brady Bruce, Head of Marketing | Tempo Automation
The manufacturing industry is seeing a turning point in its growth and development, moving from decades-old operational processes to new implementations of IoT and connected technology such as smart robotics and industrial systems. And now, the recent pandemic has complicated many components of our lives and the processes of manufacturing, hardware development and prototyping is not immune. There are dozens of factors contributing to the complexity of the new normal -- from remote work and stay-at-home orders, to travel and trade restrictions that have caused disruptions to the component supply chain.
Now, more than ever, there is a greater need to reduce risk for fast-turn, first time right builds, particularly in essential and highly complex businesses such as medical technology, semiconducting, and others where there is a high cost of getting it wrong. As businesses come back online, engineering teams need creative, efficient ways to solve these problems and develop builds faster, while ensuring that quality doesn’t take a backseat.
In Printed Circuit Board Assembly (PCBA)/prototype electronics manufacturing, the working relationship between engineers and a CM can be transactional at best, or like navigating a storm of challenges at worst. This can be achieved through the implementation of manufacturing processes such as CoDevelopment.
The traditional model of Transactional Manufacturing
In hardware development and prototyping, the working relationship between engineers and a contract manufacturer (CM) can be transactional at best, impacting the timeline and quality of board builds. This is often referred to as transactional manufacturing. In the transactional relationship, it is like there is a brick wall between designers and manufacturers -- after the design is completed, a monolithic manufacturing package is tossed over the wall, and sometime later, a board is tossed back. Then the whole process starts all over again, from scratch, with no additional information or insight to show for it, leaving engineers back at square one.
Transactional manufacturing, even when done well, is fundamentally limited – and to better understand these limitations, it is important to evaluate the tasks associated with the prototype manufacturing.
The designing and manufacturing process for prototype electronics is often referred to as the DBT, or Design, Build, Test cycle. The Build phase is when the board is manufactured. The most important task is fabrication and assembly of the printed circuit board (PCB), but it is just one of many tasks that must be completed for a successful build. These other tasks are related to processing data and include data validation, DFx, production planning, sourcing, configuration management, and CAM generation. In a standard transactional model, data is shared from the engineer and the manufacturer begins only when the design is finalized.
This puts all the tasks described above on the critical path and leads to four fundamental issues. The first is task compression where a majority of the time is focused on production, compressing time spent on data processing tasks into as little durations of the design possible and thus, increasingly the possibility of errors and omissions. This coincides with the second issue, delays, especially for complex boards, which can put a project behind schedule before the production has even begun. Then, if Design-for-Manufacturing (DFM) issues are discovered by the manufacturer, it is often too late in the project schedule to change the design, leading to design-lock in. Engineers and designers are left with second-best solutions like post-production reworks of the board, which impacts the quality of the final prototype electronics. Finally, there is no single source of truth in a transactional model because the engineer and manufacturer data are always separated. This means that both sides are working with incomplete and potentially conflicting data, which can impact version control, build configuration management, and the overall project timeline. With a build process that sees the first interaction between the designer and manufacturer beginning after the design is finished, inefficiencies and opportunities for errors arise.
Transactional manufacturing is one of the most common approaches in the hardware development and prototyping industry, but it is inefficient and can lead to lower-quality boards, as well as extended timelines and impact engineer creativity and innovation. The alternative involves sharing the design of manufacturing information from manufacturers, to engineers, much earlier in the design and build process using CoDevelopment.
What is CoDevelopment?
CoDevelopment is often known by other names such as Agile Hardware Development or Agile Electronics Development, but the core principle is that continuously shared design and manufacturing data leads to better results. Rather than communication and data-sharing barriers between engineers and CMs, there is transparency. Instead of a periodic transmission of data at sporadic times, there is a continuous sharing of data, from before a design is even uploaded, to the the moment a CAD is shared, throughout the DFM process, and even afterwards with forensics and data gleaned from the manufacturing process. CoDevelopment leads to a better coordinated, more efficient prototype manufacturing process that will yield better results for engineers and their teams.
CoDevelopment drastically opens the relationship and line of communication between CM and engineer. In CoDevelopment, the design process overlaps with the manufacturing process and allows engineers to work synergistically with their CM throughout the build process. It also gives them the opportunity to make critical edits to their design before the board makes its way to assembly production.
With CoDevelopment, there is also less schedule risk. This is because data processing and issue resolution are tasks that are removed from the critical path and happen in parallel with the PCBA design phase. If an issue comes up, they can be addressed thoroughly, without the time pressure or worry about delaying the build – compare this to transactional manufacturing where there is often a day-to-day delay if issues are found.
CoDevelopment also offers multiple opportunities for data feedback derived from the manufacturing process itself, back into the design process, reducing design risk and creating a dynamic feedback cycle that can immediately make changes to the design as they’re discovered. This leads to less revisions overall, because there is no longer the need to completely re-spin the board to correct issues, which can drive time and cost.
There is also minimal data risk with CoDevelopment, as it generates a single data set that merges both design and manufacturing information which supports proper build configuration control. As design iterations are made during the PCBA process, the data gleaned from testing and re-spinning boards is compiled into a single source of data that can then be used as the input for all of the other processes in the DBT cycle. And drawing from the same data leads to greater process control and higher quality boards.
In a fully developed CoDevelopment system, interaction can start as early as when the first board outline is created, or a single component is specified, and continues until the board makes its way through production. Both designers and manufacturers draw from a single source of truth guaranteeing the correct design configuration is built. Seamless ECO processing allows in-process course correction during manufacture and all of the previous ephemeral communication would be captured and stored in the production log. Engineers are in turn provided important insight and a virtual presence on the factory floor during the PCBA process.
CoDevelopment in Practice
With more manufacturing processes leveraging Industrial Internet of Things (IIoT) networks and software automation, smart factories are revolutionizing the traditionally slow PCBA manufacturing cycle and enabling CoDevelopment.
For example, end-to-end software automation in a smart factory can create a “digital thread” that automates the flow of information from the engineer’s design to the machines and the people on the connected factory floor. This supports CoDevelopment, allowing engineers to communicate directly with the manufacturer throughout the build process, and working with them synergistically to complete the DBT cycle with quality, speed, and accuracy in the PCB assembly.
The CoDevelopment cycle at work in a smart factory, leveraging a digital thread to automate the flow of information from the engineer’s design throughout the factory floor.
As the electronics manufacturing industry across verticals like medical technology and semiconductors face increased demands driven by the COVID-19 pandemic, the need for practices like CoDevelopment have never been more important. Highly complex electronics that use equally complex boards need a system in which they can be developed more efficiently and effectively for first time right builds.
By choosing a CM that supports CoDevelopment through a software-driven smart factory, manufacturers are able to solve many problems of the traditional PCBA manufacturing processes that often plague engineers.
CoDevelopment supports a world where high fidelity leads to high efficiency, engineers get their boards back faster and with more analytical data, and higher quality, and where more innovative products are brought to market faster. Put simply, CoDevelopment is the shortest path to reality for the complex products that will enable real change in the world.
About Brady O. Bruce
Brady O. Bruce is Head of Marketing at Tempo Automation. Having served for over 25 years in marketing, product management, and sales with global B2B and consumer technology companies, Brady offers a wealth of executive experience. Prior to Tempo, Brady was Chief Marketing Officer for InFocus Corporation, an industry-leading collaboration and learning manufacturer. He also served as Vice President of Marketing and Strategic Alliances at Jupiter Systems and has served in leadership positions at UCC, Promptu, PRISMIQ, NightFire Software, Radius, and VTEL Corp. Brady was also the founder and CEO of RedDotBlue and fatBubble. Brady has a wealth of executive experience, having served for over 25 years in marketing, product management, business development, and sales with global B2B and consumer technology companies; his record of value creation includes one IPO and five successful acquisitions.
The content & opinions in this article are the author’s and do not necessarily represent the views of ManufacturingTomorrow
Comments (0)
This post does not have any comments. Be the first to leave a comment below.
Featured Product
