We are entering a new manufacturing era defined by AI, machine learning and vision, enabling us to teach machines to adapt and learn plans and move us toward a true “Lot Size 1” utopia. Automation’s next era will be defined not around volume, but around intelligence.
The Next Era of Automation Is Intelligence
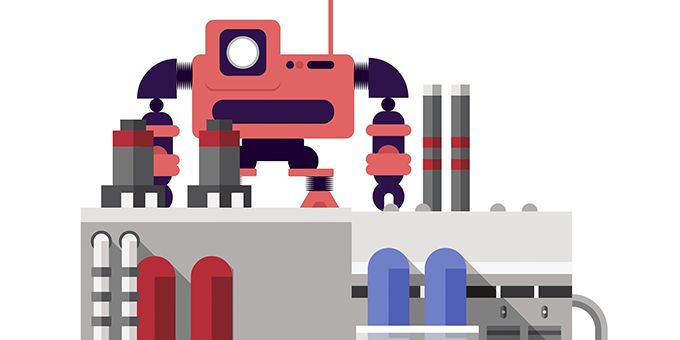
Darragh Staunton, President and COO | PaR Systems
The next era of automation is not about programming machines but teaching machines. For the last decade or more, we have programmed machines to mimic processes and movements with the goal of increasing volume and production capacity. However, when we simply tell a machine what to do, material inconsistencies and the production tolerance issues they create, hold automation’s true potential back. New technologies like AI, machine vision and learning are expanding what “automation” can do and be taught. If we really want to reinvent manufacturing, the industry needs to embrace a new mentality of teaching machines, looking beyond simply increasing volume toward building intelligence.
Over the last decade, automation has become a term that encompasses a lot, but means very little. Automation has essentially become a catch-all term for pre-programmed tasks done by a machine or robot. We tell machines what to do and they do it efficiently and at scale. Right now, around 39% of manufacturing and supply chain professionals said their organizations use robotics and automation, according to data from MHI. This adoption is only going to grow, but what if machines could be taught to do more, learning from mistakes and figuring out how to improve processes without human intervention? That new era of intelligent automation is possible today and is being driven by technologies that, many times, sit outside traditional automation investment.
Technologies such as 3D vision, LIDAR, 4D sensing and mapping, and many more have allowed manufacturers to automate systems that were previously manual. When combined, these technologies enable machines to “think” and “learn” tasks versus just do them. Take for example machining unique parts. Our team at PaR took a commercial 3D scanning technology and wrapped it with a custom algorithm that enables the machining stations to determine how to turn down unique parts. The application scans the parts to learn how much of the block is usable after it is cast and brazed, decides which model of part it would best make based on scanned features, and generates a unique machining plan ahead of each part being machined and polished.
Projects utilizing these “learning” technologies are complex, have evolved much over the years, are easy to operate, and are dependent on not just telling robots and machines what to do, but teaching them how to do a task. They’re indicative of the new, more adaptive definition of automation and it will only continue. When we expand our perspective of automation to this “learning” mentality, we can see broader benefits beyond volume and production gains:
-
The level of technical expertise across the labor force is not as high. We can free people up to define the parameters of the machine and the ways the machines should proceed or recover in those scenarios, as opposed to defining and overseeing what the machine does.
-
When we can define how a machine should proceed or recover in the manufacturing or design process, we can decrease the negative feedback loop that decreases time to market, the need to redesign, and waste resources.
-
Encourage long-term innovation by thinking beyond the status-quo of automation projects.
This new automation mentality is taking shape across the business world. The Wall Street Journal recently featured Tyson’s Arkansas robotics lab where they were developing a machine that could sort beads by color. The robot is part of an ongoing automation project to identify and cut meat parts by size, shape and color safely and efficiently. Using computer vision and software, this is as much AI as it is automation.
Now, COVID has shown us that we need to think about automation differently. From siloed knowledge centers that disappear when employees must take sick leave to reconfigured supply chains and material shifts due to the virus, the need for adaptability and intelligence has never been clearer. The future of manufacturing is only going to get more complex, connected to the supply chain and personalized to individual customer/product needs.
Technology has already eaten the world. Manufacturing is one of the final frontiers for intelligent technologies that already drive our ecommerce, marketing and social lives. Those who don’t start to invest in intelligence over volume will risk being left behind. It starts with broadening our understanding of what automation means today and where it can take us in the future.
About Darragh Staunton
With 24 years of manufacturing automation experience, Darragh has been a part of it all. He started as an automation technician at HP before solving automation problems at IBM, driving extensive sales initiatives at ATS Automation to then serve as COO of BBS Automation and build out the global expansion of BBS Automation to then move to America as head of BBS Automation Chicago operations as President. He now joins PaR Systems, LLC as COO and President.
The content & opinions in this article are the author’s and do not necessarily represent the views of ManufacturingTomorrow
Comments (0)
This post does not have any comments. Be the first to leave a comment below.
Featured Product
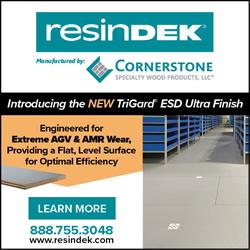