Kaleesuwari were unable to receive real-time data from the 24 line machines operating in their plant, and therefore no accurate data was being collected on production output.
Red Lion Case Study - Kaleesuwari
Case Study from | Red Lion
Edible oil is a highly competitive market. Delivering health and wellness through their superior products, Kaleesuwari is a company that prides itself on its responsiveness to customer requirements. However, they were unable to receive real-time data from the 24 line machines operating in their plant, and therefore no accurate data was being collected on production output. They were also experiencing significant challenges around workforce schedule monitoring, unable to match worker shift hours with production. The company previously tried to solve these issues by employing additional labor to manually count the production for each machine, but this led to many human errors– it was essentially guesswork on bag orders, with a great deal of raw materials being wasted.
Because of these inaccuracies, senior management made frequent visits to the plant floor to identify production inefficiencies. Relying heavily on intercommunication with their operators, concerns were manually logged into a spreadsheet – an imprecise process that provided no real actionable data that could result in a comprehensive resolution strategy.
The lack of proper production data also significantly impacted customer deliveries, ultimately affecting customer retention. As a manufacturer of Fast-Moving Consumer Goods (FMCG) products, turnaround must be rapid to remain competitive in the market.
The customer needed to obtain accuracy in its production data, avoid unplanned downtime, remotely monitor machine status, and streamline stock and production. This required a solution that would not change the existing production process but rather optimize it for better management and logging of data. To meet this challenge, there were many different elements involved, including the machines, the production team, and senior management. Moreover, it was critical to register details from the existing PLCs, presenting another challenge as other PLC vendors were involved. With the support of Kaleesuwari management, Red Lion was able to provide a solution that was quickly implemented on their production line.
SOLUTION
The team at Red Lion introduced Kaleesuwari to the concept of data mining from performing control systems, agnostic to any PLC installed. SAS Automation was used as the system integrator, supplying installation and commissioning of the system/project. Offering a trial demonstration of their full-service solution, the Red Lion team provided the production department with the functionality and features that enabled accurate production data on demand. With agnostic hardware, easy to understand visualization formats, and remote monitoring of data, Red Lion solved the customer’s challenges effectively. Kaleesuwari was excited about the comprehensive PLC connectivity provided by the PTV, regardless of the many differing PLC brands or types currently in place on the shop floor, along with multi-protocol options.
MODEL DESCRIPTION
PTV00000 ProducTVity Station: Ready-to-deploy plant floor visual management system that displays real-time Key Performance Indicator (KPI) data and Andon messages on large televisions to drive efficiency. CSMSTR Modular Controller Master with multiple protocol converter, data logger, web server with Virtual HMI up to QVGA (320 x 240) size and expansion slot CSINI800 CSINI- 8 Channel 0(4)-20 mA Input Module 108TX N-Tron Series Unmanaged Industrial Ethernet Switch: 8 port, hardened, metal, DIN-Rail enclosure designed for use in mission critical data acquisition, control, and Ethernet I/O applications RESULTS Since the implementation, Kaleesuwari has experienced many positive results. Automatic time logging with production data is helping the company understand the performance and capacity of each machine. To date, they have experienced an 8% improvement in machine output per line. However, they continue to fine-tune the process in order to gain further efficiencies from their production lines. Featuring an HMI dropdown box that lists possible reasons for a machine failure, operators simply click on the appropriate pre-programmed explanation. Management is immediately notified when a breakdown occurs, the basis for the problem, as well as contextual data for the machine, helping the company to better understand root causes and track recurring issues. Within the first 4 months, Kaleesuwari reported a 40 hours cost saving in machine downtime. Collecting production and downtime data from 24 machines, all Delta PLCs and HMIs are connected with PTVs and synced to PTV screens, allowing for remote monitoring. Kaleesuwari now has access to real-time data for raw input, packet production, oil loss, and total production output, leading to overall plant performance improvements. As a result, errors in bag counts have significantly decreased. With data accessed directly from the machine on packaging bags used, the company has experienced a 15% reduction in bag waste per line. The improvements that Kaleesuwari has seen with the help of Red Lion solutions have led to an increase in manpower efficiencies in other areas of the plant. Providing indispensable data that can help the company achieve increases in revenue and customer retention, these successes have led to discussions for further installations within the plant. With approximately 16 lines in total, the customer plans to install Red Lion’s innovative streamlining solution on at least four additional lines by the end of the first quarter 2019. While more data collection is needed to determine the impact on sales, the implementation of the Red Lion solution has opened up the opportunity for Kaleesuwari to utilize other products within the company and implement cloud-based solutions for all six of their plants. The company feels certain that, as more dedicated Red Lion systems are implemented, a true measurement of overall business impact and value will be ascertained. Today, Red Lion continues to work with Kaleesuwari for predictive maintenance and data visualization solutions.
The content & opinions in this article are the author’s and do not necessarily represent the views of ManufacturingTomorrow
Comments (0)
This post does not have any comments. Be the first to leave a comment below.
Featured Product
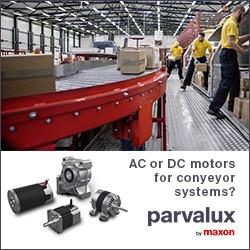