The automotive supply chain has become almost too massive to manage, leaving manufacturers and suppliers struggling to develop efficient processes to identify and prevent quality risks.
Distributed Manufacturing in the Auto Industry
Pete Butler | MS Companies
Tell us a bit about MS Companies and your role in the manufacturing industry.
We’re a data-driven technology company that provides manufacturers and suppliers with solution sets to create efficiency and agility in workforce and operational quality objectives. As founder and CEO, I set the strategic direction and lead customer-centric innovation and growth. I’ve spent more than 25 years strengthening and developing existing business models and new business ventures.
It’s no secret that distributed manufacturing environments present complex, issue-prone processes, especially across the global automotive supply chain. What are the top concerns for automakers in today’s distributed manufacturing landscape?
Automakers and their suppliers are America’s largest manufacturing sector, responsible for 3 percent of the U.S. GDP. The automotive supply chain has become almost too massive to manage, leaving manufacturers and suppliers struggling to develop efficient processes to identify and prevent quality risks. With distributed plants and locations increasing in number, it has become difficult to gauge defects, whether isolated or spanning the entire supply chain, within the more than 20,000 moving parts that go into a vehicle.
Miscommunication and disruptions from incorrect or incomplete data are often to blame as many OEMs and top-tier suppliers continue to use unreliable point-based solutions, multiple ERPs, legacy systems or basic spreadsheets to drive operations. The result is poor end-to-end supply chain visibility, latency in critical decision-making and overall operational inefficiencies that ultimately hurt productivity. Automotive executives rank visibility as the most critical means in containing costs and managing issues, so it needs to be made a priority.
From a process standpoint, what are some tangible solutions for automotive manufacturers to address these concerns and increase productivity and global profitability?
Most manufacturers and suppliers lack reliable technology that captures configurations of parts in deep granularity. They need a solution set that provides data-driven insights within an advanced hierarchy, enabling operational managers and executives to pinpoint issues and inefficiencies across multiple distributed manufacturing locations in real-time. Only a scalable, interoperable supply chain optimization platform can ensure synchronized quality performance.
This type of platform can bridge the communication gap by tying people, processes and systems together. Through data input and analysis, OEMs and top-tier suppliers can bridge digital communication to drive containment back to the source and eliminate waste. It’s crucial to collect data and allow it to flow from the bottom up through the operational pyramid to identify issue origination. This reduces issue containment time when a defect emerges.
How do these solutions impact communication capability across the supply chain – a crucial component in process efficiency?
With heavily siloed supply chains, OEMS and suppliers need a full operational picture. Without the capacity to aggregate and share data across individual operations, information becomes fragmented and negatively affects issue and resource management. Manufacturers need a digital communication tool that connects the entire supply chain ecosystem with user-friendly interfaces that allow supervisors to create, automate and track the progress of tasks and case assignments, and managers to access and configure data based on KPIs.
If a Tier 1 supplier feeding into an OEM is utilizing an employee working on multiple products, it’s nearly impossible to aggregate the data needed to identify and resolve an issue across the supply chain. To be successful, both parties must engage in the same workforce technology to gain a comprehensive operational overview. One data set means one version of the truth and one location where all engaged parties can interact in real-time.
How can these processes be implemented, and what are their specific uses across leadership/management levels?
With distributed manufacturing and supply chain environments becoming more and more complex, it’s become mission critical for enterprise leadership to drive the adoption and integration of advanced quality assurance processes and technologies that maximize efficiency, productivity and profitability. The ability to gather and utilize real-time data and alerts is key, as this helps plant and supplier quality managers to quickly identify and contain defects as soon as they emerge. Communication enablement is what ties it all together. When supervisors and managers are networked across distributed locations, it creates the ability to identify, communicate and course-correct variability in parts in synchronization.
To reiterate, what modern technologies do you see playing a pivotal role in the evolution of manufacturing efficiency and innovation? In other words, are there certain concepts/processes that stand out as being driving forces for the future of manufacturing and its complexities?
Manufacturers and suppliers must solve for the many parts of the supply chain puzzle to develop trustworthy technologies that build effective processes for the future. Cloud computing and storage, inventory and network optimization, automatic identification, predictive analytics and the internet of things will drive innovation in the coming years and should be leveraged in conjunction to thrive in today’s highly competitive marketplace.
About Pete Butler
Pete Butler is chief executive officer and founder of MS Companies, a data-driven technology company providing manufacturers and suppliers with unparalleled efficiency and agility in both workforce and operational quality objectives. Pete is an accomplished entrepreneurial business executive with more than 25 years of experience strengthening and developing existing business models and state-of-the-art new business ventures.
The content & opinions in this article are the author’s and do not necessarily represent the views of ManufacturingTomorrow
Comments (0)
This post does not have any comments. Be the first to leave a comment below.
Featured Product
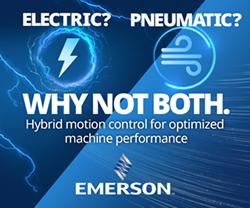