The wide variety of shapes and thinner bottles created a need for packaging machines to not only be accepting of the different sizes, but also perceptive enough not to damage the new thinner bottles.
Quick Precise Motion for the Packaging Industry Created by Nook Belt Driven Actuators
Contributed by | Nook
In order to meet the demands of a variety of consumers and retailers, bottled water packaging has taken on many different shapes and sizes. In addition to the new packaging configurations, advances in the technology used to create the plastic bottles have allowed much thinner bottles to be produced. The thinner bottle allows for a reduction in production and material costs – less material is also an environmental advantage. The wide variety of shapes and thinner bottles created a need for packaging machines to not only be accepting of the different sizes, but also perceptive enough not to damage the new thinner bottles.
APPLICATION CONCERNS
Conveyor deflectors have been used in the past, but this has been shown to damage the product due to the inertia of the product moving along the conveyor. Articulating robot arms are commonly used, but due to their large structural mass, they have limits to how fast they can process product into the correct position.
The use of Nook Industries’ three-axis gantry was not only able to realize a 20% increase in production output over the articulating robot arm, but was able to do this without damaging the product in any way.
APPLICATION SOLUTION
Nook Industries was contacted to build a robust three-axis gantry to provide the mechanics for the palletizer solution. Designing a custom gantry solution can be difficult and time consuming, however, with the sophisticated design capabilities of Nook Industries engineering group the end customer was able to cut design time and work in cooperation to check form, fit, and function of the gantry. Exchange of 3D modeled prototype designs ensured the process was smooth. The gantry itself consisted of dual QLZ-100 belt driven actuators on the base X-axis. Connected by a hollow aluminum timing shaft, the X-axis supported the dual Y-axis of QSZ-80 belt driven actuators as well as the versatile (Z-axis) ELSD-80S external belt driven actuator. ELSD-80S belt driven actuators allow the gantry to have two axis of motion in a single belt driven actuator, a vertical Z move as well as a rotational theta move. Incorporating planetary gearboxes, servo motors and drivesthe gantry system allowed the end user to modify the pallet stacking sequence without mechanical and software changes.
NOOK ADVANTAGES
- Part Number Protection
- Custom motor/gearbox adaption.
- Proven Nook Quality
- Same day response to design changes
- 3D Modeling capability with design support
CUSTOMER BENEFITS
- Seamless changeover - downtime reduction
- Gentile, quick, and precise motion
- Cost effective and on-time solution
- Complete mechatronic solution - increased customer value
The content & opinions in this article are the author’s and do not necessarily represent the views of ManufacturingTomorrow
Comments (0)
This post does not have any comments. Be the first to leave a comment below.
Featured Product
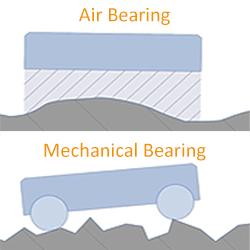