Circular Manufacturing Sets New Standards for Material Life Cycle Innovation
Industrial producers interested in exploring how to make processes and products more sustainable should turn to circular manufacturing. It is a broad priority that involves keeping products and materials in use for longer and reducing what ends up in landfills. Progressing in this evolving area often requires manufacturing professionals to prioritize material life cycle improvements.
Creating Printed Circuit Boards for Repeated Recycling
Electronic waste levels have soared as the world has become more high-tech and product prices have dropped. When people shop for new smartphones or TVs, they probably do not think about what will happen to those items at the end of their useful lives. The internal components — such as printed circuit boards — come to mind even less often. Fortunately, scientists are focusing on the issue. These efforts could alter the PCBs manufacturers use and enhance material innovations.
In one case, researchers found a solvent to convert a class of sustainable polymers into a jelly-like substance. People can then pull out the solid components to recycle them and reuse the polymer remnants to make new PCBs. Conventional polymers used to make printed circuit boards degrade significantly with each attempt to recycle them. However, this innovation could be a game-changer for material life cycle improvements.
Experiments showed this method recovered 98% of the vitrimer, 100% of the glass fiber and 91% of the solvent used for recycling. This process was also safer for those handling the components and the environment. Conventional material-extraction methods involve burning, contributing to the overall waste and releasing toxins.
Recognizing Customers’ Material Life Cycle Contributions
Efforts are also underway to use normally discarded items as the foundation for new products or to change material innovations to make things easier to break down or recycle. Additionally, some manufacturers have launched return programs that enable customers to participate directly in the process. Product return-point contributions allow supply chain partners to remove usable materials from old items. Otherwise, usable materials could end up in landfills rather than becoming part of the circular economy.
Manufacturers and engineers have already made innovations in other ways, such as finding various feasible use cases for particular materials. Carbon black is an excellent example. Auto manufacturers have incorporated it into the parts of car interiors that touch the skin because it provides ultraviolet protection and absorbs those rays. It can also add pigment to material more cost-effectively than some other options. Carbon black’s pigmentation capabilities influenced why manufacturers selected it to play a primary role in a specific circular manufacturing improvement.
Patagonia — an outdoor brand well-known for its sustainable initiatives — has partnered with a third-party service provider that will begin processing end-of-life wetsuits made of natural rubber. The external company will break the material down to the molecular level and create carbon black to dye future versions of those garments. The raw materials then go to Patagonia’s supplier, returning them to the supply chain without requiring additional resource usage.
Carbon black also comprises 15%-20% of the rubber foam used in the material. Consumers can bring their used wetsuits into any Patagonia store or mail them back to the company for processing. Those options are ideal because they are simple and reinforce how anyone can participate in the circular economy.
Lengthening Material Life Cycle Timelines
Improving material longevity sometimes means designing products to last longer or facilitating repairs at home. Many consumers like both these options because they allow using things for longer, which can enhance attachment and loyalty. However, manufacturers and engineers must work together to determine the best ways to maintain or elevate customer satisfaction while meeting other goals.
Indeed, sustainability improvements related to material longevity or other aspects may encourage shoppers to purchase specific brands over others. Customers may continue supporting the respective companies over time because they appreciate their commitment to responsible improvements.
One study found that one-third of consumers began choosing different food and grocery brands because of sustainability. Some may be drawn to businesses that strategically reduce waste associated with products they use for years, such as cars or furniture.
Decision-makers at an automotive brand opened a circular factory and prioritized processing end-of-life vehicles to optimize the associated environmental impacts. Employees categorize parts depending on their suitability for repurposing, recycling or remanufacturing. All components undergo a comprehensive validation process that partially determines how to treat them.
For example, company representatives may return reusable parts to the marketplace through parts distributors. However, the automaker intends to recycle raw materials such as copper and steel, replacing those with virgin materials in the supply chain as much as possible. Executives’ estimates about this initiative suggest that the facility will recycle approximately 10,000 vehicles per year, extending the usage of about 120,000 parts. Additionally, these efforts will recover 8,200 metric tons of steel and 300 metric tons of high-purity plastic.
Since these efforts keep materials usable longer, professionals must continually examine new options for increasing longevity and durability.
Assessing the Most Viable Options
Producers have many things to assess as they examine how to improve materials. How long will people use the product on average, and in what environments? What are the main shortcomings of current options, regardless of whether those downsides relate to sustainability?
Design teams can support these manufacturing innovations using dedicated tools to determine how and why products break down prematurely or which materials are the best choices to meet specific needs and goals. Those insights can improve production methods by increasing visibility and minimizing trial and error.
One European Union-funded project tasks participants with finding viable ways to increase the circularity of additive manufacturing and machining processes. Some project phases center on simulation and validation tools to identify options early to save time and resources. This initiative will also develop several platforms, including one with digital tools that support users in renewing, remanufacturing, repairing, or recycling materials and products.
Those controlled environments are essential for giving people the freedom and flexibility to experiment before committing to major changes. The associated insights can give them more confidence and knowledge to enable material and manufacturing-related innovations.
Supporting Ongoing Progress
Finding material improvements that will work effectively and align with other company goals can take time, collaboration and substantial resources. However, these fascinating examples show the many opportunities to consider, keeping professionals motivated.
Comments (0)
This post does not have any comments. Be the first to leave a comment below.
Featured Product
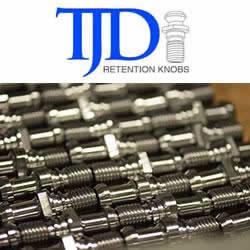