Avoiding the Pitfalls: The Biggest Mistakes Manufacturers Make When Creating a Smart Factory
Smart factories have become an integral part of the modern industrial landscape as Industry 4.0 solutions continue to shape the manufacturing industry. Smart factories promise higher production, efficiency, and cost-effectiveness using cutting-edge technologies, such as the Industrial Internet of Things (IIoT), Artificial Intelligence (AI), robotics and data analytics. However, manufacturers frequently run into several obstacles that can prevent them from successfully implementing smart factory technologies. In this article, I will delve into the most common errors manufacturers make when working to create a smart factory, along with advice on how to prevent these mistakes.
Lack of Clearly Defined Objectives and Strategy
One of the most significant errors made is starting the process of building a smart factory without a clear plan in place. Business leaders must first examine what precise goals they are looking to accomplish. This is crucial, regardless of whether the objective is to increase production efficiency, decrease downtime, improve quality control, understanding and reporting on greenhouse gas (GHG) emissions or simplify supply chain management. Before making significant investments in technologies, a thorough strategy that reflects the company’s long-term vision and addresses potential roadblocks must be established.
Neglecting Cybersecurity Measures
Smart factories comprise various interconnected systems and devices, posing significant cybersecurity vulnerabilities. Unfortunately, some manufacturers assume that intelligent technologies are inherently secure and downplay the significance of solid cybersecurity procedures. Smart factories are vulnerable to data breaches, intellectual property theft, and operational disruptions if they are not well protected. Strict cybersecurity policies must be in place, including encryption, access controls, recurring audits and employee training, to preserve the factory's digital infrastructure.
Ignoring Compatibility and Operability
Another common mistake is ignoring the compatibility and operability of different technologies within the smart factory ecosystem. Management will spend money on stand-alone solutions that don’t work well with current systems or updates. As a result, data silos form, hindering thorough data analysis and limiting the smart factory’s ability to reach its full potential. A unified and adaptable smart factory environment is supported with standard protocols and ensures that technologies communicate efficiently.
Deprioritizing Employee Training and Engagement
A competent and flexible workforce is essential to a successful smart factory implementation. Neglecting employee education and participation during the beginning phases can lead to detrimental issues. At first, workers may be reluctant to adopt new technologies because they fear losing their jobs or don’t comprehend the advantages. Personnel should have access to comprehensive training programs to operate and maintain the smart factory. Employees will adopt a more positive attitude and sense of ownership if they are included in decision-making and process improvements.
Overemphasizing Technology, Underemphasizing Data
Although a smart factory’s foundation is built on advanced technologies, these systems are only as valuable as the data they produce and analyze. It would be a grave mistake for manufacturers to prioritize using cutting-edge equipment while paying insufficient attention to data gathering, management, and analysis.
The Road to Smart Manufacturing
Smart factories offer a road to unmatched efficiency and productivity gains as the manufacturing sector transitions to a more connected and intelligent future. However, establishing a smart factory is a challenging task that demands careful planning and thought. Manufacturers can prepare for a smooth transition to an innovative and agile production environment by avoiding the most frequent mistakes, such as setting clear objectives, prioritizing cybersecurity, ensuring technology compatibility, investing in workforce training, and leveraging the power of data. Adopting Industry 4.0 and implementing a successful smart factory strategy would put manufacturers at the forefront of the industrial revolution.
Comments (0)
This post does not have any comments. Be the first to leave a comment below.
Featured Product
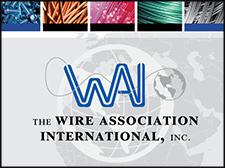