It’s clear that the way humans have traditionally been used in manufacturing is neither good for the industry nor for these individuals. This truth has been overlooked with apprehension about what change will mean for millions of workers in the industry.
The Redesign of Manufacturing is Inevitable: What Does it Mean for Humans?
Lukas Pankau, CEO, | Industrial Next
Manufacturing has reached a critical turning point as industry leaders grapple with today’s evolving demands. From rising labor costs to widespread supply chain disruptions - the industry has an unprecedented need for more efficient processes. However, it has become clear that traditional manufacturing is no longer capable of addressing these challenges. As manufacturing is inevitably re-designed to prioritize truly intelligent automation over repetitive labor - what does this mean for the human workforce?
Traditional Manufacturing Over the Years
Since the introduction of factories, humans have been performing repetitive tasks. While this may have been adequate in the past, these monotonous roles have proven to not only be inefficient but also fail to tap into the innate strengths of humans. Humans are just not built for these repetitive, labor-intensive motions that leave many susceptible to workplace injuries.
It’s clear that the way humans have traditionally been used in manufacturing is neither good for the industry nor for these individuals. This truth has been overlooked with apprehension about what change will mean for millions of workers in the industry. While there is the belief that advanced automation will replace the current workforce, this is fortunately not the case. A majority of humans will not be replaced by technology but instead moved around to take on more sophisticated tasks.
A New Role for the Human Workforce
These labor-based jobs that are replaced by autonomous manufacturing don’t disappear entirely. They can be moved to other parts of the factory where the human hand can do particularly better than machines. For example, humans are fantastic at manipulating objects in tight spaces - something that machines are typically not capable of. Labor then moves from repetitive and injury-prone jobs to more maintenance-focused jobs. The maintenance and oversight of autonomous equipment will always require humans.
As advanced automation becomes more widespread, there will also be a greater demand for jobs that are higher-skilled, yet are still accessible by the current workforce. “Smart labor” or “AI trainer” are likely to become an emerging profession in the industry. These positions do not require the advanced education that AI scientists have but will work alongside AI to supervise its results and guide its training.
Embracing Innate Human Strengths
Not only does this address the re-organization of labor in the industry, a collaborative approach to manufacturing will help to drive efficiencies to new heights. Humans are particularly good at design and development of products and manufacturing processes, as well as tasks that involve creativity, critical thinking, problem-solving, and pattern recognition. These are all incredibly important skills in manufacturing, yet automation - no matter how advanced - will likely not be able to compete at the same level.
Ultimately, human strengths will always fill gaps where automation falls short. The most powerful use of autonomous technology will be in partnership with humans, as AI will always require training and supervision. For instance, an experienced human could make an AI system much more powerful by properly flagging when automated processes make mistakes or do suboptimal routines.
New Opportunities for Talent
In addition to these roles that the current workforce can be trained to take on, the industry will inevitably bring countless job opportunities for new, higher-skilled talent. As intelligent automation is widely implemented, there will be an increased need for in-house AI and ML specialists with more advanced education and background. These individuals will be critical for troubleshooting issues with technology on the spot or have the ability to communicate problems with autonomy providers to troubleshoot remotely.
Another area for growth we may see emerge in the future are human-centered roles around designing unique, customized products for consumers. As advanced automation enables manufacturers to integrate more customization and adapt to small changes in their processes, mass production is no longer limited to uniform products. This demand for more customization is already here, and intelligent automation will bring this capability to the industry at a larger scale.
At the bottom line, the field is inevitably changing, and we cannot continue to do things the way we’ve done them before. As truly intelligent automation is implemented at scale, the manufacturing workforce will not look the same in the future as it does now. While some may fear this change and question the impact it will have on the current workforce, it's important to understand that the strengths humans have can never be replaced by technology. By combining these strengths with the countless benefits of intelligent automation, we can unlock the true potential of manufacturing and propel the industry forward to the next level.
About Lukas Pankau
Lukas Pankau is the co-CEO of Industrial Next, a company creating autonomous manufacturing for car manufacturers and other producers. Prior to his current position, Lukas was the lead electrical architect behind Ford’s Global Fusion and Edge platforms, and Tesla’s Model X, 3, and Y. In his five years at Tesla he transitioned to lead next-generation Autopilot hardware architecture and special projects in the Fremont factory focusing on autonomous manufacturing.
The content & opinions in this article are the author’s and do not necessarily represent the views of ManufacturingTomorrow
Comments (0)
This post does not have any comments. Be the first to leave a comment below.
Featured Product
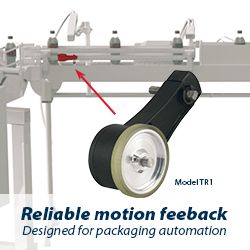