In a time when the whole world is re-evaluating the way they do business, it is essential that industries utilizing Smart Factory and automated solutions do not become over-reliant on technology to get the job done.
Post-Pandemic Operations Must Incorporate Real People into the Automation Process
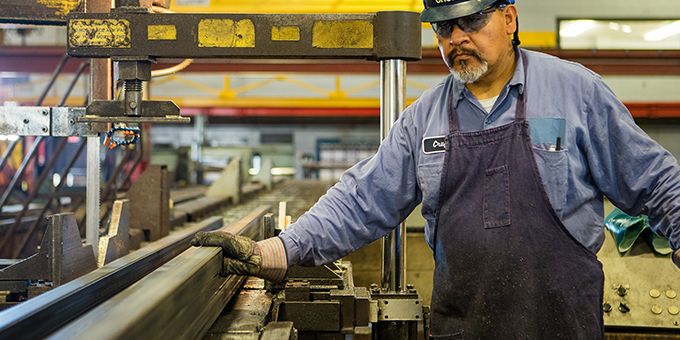
Franco van Heijningen, Vice President of Strategic Operations | CREAN, Inc.
The COVID-19 pandemic has proven to be a pivotal moment for the technology and automation industries. With the absence of non-essential workers, businesses are recognizing their ability to automate operations – eliminating job opportunities. In a time when the whole world is re-evaluating the way they do business, it is essential that industries utilizing Smart Factory and automated solutions do not become over-reliant on technology to get the job done.
Experts have often speculated whether human beings will remain relevant in industries quickly becoming automated by machines and Smart Factory solutions, but the truth is, people are the most essential part of any business operations equation. Though the implementation of Smart Factory technology is becoming increasingly popular for streamlining many processes, we must remember that Smart Factory technologies are not, nor should they ever be, a one-size-fits-all solution.
When industry leaders don’t take the time to truly assess an individual company’s priorities, it undermines the ongoing success of those who do Smart Factory solutions the right way. Focusing solely on the technology solutions will not result in successful implementation. It starts with the people, not the tech.
Before folding in the technology, you must have the right people and processes involved in order to reach the highest level of Operational Optimization. Ongoing conversations with your client will result in a more accurate, holistic picture of their operations’ current status quo. A substantial amount of data must be collected and analyzed prior to any tech implementation. Without a clear picture of a customer’s needs and areas of improvement for operations, fitting the strategy and technology behind a Smart Factory solution is nearly impossible.
Identifying exactly which areas of operations and processes need to be optimized is key to successful implementation. You need to do your homework, so to speak, and find out how Smart Factory technology best fits into a business’ daily operations.
Understanding the nuances of a business’s operations, structure, and areas of weakness are key to ensuring you provide the most customized and curated approach for implementing Smart Factory technology. If everyone isn’t on board, the likelihood of successful operations is slim. I have outlined below the most important takeaways to consider in order to be successful in implementing Smart Factory solutions.
Start at the end.
Like so many other things in life, you always need to start with the end in mind. Develop a clear, solid list of goals for your project. When we work with clients, we review their goals at every meeting and address changes immediately. You must continuously remind yourself and your team what success looks like.
Processes always change with new technology.
No matter what tech you install, the process will change, so focus on the process proactively. Obvious changes such as the implementation of automation or control technology, should be preceded by performing detailed process analysis and capacity optimization to craft how the tech fits into the process. It is important to know that even just collecting data and changing what you measure will result in changes in what people focus on which will change the performance of your operations processes.
Focus on the environment, not just the tech.
Having the right expertise and consulting the right people is essential to selecting the most appropriate solutions. Every environment has special considerations that need to be taken into account, just as every company will have different needs, different operations, and different challenges. It’s important for business leaders implementing Smart Factory solutions to understand this isn’t exclusively a tech activity just like it’s not exclusively an operations activity. It requires a holistic approach for the team. Even when you’re implementing a technology-centric project, success requires integrating people and process with that technology into how you think about that integration.
If you change the tech, you change everything.
The right technology solution is often the easiest part for tech-focused companies, but also easy to make mistakes in an ever-evolving tech space. You have to make sure your tech is capable of achieving the goals of your client. Company leaders need to recognize that if you change the technology in the process, you’re changing the entire process.
For example, if you change from manual inspection to automated inspection with an expectation of a 20% improvement in productivity, you will only see those results if that inspection is 20% slower than the rest of your operation. Another process step with the same production rate as the manual inspection process may keep you from seeing any gain from your new automation technology. That is why it is imperative that you understand, analyze and optimize the full process to meet your goals. Although implementing tech to improve any one aspect of the operation may be a near-term goal, ultimately, you need to improve the operations as a whole, otherwise you’re wasting time, money and resources.
Your people must be at the heart of your solution.
Successful people are at the heart of every major change in business. You can’t have a successful transformation without the people helping implement it. The people are the ones who will learn how to operate in the new system. It’s important to know tech solutions need to be people-centric not tech-centric, so people are brought into the solution, not victims of the solution. Every successful tech transformation begins with thoughtful leadership and succeeds through the integration of the people into the Smart Factory solution.
Making people central to your transformation will pay huge dividends. Although many claim AI will mean we need fewer workers, similar claims about the productivity gains from the Internet have yet to come true. While the nature of work has changed, the Internet revolution has enabled us to develop new products and services we had not conceived of in the early days. Now Smart Factory and AI will enable the next revolution – allowing you to compete in a world that begins delivering products and services we have yet to imagine.
About Franco van Heijningen
Franco van Heijningen is the Vice President of Strategic Operations at CREAN, Inc. With executive experience in Global Operations Management, Franco has led cornerstone projects in industries including international technology, construction, engineering and aviation. His main drivers are operational excellence, cost reduction, innovation as well as cross-functional and cross-cultural leadership. Franco’s wide breadth of industry exposure includes Facilities Management, IT, Security, Engineering, Construction, R&D Management and Manufacturing.
The content & opinions in this article are the author’s and do not necessarily represent the views of ManufacturingTomorrow
Comments (0)
This post does not have any comments. Be the first to leave a comment below.
Featured Product
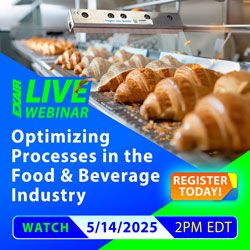