A Competitive Alternative to Traditional Linear and Rotary Position Sensors.
Jens Kautzor | Hoffmann + Krippner Inc.
Since the filing of its patent application in 1985, the membrane potentiometer has experienced many interesting advancements and has established itself as a prominent technology within the market.
Due to its flat design and voltage divider circuits, the membrane potentiometer is applicable in the same fields as the traditional potentiometer. This white paper first introduces the available types of membrane potentiometers and their respective advantages and disadvantages, and then outlines the spectrum of applications for membrane potentiometers.
The Concept
Fundamentally, a membrane potentiometer consists of a resistive path that is printed onto a membrane base, and a collector with a printed short-circuit path that is applied on top of this base. Both paths are separated by a circumferential spacer.
When pressure is applied to the collector foil, electrical contact is simultaneously applied to the resistive path and a voltage can be tapped into movement via the collector foil. Once the pressure being applied to the collector foil ceases, the voltage can no longer be tapped. This characteristic must be kept in mind when operating the membrane potentiometer manually; however, when a wiper or magnet is used, the voltage remains constant.
The Material
The membrane is comprised of polyethylene terephthalate (PET), which is a thermoplastic material (plastomer) that can be molded within a specific temperature range. Since this shaping process is reversible, the procedure can be repeated an unlimited number of times by cooling and reheating the material, as long as the thermal decomposition of the PET material is not damaged due to overheating. The critical temperature for materials used in membrane potentiometers is approximately 73°C.
PET’s ability to be molded has implications for membrane potentiometers. When a wiper is pressed statically onto the collector foil that has been heated beyond the critical temperature subsequent to its cooling, a permanent deformation could occur at the pressure point. Depending on the circumstances, this deformation could cause anything from a slight change in linearity to permanent contact between the resistance and collector path. This effect is known as the denting effect.
There are membrane potentiometers available that operate beyond the thermoplastic point of temperature, though. This category of membrane potentiometers is discussed in the following section.
Denting Effect
A membrane potentiometer is always operated mechanically with the collector foil. When the wiper experiences prolonged periods of standstill at high temperatures, the collector foil can become dented; however, whether or not these dents have an impact on the application and to what degree depends upon various factors. These factors include the temperature and surface pressure, the wiper’s shape and the length of exposure. Appropriate information about how to avoid this effect is usually provided by the manufacturer.
A PET-based material can withstand temperatures of up to 100°C, but static pressure should not be applied to the collector foil at temperatures above 60°C. Therefore, manufacturers have developed different technologies to exceed this limitation (refer to ‘Hybrid Potentiometers’). These consequences do not usually occur when the wiper is operated dynamically and the potentiometer is used according to specifications, though.
Adhesive
Adhesives are used in the production of membrane potentiometers to connect their different layers, as well as to attach the potentiometer to its customized support structure. In most cases, a single- or double-sided acrylic adhesive with a thickness ranging from 50 to 200 µm is used.
Commonly used transfer adhesives are suited for a temperature range of -40°C to 150°C, and a service temperature of about 90°C. They can resist storage in water for approximately 100 hours, and are also resistant to most oils, fats, aliphatic solvents and weak acids, as well as to fuel, salt and alkali. Furthermore, the adhesives are usually UV resistant.
The adhesive’s shear and peel strengths are quite high and depend on the type of support structure in use (e.g. PET acryl or aluminum acryl) and the surrounding temperature. Since the adhesive softens as the temperature increases, it can be removed easily. Details regarding adhesive force shall be requested from the respective manufacturer.
Characteristics of several membrane potentiometers
PET membrane potentiometer
In this class of membrane potentiometers, the resistance layer, spacer, and collector foil are made of various thicknesses of PET material, depending on the application and the manufacturer. The thickness of the film is usually between 60µm and 190µm, while the overall height is less than 600µm.
The PET membrane potentiometer is usually operated by using a mechanical wiper with a surface pressure ranging from 0.7N to 3N, but the potentiometer can also be operated by hand. Due to the material’s physical characteristics, the operation temperature ranges between -40°C and 60°C.
Kapton membrane potentiometer
Kapton is a thermosetting polyimide (PI) that can be operated continuously under temperatures up to 230°C, or even as high as 400°C (temporarily). A PI is much more dimensionally stable than PET and can be treated in a reflow oven. The potentiometer layout matches the PET potentiometer’s layout; however, its production is more expensive. In terms of the denting effect, Kapton potentiometers only show a slight improvement when compared to PET potentiometers.
Membrane potentiometer with SET function
A membrane potentiometer equipped with the SET function allows the last set value to be stored—even when someone’s finger or wiper is no longer activating the collector foil. These potentiometers are mainly used in applications requiring manual operation (input systems with an integrated membrane potentiometer). A value is set by applying slight pressure. The set function can be realized electronically or via a special doping, which allows for large areas up to DIN A4/US letter.
Hybrid membrane potentiometer
Hybrid membrane potentiometers are made of a combination of different materials, and they exhibit differences depending on the manufacturer.
-
Base and spacer made of PET, collector foil made of a thicker, foil-like material: Very inexpensive with a slightly delayed denting effect. The operating temperature falls into a range between -40°C and 65°C. Limited use for static applications.
-
PET base, collector foil made of FR4 (usually between 80µm and 150µm thick): Considerably delayed and reduced denting effect, but higher wiper pressure possible (3N to 5N). Operating temperature range between -25°C and 75°C.
-
Base and collector foil made of FR4 with a thickness of up to 150µm: The operation temperature can reach up to 85°C, but a wiper surface pressure of 3 to 5N is required. The denting effect is significantly delayed.
-
PET base, collector foil made of a flexible metal: This new alternative exhibits a high level of resistance to the denting effect; however, a wiper surface pressure of 2 to 6N is required. The temperature ranges between -25°C and 85°C.
Magnetic membrane potentiometer
The magnetic membrane potentiometer utilizes a magnetic field and therefore contactless connection. Different designs have evolved and are listed below, but for almost all variants, the magnet can provoke a tap either from the top through the collector foil, or from the bottom through the enclosure.
-
PET base, ferrite band on top of the collector: Pulled by the magnet, the ferrite band presses down onto the collector foil. The upper operation temperature can be specified to be a little higher (about 70°C); otherwise the same characteristics as for the PET potentiometer apply. This technology was introduced to the market in 2004.
-
PET base with a wiper between the foils; the wiper is moved by a magnet: The magnetic retention force can be less than what is required for a potentiometer with a ferrite band, and the distance between the magnet and potentiometer can be greater. The internal wiper is abrasive, resulting in the potentiometer’s limited lifetime. Operating the potentiometer without hysteresis is not possible because the internal wiper is pulled by the magnet.
-
PET base with inserted flexible magnetic metal strip: Only minimal information exists on this new technology; however, its properties are similar to the potentiometers with a PET base and a ferrite band on top of the collector.
-
PET base with conductive ferrite band: This variant is under development, but the magnetic force is presumed to be as small as necessary to trigger a reed contact.
FR4 membrane potentiometer
Almost all models mentioned above can also be produced with a FR4 base instead of PET. Some of the advantages of FR4 include better overall operation, an improved resistor paste (manufacturer-specific), and a simplified attachment of connectors or wires with the ability to integrate the complete circuitry into the PCB.
The respective printing of the potentiometer directly onto the PCB, the populating of the components, the soldering, and the applying of the collector foil with integrated spacer are further benefits. The extent of temperature resistance depends on the material used for the collector. Different collector materials exist in combination with FR4 PCB’s, often made of very thin PET or FR4, among them the before mentioned flexible metal foil.
Frequently Asked Questions (FAQ)
Is a membrane potentiometer sealed?
A membrane potentiometer is sealed, with a few exceptions. Most sealed potentiometers, especially those featuring a smaller design, cannot establish pressure compensation when the wiper presses down onto the collector foil.
When significant changes in air pressure occur, a sealed potentiometer is usually only suitable for limited use. The SENSOFOIL ® HYBRID membrane potentiometer is an exception, however. The short distance of only a few micrometers between the resistance path and the collector path, combined with the low level of pressure that develops within the potentiometer, can cause contact between both layers. In most cases, an integrated valve serves to adjust pressure, although this usually reduces the level of tightness to IP54 or lower, depending on the design. While other solutions are possible, they require more space.
Depending on their design, membrane potentiometers can withstand water for a short period of time. After a while, though, the adhesive can dissolve, since almost all adhesives are water-soluble. Furthermore, the membrane materials used are hygroscopic.
What are the wiper’s properties and conditions?
It is important for the user to understand that a membrane potentiometer is only considered a potentiometer when it is combined with a wiper or magnet. Only the connection between the collector path and the resistance layer results in a variable voltage divider.
Typical materials for wipers include delrin, brass, or nickel silver. The user should pay attention to the material combination with the foil. Ideally, the wiper should be of a spherical design and mounted with flexibility. When using a ball wiper, special attention must be paid to its rounded edges and parallel running. The wiper’s width should be between 10% and 15% of the resistance path’s width. A longer spring deflection should be chosen if high resistance to shock and vibration is required.
In the case of a magnetic operation, the conditions are quite different. The magnet’s diameter can exceed the resistance path’s width. Of particular importance are the force that is applied and the ferromagnetic material that is selected for the ferrule.
Magnets are characterized by their energy density, a value (e.g. N52) that is comprised of remanence (kG = kilo Gauss) and coercivity (kOe = kilo Ørsted). This value does not give information about the starting power, which depends on the magnet’s mass, the distance to the ferrule, nor the ferrule’s material properties.
In general, the following applies to the wiper: its force has to be great enough to operate the collector foil. The force depends on the type of magnet in use, but usually it falls into a range between 0.75N and 3N. When the value is given in milliTesla (mT), it is required that the exact distance, the magnet’s direction and diameter are also specified. Generally, the manufacturer can provide more precise recommendations.
How small can a potentiometer be?
A potentiometer is made of three or more parts that are glued together. The width of the required adhesive edges has to be at least 2 mm to ensure proper bonding. The adhesive’s flow characteristics must be taken into consideration when applying. For this reason, the bonding surface should be 5 mm wide. The spacer should be 3 mm larger on each side when compared to the resistance layer, resulting in the following dimensions: adhesive edge, 2 x 5mm; resistance layer width, 6mm; spacer edge, 2 x 3mm. These dimensions combine to equal a total width of 22mm. A smaller width of 12 mm is only possible if certain specifications can be altered.
Technical Parameters
The different operational temperatures were mentioned earlier in this white paper. Additional technical parameters that users frequently inquire about include life cycle, repeat accuracy, hysteresis, resolution, repeatability, and errors due to linearity.
Life cycle: The life cycle depends on the technology and wiper being used, as well as the wiper’s design and contact pressure. Please refer to the chart for average values. The life cycle is either stated in movements (one time travel over a minimum of 90% of the active area) or cycles (one time travel back and forth over a minimum of 90% of the active area). Typically, a change in linearity of >10% is considered the end of the potentiometer’s life-cycle.
Repeat accuracy: Repeat accuracy describes the user-defined approach of a given position that must always be carried out from the exact same direction.
Hysteresis: Hysteresis indicates the difference in signal that occurs when a defined position is approached from one direction; this position is then passed and re-approached from the opposite direction. A potentiometer’s hysteresis depends on its mechanics. The same applies to a membrane potentiometer – the wiper in use defines the hysteresis.
Resolution: Resolution results from the resistance layer’s grit size (level of homogeneity) and the distribution and the wiper current, among other factors. The resolution at optimal wiper tracking is indicated as infinite.
Repeatability: Repeatability describes any approach of a specified position from different directions. It demonstrates the sum of two times the resolution plus hysteresis.
Errors due to linearity: Linearity shows the deviation of a membrane potentiometer’s output voltage from a specified theoretical function. The “independent linearity error” is the maximum deviation of the output voltage’s curve from an ideal line. This is a well-known aspect of quality, but to most users, repeat accuracy or hysteresis may be more important. As long as the gradient is positive, a poor linearity can still achieve a good repeat accuracy.
Applications
This section presents several applications typical for membrane potentiometers. The advantages and disadvantages to each application differ by application and the potentiometer being used. Therefore, a consultation to optimize your desired application is advisable. Generally speaking, a membrane potentiometer with a length of up to 700 mm is an economical alternative to a traditional potentiometer. Rotary membrane potentiometers with diameters up to 400 mm are also relatively inexpensive to manufacture.
Sealed Front Panel
Membrane potentiometers are well-suited for use in fully-sealed front panels with control elements (set point devices). The potentiometer can either be integrated into a membrane keypad (manual operation), or a turning knob provided with a magnet can be welded to a stud. The magnetic potentiometer is attached to the panel’s reverse side and is activated by the magnet in the turning knob.
Flap Adjustment
For this application, electronics are usually arranged close to the control element. Therefore, the conductive layer can be printed directly onto the circuit board. The collector foil is affixed after populating the PCB. One advantage is that the conductor paths are located on the board.
Distance Measurement in Cylinders
Magnetic potentiometers (potentiometers operated by a wiper) are located inside the cylinder in order to detect linear positions.
Actuators
Membrane potentiometers can be linear or rotary, but can also be adjusted to different shapes. Usually, the encoder can be removed due to the high accuracy for correctly dimensioned potentiometers.
Robotic Systems
Generally, a decision will need to be made on a case-by-case basis; however, because of their long life-cycles, the use of a magnetic membrane potentiometer is recommended. When exposed to fast movements, the potentiometer must be adjusted.
Forklift
Expensive conventional potentiometers used in a controller can be replaced by membrane potentiometers. Additionally, switch functions can be integrated into membrane potentiometers.
Joystick
In dirty, unstable environments, a membrane potentiometer based on FR4 can be used to protect the resistance layer.
Ribbon Controller
Moving a finger over a game console creates control signals while data is simultaneously output as Midi signals.
Medical Science
Various applications for membrane potentiometers can be found in medical science; for example: in syringe pumps (perfusion pumps) for extremely slow movements, in laser technology for control and accuracy, in input systems (antimicrobial surfaces are possible) or in prosthodontics to increase reliability.
Door and Gate Systems
Both linear (e.g. in streetcar doors) and rotary systems (e.g. in barriers to detect their actual position) can be used without having to reset the systems in the event of a power outage. To a certain extent, the encoders that are typically used can be removed due to the membrane potentiometer’s accuracy.
Summary
Because of its ultra-flat design and flexible usage, combined with cost advantages, the membrane potentiometer has opened up sensing possibilities which were not possible before. With new and innovative materials like magnetic operations or hybrid membrane potentiometers (such as the patented “Sensofoil Hybrid” by Hoffmann + Krippner), designers and engineers can use this potentiometer in many applications. Complex sensor constructions can be reduced, simplified and integrated less expensively with modern membrane potentiometers.
The Hoffmann + Krippner Group, with sales offices around the globe, specializes in input and output systems as well as sensors. Headquartered in Germany, Hoffmann + Krippner has manufactured German-engineered, high quality products for over 35 years. As the North American member of the Group, Hoffmann + Krippner, Inc. delivers these engineering, design and manufacturing services to the US and Canadian market.
As of 2014, Hoffmann + Krippner, Inc. has partnered with Altmann GmbH (manufacturer of high-precision potentiometers), Inelta GmbH (manufacturer of LVDT and load cells), and PIL GmbH (manufacturer of ultrasonic sensors).
The content & opinions in this article are the author’s and do not necessarily represent the views of ManufacturingTomorrow
Comments (0)
This post does not have any comments. Be the first to leave a comment below.
Featured Product
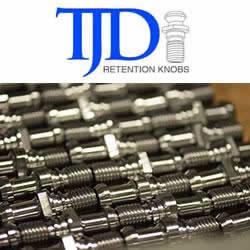