The Sky's the Limit: Additive Manufacturing in Aerospace Will Soar with Parts Certification
Additive manufacturing (AM) is taking flight in the aerospace industry, revolutionizing how aircraft parts are produced. One reason for the recent adoption of AM in aerospace is the advancement of materials. The introduction of a wide range of materials, including high-temperature materials, is enabling production of flightworthy parts capable of withstanding extreme conditions, like temperatures over 350F.
AM also brings the dual benefits of reducing prototyping time and production costs. Simply put, additive can lower the cost of making aircraft. Conventional manufacturing methods come with substantial material waste, sometimes as high as 98%, due to its subtractive process and the lengthy procedure of mold creation. Additive manufacturing, on the other hand, is, well, additive. It works by building a part, not cutting it from a block. This significantly reduces waste and leads to substantial long-term cost savings. AM also enables the production of aerospace parts with complex geometries, eliminating the need for separate assembly and reducing lead time and energy consumption.
And then there's the issue of maintenance costs. Some manufacturers charge the moon for spare parts far beyond production costs. If you're an airline, you must pay that price because you need spare parts to do your regular maintenance. But if you have a 3D printer in-house, you can print your own spare parts on demand and save a lot of money in the long run.
For these reasons and more, the aerospace industry has become a hotbed of AM innovation, with the global aerospace 3D printing market projected to grow from $2.94 billion in 2022 to $8.35 billion by 2029.
That's impressive—and the potential is there for even greater growth. But before AM can capture its full share of the flight-ready end-part manufacturing market, it must first resolve the thorny issue of parts certification.
Liftoff depends on certification
Aerospace is a challenging industry for any manufacturer. Aerospace parts have incredibly intricate designs and must meet stringent quality-assurance standards that are above and beyond what other industries require. If even one small part is deemed unsafe, it can ground a commercial aircraft and lead to millions of dollars in losses. This is to ensure the passengers, pilots, cargo and the aircraft safety.
These quality assurance and parts-certification issues are coming to the fore in the AM industry now that more and more aerospace companies are shifting away from conventional manufacturing and adopting additive manufacturing. Aircraft manufacturers and operators over the years have invested heavily in certifications and all of them are on conventional manufacturing methods and some on materials that are deemed not safe anymore for cutting and milling operations. However, it is challenging to move away immediately since the certification is key for safe operation.
Certifying AM parts for commercial aircraft remains tricky due to various technical and regulatory factors. For instance, the aerospace industry has long-established standards and practices for the traditional manufacturing methods it has always relied on. But AM often uses novel materials and alloys that may not have established standards for aerospace applications. Ensuring these materials' consistency, quality, and performance is crucial for certification, and developing industry-wide standards has been a gradual process.
A critical step is meeting the strict requirements of aviation regulatory authorities, such as the U.S. Federal Aviation Administration (FAA) and the European Union Aviation Safety Agency (EASA). Certifying additive parts based on regulations put forth by agencies like these require extensive data collection, analysis, and simulation to demonstrate the performance of the parts under a wide range of conditions.
Several strategies and measures can be implemented to achieve these steps. For instance, we're already seeing the use of sensors and machine learning models to monitor the printing process and ensure that 3D prints meet expected standards. Additionally, real-time monitoring and feedback mechanisms can be used in the AM process to detect internal flaws and quickly take corrective action. These range from simple notifications to a full-blown report of predicted failure points and part properties without NDT (Non Destructive Testing).
By implementing these strategies, AM manufacturers can ensure their parts meet the reliability and consistency standards of the certification process. The strategies are vital to gaining regulatory approval and attaining confidence from the aerospace industry.
On several fronts, systems are already go
A measure of AM's potential is its use in aerospace applications soaring even as it works toward established standards. The space industry, for example, is turning ever more to additive manufacturing to reduce the weight of the parts and components that go into orbit. Launching vehicles into space is exorbitant—around $10,000 per pound. With space vehicles containing millions of moving parts, even a slight reduction in their size can significantly reduce overall weight and significantly cut costs.
Notably, SpaceX has been at the forefront of embracing additive manufacturing. It has successfully designed 3D-printed rocket nozzles using advanced alloys, and its continuing adoption of 3D printing enables SpaceX to achieve unprecedented progress in the industry and speed up its ultimate goal of putting people into space.
The U.S. Air Force also uses AM for tooling, maintenance, and repair and creating flight-certified parts, aiming to save millions of dollars. The Air Force faces continuous pressure to quickly repair aircraft and promptly return them to operational status. This is increasingly difficult as aircraft age due to the scarcity of replacement parts, as well as the reluctance of manufacturers to produce parts that may not be reordered for many years.
This means that ordering individual parts can be a costly and cumbersome process. The Air Force is flying over that hurdle by implementing a 3D-printing platform that enables the rapid production of on-demand parts and streamlines the certification process for new materials, making them viable for use more quickly.
As additive technology moves forward, the horizon is broad, and the skies are clear. AM will continue to dramatically impact the aerospace industry in the years ahead, revolutionizing production practices and dramatically lowering costs.
Comments (0)
This post does not have any comments. Be the first to leave a comment below.
Featured Product
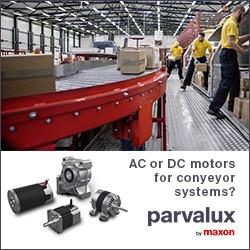