Rocket Propulsion Company's 3D-Printing Lab Delivers First Rocket Engine Components
Ursa Major, America's only privately funded company that focuses solely on rocket propulsion, delivered its first copper-based 3D-printed rocket engine combustion chambers out of its additive manufacturing (3D-printing) lab in Youngstown, Ohio, compressing the production and delivery cycle to one month, compared to a minimum of six months using traditional manufacturing processes. These advanced copper alloy-based engine components will be tested for space launch and hypersonic applications.
"Speed is of the essence when it comes to producing rocket engines right now because lack of propulsion is causing a significant bottleneck in U.S. access to space and hypersonics testing," said Joe Laurienti, founder and CEO of Ursa Major. "The Ursa Major facility in Youngstown is playing a pivotal role in accelerating our customers' time to market in both commercial and government sectors."
The Ursa Major Advanced Manufacturing Lab began in October of 2021, with $3 million in federal financial support from U.S. Rep. Tim Ryan and Department of Defense-backed manufacturing innovation institute America Makes. The Lab's charter is to develop and test additive manufacturing (3D printing) processes and materials for Ursa Major's rocket engines, used for both space launch and hypersonic applications.
"Ursa Major's goal to help establish the U.S. as a global supplier of rocket propulsion is in line with our efforts to foster domestic innovation and manufacturing across industries in Ohio," said Rep. Tim Ryan. "I'm pleased that Youngstown is home to this state-of-the-art facility that will ultimately help the U.S. regain its leadership in space and hypersonic technologies."
The Youngstown-based facility is equipped with an EOS large-format laser powder bed fusion 3D printer designed to make on-demand components for Ursa Major rocket engines. It is located in the Youngstown Business Incubator, an internationally recognized program focused on the development of software and additive manufacturing companies in the region.
"This type of advanced additive manufacturing is a great example of the kind of American innovation that America Makes seeks to support," said John Wilczynski, Executive Director of America Makes. "Successful projects like this are part of a resurgence in American manufacturing that helps strengthen our domestic supply chain."
The existing supply chain for high temperature metal alloy components is limited, and it can take months to turn around a needed revision. The Advanced Manufacturing Lab accelerates the engine development process, allowing Ursa Major to rapidly iterate on design adjustments in-house to improve engine performance and reliability.
The Advanced Manufacturing Lab was critical to rapidly redesigning Ursa Major's "Ripley" from a 35,000 to 50,000-pound thrust engine in order to meet market demand. The technical lessons learned from Ripley and the methods and materials produced in this facility are now contributing to the development and testing of their two other rocket engine programs – the "Hadley," a 5,000-pound thrust, oxygen-rich staged combustion engine used in small launch and hypersonics, and the recently announced 200,000-pound thrust "Arroway" designed for medium and heavy launch.
3D printing allows Ursa Major to speed up engine production and apply improvements gleaned from testing in real time, lowering costs. Ursa Major's rocket engines are more than 80 percent 3D-printed by mass and primarily built and tested in its Berthoud, Colorado headquarters.
Ursa Major's flexible rocket engines can be used for a range of missions, from air launch to hypersonic flight to on-orbit missions with many restarts. The company's customers get to launch many years faster and without the development cost of building engines in-house. Ursa Major has built and tested more than 50 staged-combustion rocket engines to date and plans to deliver 30 customers by year's end. To date, Ursa Major engines have accumulated more than 36,000 seconds of run-time, far more than a typical engine is tested prior to first flight.
Connect with Ursa Major on LinkedIn, Twitter, Instagram and Facebook.
About Ursa Major
Ursa Major is America's only privately funded company that focuses solely on rocket propulsion, bringing high-performance, staged combustion engines to market for space launch and hypersonic applications. Ursa Major customers, ranging from "New Space" startups to enterprise-level aerospace leaders and the U.S. government, get to flight faster, more reliably, and cost-effectively. The company employs the most sought-after engineers from top space programs and universities and is backed by world-class investors including XN and Explorer 1 Fund. Headquartered in Berthoud, Colorado, Ursa Major was named one of the best places to work by Built in Colorado two years in a row. For more information, visit www.ursamajor.com.
Comments (0)
This post does not have any comments. Be the first to leave a comment below.
Featured Product
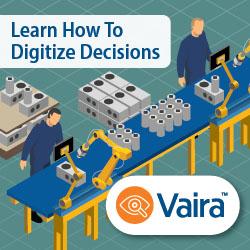