COVID-19 Accelerates Digitalization in Manufacturing But Data Silos Must Go!
When the manufacturing industry emerges out of the COVID-19 pandemic, we will see the rapid trend of digitalization. However, to achieve maximum success - this will only happen if manufacturers finally deal with the challenge of data silos!
Kari Terho, the General Manager of Elisa Smart Factory, the industrial data analytics specialist company, acknowledges that data silos are typical in manufacturing. However, they are also a major hindrance to manufacturing digitalization for operations prepping for the ‘new normal’ after COVID-19.
In this article, he explains why digitalization is critical post-COVID-19 and how manufacturers can tear down their data silos for optimum business sense!
How has COVID-19 Changed the Manufacturing World?
Due to the COVID-19 pandemic, thousands of suppliers, manufacturers, and their customers have suffered material losses. Productions and shipments have slowed down and even stopped.
We've seen epidemics, pandemics, and other global disruptions several times before. What's so different this time around?
Earlier global disruptions have only affected some specific, typically offshored manufacturing parts of the supply chains in Asia. The damages were then signalled upstream, hit manufacturers and companies elsewhere, eventually stopped productions, and canceled shipments globally.
COVID-19, however, is the first pandemic, which has directly and simultaneously impacted multiple parts of the supply chains globally. The unthinkable has become a reality for many manufacturers. Their primary plants have had to be closed down, and this has impacted on the alternative back-up plants and suppliers. The members of staff have been locked-down.
For the first time in manufacturing history - demand, supply, and workforce availability are affected, simultaneously.
Why is Digitalization in Manufacturing the Answer Post-COVID-19?
According to the industrial data and tech company, Thomas, two-thirds of North American manufacturers are planning to bring production and sourcing back to the American continent. This is also known as reshoring. Because of the high labor costs in Europe and the US, the success of production reshoring will depend on fully-automated, robotized, and data-driven manufacturing systems.
Consequently, digitalized factories with a minimum of on-site staffers are likely to trend quickly post-COVID-19.
Why did the effects of the COVID-19 pandemic drive manufacturers onto their knees? It wasn't just the halted production lines, it was the simultaneous staff lockdowns, measures of social distancing, and other employee safety procedures. Manufacturing requires people to physically be on-site. Operators keep an eye open and run machines, while maintenance staff maintains and repairs them. Many factories are not designed to be managed remotely and lack the digital tools and infrastructure that are needed to support such activities. Consequently, according to Gartner, up to 50 percent of the production workforce has been unavailable during the pandemic.
It is clear that the "new normal" will require smarter ways of working, and also a higher degree of digitalization in manufacturing – such as a "virtual shift" – a team of specialists who connect remotely to be available 24/7 to supervise processes, guide and support the reduced personnel present on-site.
What is the Major Hurdle to the Success of Digitalized Manufacturing?
Quite simple, it is the obstacle of data silos. Many manufacturers have first-hand experience of working in an organization, packed with silos.
There are several stakeholders involved: from procurement to material planning, production planning, sales, finance, fulfillment, and more. These teams are working in their own silos; they have siloed processes, databases, systems, and dashboards. While these might work individually, the systems do not communicate well across department borders.
The production machines generate massive amounts of valuable data, also. However, this data is very difficult to collect, due to the various machine-specific formats and interfaces, which has resulted in all the important data left to reside in isolated silos. The information cannot be correlated, cross-referenced, combined, or harmonized to give an important end-to-end view on the manufacturing process, inventories, and material flows.
These silos prevent manufacturers from efficiently advancing their digital transformation!
How Can We Break Down the Walls of Data Silos?
Start by gaining access to the data residing in the silos – i.e. production machines, systems, and other departments. This data, which is in different formats, will have to be harmonized, integrated, analyzed, and then opened for use by various applications, such as a digital twin, or a performance monitoring platform.
In practice, this will involve connecting machines and core systems - such as ERP, MES, PLM, and automation systems via a purpose-built smart factory analytics layer. This will handle the continuous stream of data, generated by the machines and systems. It will collect, integrate, and analyze all the structured and unstructured data that has been collected from an unlimited number of sources.
This will result in valuable insights and can be created simply by integrating the disparate data points. The ERP systems will tell operators the inventory levels and delivery lead times; MESs will track and manage manufacturing information in real-time, to provide information gems about traceability and performance; and the PLM systems will include all the information, related to a specific product, from concept to production.
Once all data is merged, a manufacturer can then gain a solid foundation for optimal digitalization. Production lines can be automated and robotized; and management will have full control over the manufacturing processes, even if they are based in remote locations. Maintenance needs can be predicted and better managed.
Can the virtual and physical shifts collaborate efficiently?
Yes, if they can see the production area, lines, and machines on a visual, online 3D digital twin. The digital twin factory is based on real-time data, and it shows what is happening in the "real" factory, either on a specific line, or a machine at any given moment – so that operators and management can make fact-based decisions.
Can managers and supervisors keep an eye on the processes when locked-down at home?
They can. It works, by working with role-based performance dashboards, which collect data from all data sources and display it on a single intuitive view.
Managers can monitor the production KPIs e.g. net run time, yield, first pass yield, and DPMO (defects per million opportunities), and compare these against set targets, in real-time. Supervisors have end-to-end visibility of the inventories, machines, and processes via performance dashboards, and can optimize material flows continuously.
Digitalization makes manufacturing more resilient against severe disruptions by facilitating flexible ways of working. New manufacturing tools can include digital twins, remote diagnostics, preventive maintenance, predictive analytics, virtual collaboration, and more.
In Conclusion
COVID-19 has pointed out hard lessons to manufacturers. We now realize that production is highly networked – and components and raw materials are sourced from all over the world. Despite this, global supply chains are fragile. Factories cannot be dependent on staff being on-site physically, any longer. Learning can be positive, although now, it is the result of a devastating disease.
When manufacturers soon emerge from the downturn – they will be fully digitalized, more resilient, efficient, and flexible – and ready for the new normal!
About the Author:
Kari Terho is the Director and Head of Smart Factory at Elisa Corporation, the leading ICT service provider in Finland. Prior to joining Elisa Smart Factory, Kari held various leadership positions in service management and was responsible for sales and business development at tier-one wireless service providers, and at global blue-chips - including Hewlett-Packard. Kari holds a Master of Business Administration.
About Elisa Smart Factory:
Elisa Smart Factory is a leading provider of artificial intelligence and industrial IoT software for industry manufacturers. We connect to any data source, harness streams of data, and combine data analytics and machine learning to create outcomes like increased uptime, production quality, and yield. Being part of Elisa corporation, we have decades of experience in managing vast, highly automated network infrastructures as well as predicting and preventing disruptive incidents. Our aim is to use this expertise and become the leading provider of factory digitalization solutions in Europe and beyond. For more: https://www.elisasmartfactory.com/Comments (0)
This post does not have any comments. Be the first to leave a comment below.
Featured Product
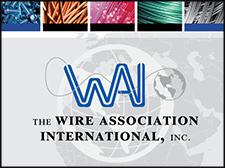