Green Cubes Demonstrates Suite of Lithium Battery Solutions at MODEX 2024
As electrification of material handling equipment continues to gain traction, Green Cubes offers new battery and charger technology roadmaps and best practices to ensure safety and sustainability for electric fleets.
Green Cubes Technology (Green Cubes), the leader in producing Lithium-ion (Li-ion) power systems that facilitate the transition from lead-acid batteries and Internal Combustion Engine (ICE) power to green Lithium-ion (Li-ion) battery power, today announced it will demonstrate its suite of Lithium SAFEFlex Batteries and Chargers, including its recently announced Lithium SAFEFlex PLUS Batteries, SAFEFlex Chargers and Industrial Swappable Batteries at MODEX 2024 in booth B2607. Green Cubes will also present a roadmap for the latest sustainable technology for material handling best practices and results from the adoption of Lithium-ion batteries in material handling equipment. The presentation is on Wednesday, March 13 at 11:30 a.m. in the Sustainability Theater.
For over 35 years, Green Cubes has been on the forefront of electrification innovations. The company recently celebrated a decade of motive power technology leadership for material handling and ground support equipment with its flagship suite of Lithium SAFEFlex Battery solutions, designed to meet the cost, performance, efficiency, and durability requirements of the rugged warehouse, distribution, and airport environments. For more information, visit: https://greencubes.com/products/batteries/
Green Cubes will demonstrate its suite of Lithium SAFEFlex Batteries and Chargers at MODEX 2024 in booth B2607. Green Cubes will also present a roadmap for the latest sustainable technology for material handling on Wednesday, March 13 at 11:30 a.m. in the Sustainability Theater.
With an enhanced feature set developed based on 10 years of experience with the groundbreaking Lithium SAFEFlex product line, Lithium SAFEFlex PLUS is a comprehensive battery solution designed to meet the cost, performance, efficiency and durability requirements of the rugged warehouse environment. FBP2 series Lithium SAFEFlex battery systems are high cycle life, low maintenance solutions for industrial vehicles with a broad specification range to fulfill the most demanding requirements. The modular design facilitates family safety certifications and the drop in replacement batteries make upgrading from Lead Acid to Lithium simple. The batteries are sized to fit the standard material handling lead acid battery compartment, along with meeting the truck battery weight requirements. For more information, visit: https://greencubes.com/product/safeflexplus/
The Lithium SAFEFlex Battery Charger is designed to operate with Material Handling (MH). This charger has universal AC power input and CANBus communications with the battery, has a touchscreen display, provides unity power factor with very low iTHD which results in very high charging efficiency, and has the smallest footprint in the MH industry. For more information, visit: https://greencubes.com/product/lithium-safeflex-chargers-fbc-series/
The Green Cubes swappable battery platform is a complete pre-engineered energy storage power system available to industrial workstation manufacturers to save time and money for their product's system design. The battery, power system controller and charger enable electrification of non-powered OEM mobile workstations. For more information, visit: https://greencubes.com/product/24v-industrial-swappable-battery-2440/
On Wednesday, March 13 at 11:30 a.m. in the Sustainability Theater, Green Cubes will present a roadmap for the latest sustainable technology for material handling best practices and results from the adoption of Lithium-ion batteries in material handling equipment. Robin Schneider, Director of Marketing of Green Cubes, will profile emerging battery and charger technology and present a case study, with an emphasis on demonstrating what benefits enterprise customers recognized when they implemented Lithium-ion platforms. Lithium-ion batteries have become an increasingly common choice for powering material handling equipment (MHE), from larger Class 1 forklifts to smaller Class 3 pallet jacks. Now that Li-ion batteries have an attachment rate with electric MHE estimated between 15 and 25 percent, the technology has changed from an early adopter novelty to mainstream. With Li-ion technology, fleets will have a lower total cost of ownership and achieve environmental and sustainability goals, taking advantage of incentives and vouchers. However, to make the transition seamless, it is important to understand the best practices in implementing this technology.
About Green Cubes Technology
Green Cubes Technology develops and manufactures safe and reliable electrification solutions that enable its OEM and enterprise customers to transition from Lead Acid and Internal Combustion Engine (ICE) power to Lithium-ion battery power. Green Cubes utilizes proven hardware and software platforms to build the most reliable Lithium power solutions in its industries. With over 300 employees across six countries, Green Cubes has been producing innovative, high-performance and high-quality power solutions since 1986.
Featured Product
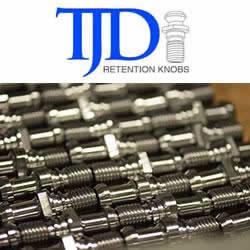