Presenting the World’s Fastest Photonics Alignment Systems for SiPh Chips at Photonics West
Experience high-speed alignment engines, a new way to improve laser micro-hole drilling, air bearing-based wafer stages, high-resolution focusing devices, and microscope stages at BIOS/Photonics West in San Francisco, Booths 8517 / 3517, January 27 – February 1, 2024.
Auburn, MA - With its proprietary Fast Multi-Channel Photonics Alignment Algorithm (FMPA) and specialized high-precision mechanics, PI helps customers to improve production economics to participate in the rapidly growing Silicon Photonics market. PI has been continuously expanding its range of automated photonics alignment engines over the last decade and will introduce new systems at both ends of the spectrum at this year's event. A new, modular entry-level system based on mechanical stages, yet with a high-performance controller will be presented, as well as high-speed, air-bearing based systems for test and assembly applications requiring the highest throughput with zero wear and maintenance.
The global demand for SiPh components is currently growing dramatically, and leading market research companies unanimously predict a quadrupling of the SiPh component market to around $10 billion by 2030. Productivity, throughput, and manufacturing costs are therefore increasingly in focus. One of the major cost drivers is the precise alignment of optical fibers to the photonic elements of the chips. This task plays a crucial role both in production-related quality control and in coupling with optical fibers for assembly. Depending on the complexity of the end products, the alignment must be repeated up to two dozen times in the manufacturing process.
The time required for this is crucial for the throughput and cost of SiPh production and very second saved per alignment can be worth millions over a production run. With PI's proprietary algorithms and mechanics, alignment time can be reduced up to 99% compared to legacy approaches.
In addition to well-known solutions such as the F-712 alignment family, consisting of a hybrid combination of hexapods and piezo-based nanopositioners, the new air-bearing-based F-142/F-143 alignment systems and the F-836 entry-level system are now available.
Additional Solutions for Life-Sciences, Semiconductor Manufacturing, Laser Communication, and Laser Processing
In addition to photonics alignment engines, PI will also present wafer stages for the semiconductor industry, actuators for quantum computing optical paths, fast focusing stages for laser applications, nanopositioning and nanofocus devices for super-resolution microscopy, a new, piezo-based method of increasing throughput in laser micro-hole drilling and fast steering mirrors for free space optical laser communication on earth and on LEO satellites.
PI's modular architecture supports the mixing of motion and drive types in one system, allowing each axis to be optimally equipped in terms of cost and performance. Control is carried out via expandable EtherCAT-based controllers from ACS, a company of the PI Group.
Can't make it to San Francisco to experience our technology? You can look at a variety of performance automation, photonics, and nanopositioning applications covered by PI system technologies »here. https://www.pi-usa.us/en/news-events/virtual-product-demos/?utm_source=Cision&utm_medium=email&utm_campaign=ONLET_Cision_email_2024-01_PW-2024-pg
Industries Served
Silicon Photonics, Semiconductors, Laser Processing, Microscopy, Life Sciences
Featured Product
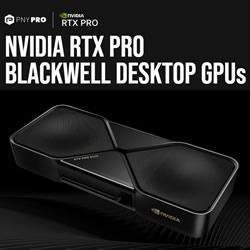