New Multi-Axis Alignment System for Silicon Photonics Automation Applications, from PI
Achieve first light search and alignment up to 100X times faster.
Auburn, MA - PI's family of photonics alignment automation systems has expanded with a new air-bearing-based multi-axis assembly and an EtherCat-based high-performance motion controller with embedded alignment algorithms. The unique combination of direct-drive maintenance-free air bearing alignment stages with sophisticated first light search and alignment routines result in extraordinary time savings - a critical factor in silicon photonics alignment automation.
How the Alignment System Works
The F-143 alignment system is based on three A-143 air bearing stages in an XYZ configuration. Each axis provides a travel range of 25mm, with a maximum velocity of 250mm/sec, and acceleration up to 10m/s2. Preloaded air bearings guarantee exceptional flatness and straightness of 0.25µm and 0.05µm, respectively. The vertical axis stage is equipped with an adjustable counterbalance and brake mechanism to offset the force of gravity on the motor and prevent potential collisions with a SiPh wafer in the event of a power failure.
A special, EhterCat-based motion controller with embedded photonics alignment algorithms and user-friendly software allows the system to perform alignments up to 100 times faster than conventional optical alignment engines.
Wear-Free and Clean-Room Compatible
The use of friction-free, wear-free, and maintenance-free components along with the absence of lubricants makes the air bearing automated alignment system ideally suited for silicon photonics waver probing and other clean-room applications.
Absolute Encoder Option
A key feature of these stages is the choice of encoders, including absolute and incremental options. Absolute encoders provide explicit position information, facilitating precise determination of each angular position without the need for incremental counting. This feature ensures immediate availability of position information upon power-up, enhancing operational efficiency and safety.
Industries
Served industries include optics, photonics, silicon photonics.
Featured Product
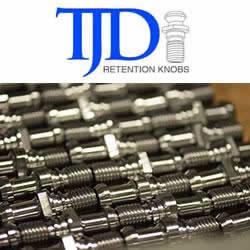
T.J. Davies' Retention Knobs
Our retention knobs are manufactured above international standards or to machine builder specifications. Retention knobs are manufactured utilizing AMS-6274/AISI-8620 alloy steel drawn in the United States. Threads are single-pointed on our lathes while manufacturing all other retention knob features to ensure high concentricity. Our process ensures that our threads are balanced (lead in/lead out at 180 degrees.) Each retention knob is carburized (hardened) to 58-62HRC, and case depth is .020-.030. Core hardness 40HRC. Each retention knob is coated utilizing a hot black oxide coating to military specifications. Our retention knobs are 100% covered in black oxide to prevent rust. All retention knob surfaces (not just mating surfaces) have a precision finish of 32 RMA micro or better: ISO grade 6N. Each retention knob is magnetic particle tested and tested at 2.5 times the pulling force of the drawbar. Certifications are maintained for each step in the manufacturing process for traceability.