HORIZON SET TO DEMONSTRATE ITS UNIQUE PROPRIETARY MICRO AM COATING PROCESSES AT FORMNEXT 2023
Adding non-metallic conductive and metallic coatings opens up the power of micro AM for numerous applications such as electrodes and electrical connectors, 3D microfluidic devices, MEMs and optics packaging, and cutting-edge mm-wave antennae, filters, mixers, and similar components.
(31st October 2023, Karlsruhe, Germany) With Formnext 2023 just a few days away, Horizon Microtechnologies is making final preparations for the show. The company will be exhibiting alongside leading micro-AM innovator Boston Micro Fabrication (BMF) on stand B38 in Hall 11.1, and will be showcasing micro-AM parts on the stand that have enhanced functionality through the addition of Horizon's non-metallic conductive, environmentally resistant, and metallic coatings.
Adding non-metallic conductive and metallic coatings opens up the power of micro AM for numerous applications such as electrodes and electrical connectors, 3D microfluidic devices, MEMs and optics packaging, and cutting-edge mm-wave antennae, filters, mixers, and similar components. It is also possible to use the conductivity to eliminate the risk of static discharge. Adding environmental resistance to micro-AM produced parts (or a range of parts/materials derived from more conventional machining processes) is important because it enables the creation of microscale devices that are more durable, reliable, and better suited for use in harsh environments such as in the presence of aggressive chemicals and/or high temperatures. This can lead to improved performance and longer lifetimes for these devices, making them more suitable for use in a wide range of applications.
CEO at Horizon, Andreas Frölich says, "As Formnext gets closer, we are increasingly excited to engage with visitors after a hugely important year for our company which has seen us receive early-stage funding tailored for innovative tech start-ups. This has allowed us to bring the full technology infrastructure for our 3D microfabrication printing and coating processes in-house which has created enormous advantages for our customers who can access a truly vertically integrated solution partner that can support them from design through manufacturing to delivery in a one-stop-shop fashion."
Horizon's post-process coating technologies exploit the usefulness of a precisely made 3D microstructure (the template) for hitherto unserved areas of industry. Typically, the templates are derived from polymer micro-AM processes but parts from different machining processes and consisting of other materials can also be inserted into Horizon's coating process chain. Adding functional coatings to the template microstructure via the company's proprietary coating processes overcomes the functional limitations of the polymer material from which the micro-AM part is made. This "best of both worlds" approach is a real game changer for industry and broadens the versatility of micro-AM in an array of applications.
Frölich continues, "Our in-house coating technologies can wholly or selectively coat micro-AM parts. By so doing, we effectively open up the resolution, tolerances, weight saving possibilities, geometric complexity, and other attractive features of polymer micro-AM for applications where it is otherwise not appropriate due to the polymer's material properties.
Our post process coating technology is unlike any other on the market, and allows us to offer unique possibilities when adding metal, non-metallic conductivity, or environmental resistance to micro-AM parts. We welcome the opportunity to discuss the possibilities this can open up for visitors at Formnext, and we value the opportunity to forge new relationships with customers to expand the use of AM into new application areas."
Horizon is exhibiting on the BMF stand at Formnext having recently invested in the BMF S240 machine which comes from the company's 10μm series of micro AM solutions, an ideal option for Horizon where the requirement is for ultra-high resolution, accuracy, and precision. The purchase of the machine means that Horizon is positioned to work with customers at various stages in the product development cycle, with the in-house infrastructure to act as an end-to-end product development and contract manufacturing partner that is able to influence the design of micro AM parts to optimise them for end-use functionality and for the application of its proprietary coating technologies.
Horizon and BMF invite Formnext visitors November 7-10 to come along to stand B38 in Hall 11.1 to see the future of micro AM and its disruptive capabilities.
www.3dmicrofabrication.com
Featured Product
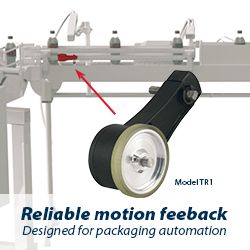