How Barcodes and RFID Deliver Value to Manufacturing and Distribution
Supply chain operation is a process that defines the methodical inflow of goods and materials to companies, retailers, and manufacturers. Asset monitoring, outbound storehouse, inbound storehouse, particulars returned are some of the cases involved in the supply chain process. Businesses can manage their supply chain process by integrating it with barcodes and RFID for manufacturing.
Combining barcode and RFID (radio frequency identification) with a relational database enhances the speed and delicacy of business processes. It can also boost a company's development by optimizing supply and refining the manufacturing processes. With significant growth in supply chain productivity, stakeholders can concentrate on other vital conditioning. In this composition, we will discuss about barcodes and RFID for manufacturing.
What's Barcode Technology?
Barcode technology is a system of garbling data in a visual pattern that can be read by electronic bias. Barcodes are generally used to track inventory, identify products, and streamline checkout processes in retail surroundings. still, barcodes can also be used to track means and people in logistics operations. RFID technology uses radio waves to communicate information between bias. RFID markers are frequently used in confluence with barcodes to give fresh data about an asset or existent. These markers can be read at a distance, which makes them well- suited for tracking large figures of particulars in storages or supply chain operations. Barcode and RFID technology can be used together to produce comprehensive tracing results for today's logistics challenges. By using the strengths of both technologies, businesses can ameliorate asset visibility, optimize supply operation, and reduce functional costs.
What are RFID Systems?
RFID systems are used to track and manage supply in a variety of sectors. RFID markers are attached to products or packed holders, and the label's data is read by an RFID reader. This allows businesses to track their supply in real time, which is essential for effective logistics operation. There are two main types of RFID systems active and unresistant. Active RFID systems use battery- powered markers that emit a signal that can be detected by a reader up to 100 feet far. Passive RFID system markers don't have a power source and calculate on the energy emitted by the reader to activate the label. These markers have a shorter range but are much less precious than active markers.
RFID technology has numerous benefits over traditional barcode-grounded tracking systems. RFID markers can store further data than barcodes, and they can be read without a line of sight, making them ideal for tracking supply in storehouse surroundings. Also, RFID markers are more durable than barcodes and aren't fluently damaged or destroyed.
The Challenges Barcodes and RFID Systems Addresses
There are numerous challenges that need to be addressed when it comes to managing supply in a storehouse. One of the major ones is keeping track of what is on hand and where it's located, which can be delicate when there are hundreds of particulars per position. Also, since each item has its own barcode, tracking them collectively becomes nearly impossible without using RFID technology.
How Barcodes and RFID for Manufacturing Give Results
Barcodes and RFID for manufacturing industry are getting highly popular as solutions for logistics challenges. Here is a look at how these technologies can help break some of the most common issues faced by manufacturing professionals:
Supply Operation
Barcodes and RFID markers can be used to track supply situations in real- time, making it easy to reorder inventories when demanded.
Asset Tracking
By attaching barcodes or RFID markers to means, you can quickly and fluently detect them if they are lost or stolen.
Shipping and Entering
These technologies can be used to automate shipping and entering processes, thus, ensuring that products are duly tracked and reckoned for.
Security
Barcodes and RFID markers can help discourage theft and fraud by furnishing a visible interference and helping to track particulars if they are stolen.
What's the Difference Between Barcoding and RFID?
Barcodes and RFID for manufacturing using technologies are both ways to automate the process of reading and landing information about particulars in stock. With barcoding, you use a barcode to automate the process of reading and landing information about particulars in stock. RFID uses radio waves to automatically identify and track particulars without visual contact. It's one of the most popular forms of tracking technology nowadays because it offers numerous benefits over traditional styles. For example, manual scanning or manual- tagging products with stickers (which can be delicate).
How Barcode and RFID can Ameliorate Supply Chain Productivity
- Barcode and RFID checkup reduces manual tasks by automatically storing product information. It also saves labor costs and increases productivity by barring paperwork.
- Barcode and RFID scanning automates the data entry process and reduces the compass of human errors. Digitally stored data therefore enables businesses to effectively manage their orders, supply, and shipments.
- Barcodes and RFIDs enhance supply visibility by furnishing perceptivity into the materials coming by and out. Attaching RFID label or barcode marker enables manufacturing companies to track mobile and fixed means in real- time.
- Barcode and RFID can be integrated with database software to detect means in real- time. It also tracks supply from accession to disposal and reduces inspection time.
Advantages of a Barcode and RFID Enabled Supply Chain
- Barcode markers and RFID reduce manual errors significantly by automating data collection
- RFIDs enhance functional effectiveness by reading multiple markers contemporaneously
- All RFID markers can be linked incontinently and matched with details stored in the database.
- The use of barcodes and RFIDs is effective for locating means in the assigned
- RFIDs can be integrated with active scanning and fixed compendiums to track supplies automatically.
- RFIDs supports label reading, whereas barcodes identify products with the aid of scanning.
How Barcodes and RFID Systems Help the Supply Chain
Barcodes and RFID systems are important tools that help the supply chain function easily. Barcodes are used to track stocks and keep track of products as they move through the supply chain. RFID markers can be fixed to products and used to track their movement through the supply chain. Both barcodes and RFID markers give data that can be used to ameliorate the effectiveness of the supply chain. Barcodes are used to track supply situations and product locales. This information is essential for managing the inflow of products through the supply chain. By knowing where supply is located, businesses can make sure that products are available when demanded. By tracking product movement, businesses can identify issues and backups in the supply chain. RFID markers give more detailed information than barcodes. RFID markers can store information about a product's origin, destination, and history. RFID data can also be used to ameliorate client service by furnishing businesses with real- time visibility into their inventory situations.
Final Study
Barcodes and RFID systems help businesses manage their inventory situations and product locales. These systems give essential data that can be used to ameliorate the effectiveness of the supply chain. Whether you are a logistics company, an e-commerce retailer, or an agricultural supply company, Aeologic Technologies have got things for you. Our barcode and RFID technology results can help your business flourish, by reducing the time it takes to get products from one point to another.
Featured Product
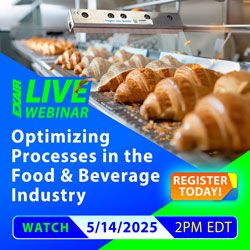