How Computer Numerical Control (CNC) Machining Turns Design Ideas into Reality
In the intricate dance of industrial innovation, CNC machining emerges as a revolutionary manufacturing marvel, transforming the way we bring designs to life. At the heart of CNC manufacturing lies a sophisticated symphony of technology, precision, and automation that orchestrates the seamless interaction of tools and machinery.
What is Computer Numerical Control (CNC) Machining? A Revolutionary Manufacturing Marvel!
In the intricate dance of industrial innovation, CNC machining emerges as a revolutionary manufacturing marvel, transforming the way we bring designs to life. At the heart of CNC manufacturing lies a sophisticated symphony of technology, precision, and automation that orchestrates the seamless interaction of tools and machinery.
Prowess of Pre-Programmed Precision:
CNC machining leverages the power of pre-programmed computer software, a technological wizardry that transforms complex three-dimensional cutting tasks into a symphony guided by a single set of digital commands.
CNC Symphony: Picture a virtual conductor directing an orchestra of industrial tools—the precision of grinders, finesse of lathes, and versatility of mills and CNC routers—all dancing in harmony to the digital tune. This prowess of pre-programmed precision sets CNC machining apart as a transformative force in modern manufacturing.
Decoding the CNC Machine Programming Language:
When a CNC system is activated, a magical unfoldment occurs. Desired cuts are meticulously programmed into the software, initiating a mesmerizing sequence where the code generator assumes flawless mechanisms, elevating manufacturing precision to unprecedented levels.
G-Code Mastery: At the core of CNC programming is the language of control, known as G-code. This alphanumeric language dictates the behaviors of machines, a digital script that orchestrates speed, feed rate, and coordination.
Open/Closed-Loop Machining Systems: The Precision Redefined:
Precision takes center stage in CNC manufacturing, and the distinction between open and closed-loop systems becomes crucial. Closed-loop systems, by receiving real-time feedback, redefine precision by enhancing error correction in the ever-evolving dance of position control.
Mastering Precision:
Dive deep into the world of open and closed-loop systems, understanding their pivotal role in achieving CNC machining precision. In closed-loop systems, irregularities in velocity and position are meticulously rectified, setting a new standard for industries where consistency is non-negotiable.
Automation, the Heartbeat of CNC Machining:
Automation becomes the heartbeat of CNC machining, where design concepts seamlessly transition into tangible creations. Computer-Aided Design (CAD) conceptualizes intricate drawings, and Computer-Aided Manufacturing (CAM) translates them into CNC-executable code—a collaborative symphony that ensures precision and efficiency.
Orchestrating Excellence:
Explore the intricacies of CNC machining automation, witnessing how CAD and CAM collaborate seamlessly. This automated symphony not only ensures precision but also streamlines the manufacturing process, turning abstract ideas into tangible realities with unparalleled accuracy.
Decoding CNC Machine Programming: A Symphony of Precision
When a CNC system is activated, the magic unfolds as desired cuts are meticulously programmed into the software, dictating corresponding tools and machinery to perform tasks akin to a well-coordinated robotic ensemble. This is CNC programming in action, where the code generator assumes flawless mechanisms, despite potential errors, elevating manufacturing precision to unprecedented levels.In the intricate world of CNC machining, precision is not just a goal.
Automated Precision in CNC Programming:
CNC programming is the heartbeat of the automated nature of CNC machining. It's the language that transforms digital instructions into tangible actions, dictating the behavior of machines with an unwavering commitment to precision.
Pre-Programmed Excellence: Imagine a conductor crafting a musical score where every note is pre-determined, every instrument plays in perfect harmony. Similarly, in CNC programming, speeds, feed rates, and coordination are pre-programmed, leaving nothing to chance, and reducing human intervention to a minimum.
The G-Code Language:At the core of CNC programming is the G-code language. It's the alphabet of CNC machining, where each command represents a specific action—whether it's the speed of a tool's movement, the rate of material removal, or the exact coordinates of a cut.
G-Code Mastery: Delve into the intricacies of G-code, where strings of numbers and letters become the conductor's instructions. The G-code ensures that the CNC ensemble follows a predetermined script, achieving a level of precision that surpasses traditional manual machining methods.
Flawless Mechanisms Despite Potential Errors:CNC programming assumes flawless mechanisms, even in the face of potential errors. The magic lies in the ability to anticipate and correct deviations through meticulous programming, ensuring that the CNC continues its performance with unwavering accuracy.
Precision Assurance: Explore the automated assurance of precision in CNC programming. While human error is inherent in manual operations, CNC machines follow a script devoid of unpredictability. Any potential deviation is considered and addressed in the programming phase, guaranteeing a consistent and precise outcome.
Reducing Human Intervention to a Minimum:CNC programming minimizes the need for constant human intervention during the machining process. Once the code is set, the machines operate autonomously, adhering to the predetermined script with a level of consistency that surpasses the variability introduced by manual control.
Unveiling Automation: Unveil the beauty of automation in CNC programming, where the role of human operators transitions from constant supervision to overseeing the broader aspects of the manufacturing process. This reduction in manual intervention not only enhances precision but also improves overall efficiency.
Open/Closed-Loop Machining Systems: Precision Redefined
Position control in CNC manufacturing takes center stage with open or closed-loop systems. In this section, explore the distinction between these systems, understanding how closed-loop systems, by receiving feedback, enhance error correction. This precision is imperative for industries like metalwork, where irregularities in velocity and position are meticulously rectified.
In the realm of CNC machining, where precision is paramount, the distinction between open and closed-loop systems takes center stage. Precision, or the degree of accuracy in machining processes, becomes a critical factor in determining the quality of the final product.
Understanding CNC Machining Accuracy:
CNC machining accuracy refers to the ability of the system to consistently produce parts with tight tolerances and minimal deviation from the intended design. It's the holy grail for industries where the slightest error can lead to significant consequences.
Closed-Loop Machining Systems:
Closed-loop systems operate with a feedback mechanism, constantly receiving data from sensors that monitor the machine's position, velocity, and other relevant parameters. This real-time feedback allows for immediate adjustments, ensuring that any deviations from the programmed path are corrected promptly.
Role in Machining Accuracy: Closed-loop systems excel in maintaining accuracy by actively compensating for errors. Whether caused by temperature variations, tool wear, or external forces, the closed-loop system detects these deviations and makes instantaneous adjustments, resulting in precise and consistent machining.
Open-Loop Machining Systems:
In contrast, open-loop systems operate without continuous feedback during the machining process. The system relies solely on the programmed instructions without actively monitoring and adjusting to real-time data.
Role in Machining Accuracy: While open-loop systems are efficient in many applications, they may lack the precision demanded by industries where tight tolerances are non-negotiable. The absence of feedback means that any deviation from the ideal conditions may go unnoticed until the machining is complete, potentially affecting the final product's accuracy.
Understanding the role of closed and open-loop systems in CNC machining accuracy is crucial for industries where consistency and reliability are paramount. Closed-loop systems, with their ability to adapt on the fly, redefine precision in machining, ensuring that the end result aligns perfectly with the intended design. This level of accuracy is a game-changer in fields such as aerospace and medical manufacturing, where components must meet stringent specifications.
CNC Machining Automation: From Concept to Creation
Automation is the heartbeat of CNC machining. Witness how, in contemporary protocols, parts production becomes an automated symphony orchestrated by pre-programmed software. With computer-aided design (CAD) conceptualizing intricate drawings and computer-aided manufacturing (CAM) translating them into CNC-executable code.Automation is the heartbeat of CNC machining, orchestrating a seamless transition from design concepts to tangible creations.
Conceptualization with Computer-Aided Design (CAD):
The journey begins with the conceptualization of a design idea using Computer-Aided Design (CAD) software. Engineers and designers create intricate 2D and 3D models, defining every detail of the desired product. This digital representation serves as the blueprint for the upcoming manufacturing process.
CNC Integration: CAD designs seamlessly integrate into CNC systems, forming the basis for the subsequent automated machining. The precision and complexity of the design are translated into a language that CNC machines understand, setting the stage for the physical realization of the concept.
Translation with Computer-Aided Manufacturing (CAM):
Computer-Aided Manufacturing (CAM) takes the digital design a step further by translating it into CNC-executable code. CAM software generates the necessary instructions, including toolpaths, speeds, and feeds, ensuring that the CNC machines can execute the design with utmost accuracy.
CNC Integration: The CAM-generated code becomes the language spoken by CNC machines. It dictates the movements and operations required to transform raw materials into the envisioned product. This automation reduces the potential for human error and ensures consistency in manufacturing.
Precision Machining:
With the CNC machine armed with the coded instructions, precision machining comes into play. Whether it's milling, turning, cutting, or additive manufacturing processes like 3D printing, the CNC machine executes each step with meticulous accuracy.
Role of CNC Automation: CNC automation ensures that every cut, every movement is in perfect alignment with the digital design. The speed, feed rates, and tool changes are all orchestrated seamlessly by the pre-programmed instructions, guaranteeing a high level of precision and repeatability.
Quality Assurance and Iteration:
The automation process doesn't end with the physical creation of the product. CNC machining allows for integrated quality assurance steps, where the manufactured part can be measured and inspected against the digital design. Any deviations can trigger automated adjustments for subsequent iterations.
CNC Integration: The closed-loop nature of some CNC systems further enhances this process. Feedback mechanisms can identify discrepancies during machining, enabling real-time corrections for unparalleled precision.
From the initial spark of an idea in a designer's mind to the tangible creation produced by CNC machines, this automated journey is a testament to the efficiency and precision of modern manufacturing. CNC machining bridges the gap between concept and creation, making what was once a design concept into a physical reality with unmatched accuracy.
Different Types of CNC Machines: A Panorama of Precision Tools
Embark on a journey through the evolution of CNC machines. From the early days of numerical control to the contemporary realm of fully electronic systems, this section unveils the diversity of CNC-operated processes. CNC mills, lathes, plasma cutters, electric discharge machines (EDM), and water jet cutters take center stage, each with its unique role in the manufacturing orchestra.
Mastering Machine Diversity: Uncover the capabilities of various CNC machines and understand their roles in different industrial applications. This knowledge is invaluable for businesses seeking the right CNC tool for their specific needs.
CNC Mills:
These machines are the workhorses of CNC manufacturing, capable of performing a variety of tasks such as drilling, cutting, and complex 3D contouring. Vertical mills and horizontal mills offer versatility in different applications.
CNC Lathes:
Lathes are masters of turning and shaping cylindrical parts. They excel in creating symmetrical components, making them indispensable in industries like automotive and aerospace for crafting precision components.
Plasma Cutters:
Ideal for cutting through electrically conductive materials like metal, plasma cutters use a high-velocity jet of plasma to achieve accurate and clean cuts. They're often employed in industries requiring metal fabrication.
Electric Discharge Machines (EDM):
EDM machines use electrical discharges to shape and mold materials, particularly metals. They are crucial in producing intricate parts with tight tolerances and are preferred when traditional cutting methods are impractical.
Water Jet Cutters:
Harnessing the power of high-pressure water mixed with abrasive particles, water jet cutters excel in precision cutting of various materials, including metals, ceramics, and composites. Their versatility makes them suitable for a wide range of industries.
Versatility of CNC Machines: Crafting Excellence Beyond Expectations
CNC machines are not confined to traditional processes. From aerospace parts to automotive components, wooden decorations, and plastic consumer goods, CNC machines showcase their prowess in crafting products with unmatched detail.
Departure from Traditional Processes:
Unlike traditional manufacturing methods that rely heavily on manual labor and fixed processes, CNC machining ushers in a new era of precision and automation. It departs from the limitations of human-operated machinery, introducing a level of accuracy and repeatability that was once unimaginable.
CNC Advantages: CNC machines operate with pre-programmed instructions, translating digital designs into tangible products with meticulous precision. This departure from traditional processes minimizes errors, enhances efficiency, and opens doors to a broader range of manufacturing possibilities.
Versatility in Material Processing:
CNC machining is not confined to a specific set of materials. Whether it's metals, plastics, composites, or even exotic materials, CNC machines exhibit the versatility to handle a diverse range of substances.
CNC Applications: This versatility enables CNC machines to be applied across various industries. From aerospace components to automotive parts, wooden decorations to plastic consumer goods, CNC machining adapts seamlessly to the unique properties of different materials, crafting products with unmatched detail and accuracy.
In the dynamic landscape of manufacturing, CNC machining emerges as a transformative force, distinct from traditional processes. Its unparalleled versatility redefines what's possible, crafting excellence beyond expectations.
Choose GD-HUB CNC Machine Works: Your Trusted Partner in CNC Manufacturing
The journey culminates with a call to action. GD-HUB Machine Works emerges as a beacon in the CNC manufacturing landscape, backed by over 15 years of industry experience and a team of CNC-certified experts. Explore the precision machine services offered by GD-HUB, emphasizing our personalized solutions tailored to meet the unique needs of every client.
GD-HUB CNC Machine Works - Elevate Your CNC Manufacturing Experience with Precision and Expertise.
Featured Product
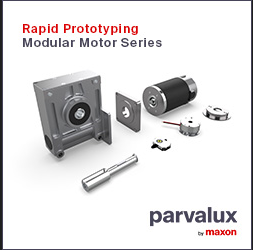
Rapid Prototyping with the Modular Motor Series
Quick to configure. Quick to build. Quick to deliver. Parvalux understands the importance of getting product in the hands of customers quickly and efficiently. The Modular Range does just that allowing customers to configure their own solution, selecting motor and gearbox, adding encoders and brakes to create a solution perfectly suited for their specific applications such as conveyor belt systems, picking systems, parcel sorting equipment, pallet shuttles and automated storage and retrieval systems (ASRS). Read our modular range guide for specifics.