3DPRINTUK ATTAINS CERTIFIED CARBON NEUTRAL STATUS
Thanks to its partnership with Climate Partner, 3DPRINTUK has gained a better understanding of its carbon footprint and identified ways to reduce it. The company has also been able to offset the emissions that it can’t eliminate through its current carbon reduction programme.
(9th August 2023, London, U.K.) Earlier this year, 3DPRINTUK announced its commitment to a sustainable approach to its additive manufacturing (AM) operations and outlined its "Road to Net Zero" plan. Today, the company is thrilled to announce that it has already taken a significant step towards this goal by attaining certified carbon neutral status, the first 3D printing service bureau to do this in the United Kingdom.
Thanks to its partnership with Climate Partner, 3DPRINTUK has gained a better understanding of its carbon footprint and identified ways to reduce it. The company has also been able to offset the emissions that it can't eliminate through its current carbon reduction programme.
Through this collaboration, 3DPRINTUK has been able to offset an impressive 448,000 kg CO2, equally split between two supported projects: improved cookstoves in Uganda and wind energy in De Aar, South Africa. Both projects contribute to the UN Sustainable Development Goals (SDGs) and have been verified by Carbon Check (India) Private and TUV SUD South Asia Private Limited, respectively.
The improved cookstoves Uganda project aims to replace conventional and less efficient cookstoves in the country with improved cookstoves. Three objectives are being pursued: reducing fuel consumption, improving the health of the population in Uganda, and reducing deforestation.
The aim of the wind energy project in De Aar, South Africa is to harness the region's wind energy potential to balance its energy needs in a sustainable way. The share of electricity now supplied by the wind farm would have otherwise been generated by fossil fuels. The wind power project avoids about 433,920 tonnes of CO2 emissions per year. In addition to the environmental benefits, the project assists the local community by creating jobs and improving the access to healthcare.
Commenting on this significant milestone, 3DPRINTUK CEO Nick Allen says, "We were very serious when we made the announcement about our Road to Net Zero initiative. We set ourselves some important goals as a leading 3D printing service provider, with the full intent to meet them as soon as practicably possible. Offsetting our carbon footprint and achieving certified carbon neutrality is a really great start, and we are proud of this achievement, but it remains just the start. We push on."
www.3dprint-uk.co.uk
ENDS
ABOUT 3DPRINTUK
3DPRINTUK are specialists in low volume production using state-of-the-art powder bed fusion (PBF) 3D printing systems with polymer materials. The company bridges the void that exists between prototyping and injection moulding, such that if tooling costs are prohibitively expensive for an application that does not require the volume demanded by injection moulding, 3DPRINTUK can provide a high quality, cost-effective and fast solution.
3DPRINTUK has mastered the process of 3D printing with polymer powders, with no need for support material, virtually no layer lines and short turnaround times. The company is an ideal partner for producing one-off prototypes through to production runs of tens of thousands of parts — on demand.
Featured Product
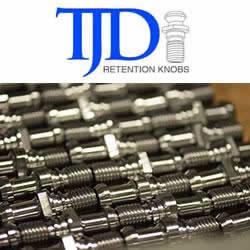