Carbon® Gen 2 Aligner Model Solution Brings Efficiencies to Aligner Manufacturers
Announced at IDS Conference: New, More Sustainable Production Solution Enables Significant Cost Advantages with up to 65% Increase in Throughput and Less Material Required Per Print
Carbon, the leading 3D printing technology company, announced today a new production solution that may enable clear aligner manufacturers to dramatically reduce cost per part while simultaneously increasing throughput. The Carbon® Gen 2 aligner model solution includes new proprietary software and high-performance resin that integrates with Carbon's existing printer hardware and aligner model workflow.
The Gen 2 aligner model solution will offer new and existing customers integration with Carbon's existing clear aligner workflow which is utilized by leading aligner manufacturers to produce millions of custom clear aligners globally each month. It consists of the Carbon L1 printer, solventless spin cleaning solution, as well as API-based software that automates the hollowing, nesting, and batching of models to be printed. Using software engineered in parallel with Carbon's new UMA 20 resin, Carbon's new production solution automatically hollows models, a revolutionary approach that creates a cost-effective and sustainable solution for clear aligner manufacturers. This new solution offers Carbon customers the potential to reduce material consumption by up to 40 percent per model while increasing throughput up to 65 percent with the Carbon L1 printer.
The Gen 2 aligner model solution offers aligner manufacturers new innovations while leveraging their current Carbon subscription and may lead to:
Decreased Cost Per Part: Cost per part is decreased by increasing throughput while simultaneously decreasing resin usage per part. Completely automated hollowing saves up to 40 percent of resin per part based on Carbon testing.
Increased Throughput: The automated hollowing software, paired with the UMA 20 resin, enables increased part throughput of up to 65 percent based on Carbon testing.
Improved Sustainability: Improved solvent-free model cleaning eliminates solvent waste and allows resin to be reclaimed for future use.
"Working with the top clear aligner companies has given us insight into the barriers this industry faces on a daily basis. We heard from customers and we took action to create efficiencies and cost savings in the clear aligner workflow," said Terri Capriolo, Senior Vice President, Oral Health at Carbon. "This new aligner workflow is designed to enable Carbon customers to reduce cost per part while simultaneously improving model throughput with a more sustainable production process."
The Carbon® Gen 2 aligner model solution will be available to customers in the second half of 2023. It will be showcased at the IDS Conference, a leading global trade fair for the dental community, taking place in Cologne from March 14-18, 2023. For additional information please visit: https://www.carbon3d.com/industries/clear-aligners.
About Carbon
Carbon is a 3D printing technology company helping businesses to develop better products and bring them to market in less time. The Carbon DLS™ process combines versatile printers, advanced software, and best-in-class materials to deliver functional parts with end-use performance and aesthetics, helping engineers and designers to create products that outperform expectations. From prototyping and low-volume production to production-at-scale, global organizations use the Carbon process to create a wide range of functional end-use parts and print them reliably wherever and whenever they need them through Carbon's production network partners. Carbon is a venture-backed company headquartered in Redwood City, CA. To learn more, follow Carbon on Twitter, LinkedIn and Facebook.
Featured Product
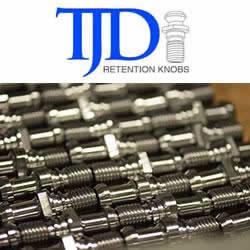