WAYLAND ADDITIVE RAMPS UP PRODUCTION AND INSULATES CUSTOMERS AGAINST SUPPLY CHAIN DELAYS
The company has also given some information about what initiatives it is taking to overcome and address the various supply chain issues that are bedevilling international industry in the wake of the pandemic.
(23rd February 2023 Huddersfiled, U.K.) Wayland Additive, creator of the Calibur3 metal AM machine featuring the Neubeam® process, has allowed a behind the scenes look at its production facilities. The company has also given some information about what initiatives it is taking to overcome and address the various supply chain issues that are bedevilling international industry in the wake of the pandemic.
Dan Rushton, Operations Manager at Wayland picks up the story, "We are having to cater for unprecedented demand for our ground-breaking metal AM technology at a time when industry globally is struggling with supply chain issues. We start from the position that all our operations need to be geared to customer satisfaction and the mitigation of risk, and so over the last period it has all been about ramping up production and placing orders for parts and components months and months in advance of when they will be needed. We have 6 machines in production right now catering for orders, and are pre-ordering enough components for a further 10 by the end of 2023, with plans for a further 24 in 2024 which will dramatically reduce the lead-times between customer interest and delivery. Effectively, on the continuum between ‘make to order' and ‘buy off-the-shelf ‘we are moving significantly towards the latter, which should reduce order to delivery to a matter of a couple of months."
Wayland's production initiatives and successes come at a time when typically, OEM machine providers are increasing their delivery times, in some instances quoting 18-24 months from order. Wayland appreciates that especially with a new and innovative technology like Calibur3 such a situation would be intolerable for customers, and has made significant investment in not just resourcing and allocating space for a larger production line area, but also in addressing bottlenecks in the sourcing of supply chain affected parts and components.
Rushton continues, "We are making significant investment in facilities and infrastructure at the moment. We have over the last few months doubled the size of our production facility, have added an inspection and workshop area, have installed an impressively large carrousel where all machine parts are sorted and stored, and working towards 2025 will boast a new applications centre and an R&D centre as well. Specifically in respect of supply chain issues, we have spent time and resource expanding the supply chains into new geographies, and building relationships on a global basis allowing us to tap into a much broader base of potential suppliers. As mentioned, we are also securing future stock through pre-orders and strong supplier relationships, which is only possible with a level of financial robustness that can carry the burden.."
Wayland's Calibur3 delivers on all of the advantages of metal electron beam (eBeam) powder bed fusion (PBF) technology, while overcoming the troublesome issues that have traditionally limited wider adoption. It produces fully dense parts in refractory metals such as tungsten and also highly reflective alloys, free from residual stresses and with reduced energy consumption, and opens up a raft of applications across a range of industry sectors hitherto unable to benefit from the use of AM as a production process.
This explains the huge interest in the technology, and shows why a concerted focus on streamlining production and supply chain issues at this time is hugely important for customers and Wayland alike.
About Wayland Additive
NeuBeam technology has been developed in-house from the ground up by a team of physicists that have worked for many decades with electron beam technology and industrial systems in the semi-conductor industry. The science, combined with extensive expertise and experience has allowed Wayland Additive to develop a very capable and reliable system rather than imitating existing systems or adapting off-the-shelf components and re-purposing them.
Featured Product
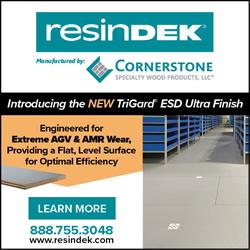