Smart Workforce Conference Reveals Job Requirements Essential for 4th Industrial Revolution
Smart Factory Institute Releases Findings in ‘New Collar’ Worker Job Requirements Report
CLEVELAND, Tenn. - The Smart Factory Institute of Tennessee hosted The Smart Factory Workforce Conference on December 8, 2022 at the Institute's manufacturing collaborative community space within the Partnerships in Industry and Education (PIE) Innovation Center in Cleveland, Tenn. The Conference drew in leading manufacturers and professional workforce organizations to discuss the transformational impacts of Industry 4.0 advancements as they relate to changes in the manufacturing workforce.
During the Conference, the Smart Factory Institute presented findings from its newly commissioned report, The "New Collar" Worker Job Requirements, researched and written by UC Foundation Professor of Psychology at the University of Tennessee Chattanooga (UTC), Dr. Chris Cunningham, and Scott Meyers, Graduate Research Scientist at UTC's Industrial-Organizational Psychology Master's degree program.
Through an intensive data-driven process, The "New Collar" Worker Job Requirements report unveils 60 critical knowledge, skill, ability, and other (KSAO) characteristics workers will need to succeed as the "smart workers" in future Industry 4.0 manufacturing settings. Many of these characteristics are not currently the norm in traditional factory environments. Some include: the need for technical and interpersonal forms of knowledge; skills associated with working well with others in complex environments to solve problems and move production processes forward; and higher-order knowledge and information processing skills such as operations monitoring, critical thinking, written communication, and systems analysis.
"In addition to adopting new KSAOs, many current manufacturing worker requirements are likely to persist and continue to be essential in Industry 4.0 settings," said Dr. Cunningham. "However, the ways in which current requirements and competencies are demonstrated will change due to disruptive technologies and processes that workers will have to use and follow while working, such as Internet of Things (IoT), machine-learning, virtual reality (VR), and artificial intelligence (AI)."
Access to the full report can be found here.
Following the featured presentation, graduate students from UTC's Industrial-Organizational Psychology Master's degree program participated in a focus group workshop exploring how manufacturers can accommodate non-traditional manufacturing workers such as women, disabled-workers, and Spanish speaking workers.
Additionally, Wes Wood, Workforce Partnerships Lead Southeast at Veryable, presented the ‘Labor Pool' model, which allows businesses to 'variablize' labor costs in small increments, enabling businesses to scale while maintaining a lower and more constant cost structure.
Two panel discussions closed out the Conference. Heather Canada Smith, VP of Human Resources, HR, Compliance & Admin, Shaw Industries, and Melanie Silva, Chief of Staff, Hinton and Company participated in the first discussion led by moderator, Kayla Shugart, Director of Development, United Way of the Ocoee Region. Titled "Business Leaders' Guide to Diversity and Inclusion," panelists examined the difficult challenge of securing and retaining talent in a tight labor market while simultaneously cultivating a more diverse and inclusive workforce.
The second panel was led by moderator Stephanie Linkous, CEO of United Way of the Ocoee Region, and featured Teri Cassem, Human Resources Director at WACKER, and Denise Rice, President & CEO, Peak Performance Inc. Titled, "Strategies to Enhance Your Talent and Capabilities," panelists discussed strategies to attract and retain manufacturing workers by emphasizing the ways in which workers can grow and flourish, including micro-credentialing, earn-and-learn programs, and opportunities to earn credentials.
"At WACKER, we understand that despite the increasing presence of machines and automation, the greatest projected workforce need is for human-centered technological skills," said Cassem. "These skills are quickly changing, and we must be ready to develop and train potential employees at all levels to meet the high demand for qualified workers in an Industry 4.0 future."
The event concluded with an exclusive tour of the PIE Innovation Center, including a look into new business retail, industry, manufacturing, and educational tenants in the mixed-use facility.
The Smart Factory Institute will hold its next signature event, the Automation, Maintenance and Reliability Summit, in February 2023. To purchase tickets or sponsor the event, contact Mary Beth Hudson at m.hudson@peakperformanceinc.com.
About Smart Factory Institute
The Smart Factory Institute is a business-driven effort guided by the Tennessee Manufacturers Association driving innovation and technology in Tennessee and the southeastern United States. The Institute, operated by Peak Performance Inc. and located at the Bradley County Partnerships in Industry and Education (PIE) Center, is an exclusive U.S. institute providing manufacturers with connections, collaborative relationships, and certifications for improving manufacturing processes by providing them with access to the latest technology in advanced manufacturing. The global network of Smart Factory Institutes by Deutsche Messe is comprised of leading companies and organizations in advanced manufacturing. For more information, visit www.smartfactoryinstitute.com.
About Peak Performance Inc.
Peak Performance Inc. is a workforce training and consulting firm specializing in incumbent worker training for the manufacturing industry, and operators of the Smart Factory Institute, serving businesses across the country from their headquarters in Cleveland, TN. Peak Performance equips its customers to transform their operational strategy through comprehensive, sustainable solutions in people and processes. Their services are unique, customizing the training to their client's needs, and using real-world simulations and instructors from the manufacturing industry. For more information, visit www.peakperformanceinc.com.
Featured Product
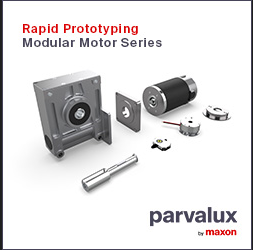