UltraFlex using induction to cut the preheat time for iron cast parts from 30 minutes to less than 2 minutes
The demo induction heating application set up by UltraFlex confirmed that by replacing oven heating with induction heating, the customer could achieve high-quality, repeatable and reliable results, while greatly reducing the heating process time and costs.
A recent demo application by UltraFlex Power Technologies showed how furnace heating can be efficiently replaced with induction heating, cutting down the heating time to less than 1/15th of the original one.
The heating scenario for this application included heating iron cast molds weighing between 30 and 50 pounds each (13.6-22.7 kg). The molds had to be evenly heated to 356°F (180°C), in order to be used for molding rubber.
The heating process for the parts, at that moment, used an old furnace technology, and took more than 30 minutes. By using induction, the customer was looking to cut down the heat time and energy costs significantly, along with improving the quality and reliability of the heated parts.
For this heating scenario, UltraFlex engineers recommended the use of an induction heater from the UltraFlex UltraHeat SM series. UltraHeat SM are compact and easy-to-use 5kW induction heating systems. They are reliable, modular systems, easy to tune to a wide range of loads and coils. To confirm that the required temperature had been reached during the heating, tempilaq paint had been used.
At a power output of 5 kW, it took less than 2 minutes to reach the target heating temperature of ~200°C for the heated parts. This short heating time proved that by using induction, the customer would be able to increase productivity, while significantly reducing his energy costs. At the same time, the digital control of the heating process would ensure a high quality, repeatable process, with no dependency on the operator skills.
After evaluating the test results, UltraFlex engineers also recommended improvements that would further optimize the process when transferred to the production line - for example, the use of a more powerful induction heating machine like the new UltraFlex unit SOLO 32W - 25/32kW power supply, along with a specifically designed custom coil.
The demo induction heating application set up by UltraFlex confirmed that by replacing oven heating with induction heating, the customer could achieve high-quality, repeatable and reliable results, while greatly reducing the heating process time and costs. He would also achieve a green and safe process, due to the lack of open flame and noxious emissions.
Find out more at:
https://ultraflexpower.com/
Contact us at:
+1.631.467.6814
uptnews@ultraflexpower.com
Svetla Markova
About UltraFlex Power Technologies:
UltraFlex Power Technologies (ultraflexpower.com) offers the most advanced and innovative digitally controlled induction heating equipment in the industry. Its compact modular and flexible systems are used for a wide variety of induction heating, casting and melting applications.
Featured Product
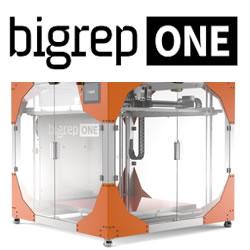
BigRep ONE: Large-Scale 3D Printing
The BigRep ONE is an award-winning, large-format 3D printer at an accessible price point. With over 350 systems installed worldwide, it's a trusted solution for prototyping and production by designers, innovators, and manufacturers alike. Featuring a massive one-cubic-meter build volume, the fast and reliable ONE brings your designs to life in full scale.