UltraFlex performing efficient induction annealing for steel and nickel parts
The efficient induction annealing for steel and nickel parts has recently been demonstrated by UltraFlex Power Technologies. The demo had been set up by UltraFlex per request of a customer from the manufacturing industry looking to evaluate the usage of both induction preheating and induction annealing in his manufacturing processes.
The efficient induction annealing for steel and nickel parts has recently been demonstrated by UltraFlex Power Technologies. The demo had been set up by UltraFlex per request of a customer from the manufacturing industry looking to evaluate the usage of both induction preheating and induction annealing in his manufacturing processes.
The customer sent two tube samples for induction heating evaluation - a large steel tube with size L150mm, OD16mm, ID10mm, and a small tube made of nickel alloy, with size L 121mm, OD8mm, ID 4mm, each of them split in two parts in the middle.
For this induction heating application, the customer required that 20 mm of the total length of the tubes be preheated for 7-8 sec, to a target temperature of 450°C, and this temperature maintained for 20 seconds. It was important to ensure uniform heating and reliable temperature maintenance.
For this induction heating scenario UltraFlex engineers recommended the use of an induction heater from the UltraFlex UltraHeat S series. UltraHeat S are small and efficient 2kW induction heaters that operate with a water-cooled or air-cooled remote heat station. All systems utilize the latest switching power supply technology and adaptive digital phase control, which efficiently operate in wide frequency ranges.
The efficiency of two different induction coils had been evaluated in this induction heating scenario. At kW of power, the preheat cycle for the smaller tube was accomplished within 7 seconds and for the bigger tube - within 8 seconds. The target temperature was then successfully maintained for the desired time of 20 seconds. The reach of the target temperature, as well as the maintenance of the temperature to no less than 427°C had been confirmed via tempilaq paint.
By using temperature profiles for the induction heating of both parts, the customer could automate this process and ensure repeatable and consistent results, with no dependency on the operator skills. Furthermore, if a custom induction coil is designed for the heating of each tube, the heating process efficiency could be increased even more.
Finally, thanks to the lack of open flame and noxious emissions, this heating process would be completely safe - safe for the operator and for the environment.
Find out more at:
https://ultraflexpower.com/
Contact us at:
+1.631.467.6814
uptnews@ultraflexpower.com
Svetla Markova
About UltraFlex Power Technologies:
UltraFlex Power Technologies (ultraflexpower.com) offers the most advanced and innovative digitally controlled induction heating equipment in the industry. Its compact modular and flexible systems are used for a wide variety of induction heating, casting and melting applications.
Featured Product
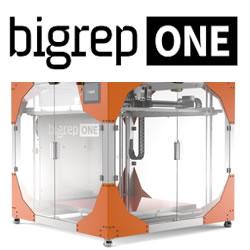